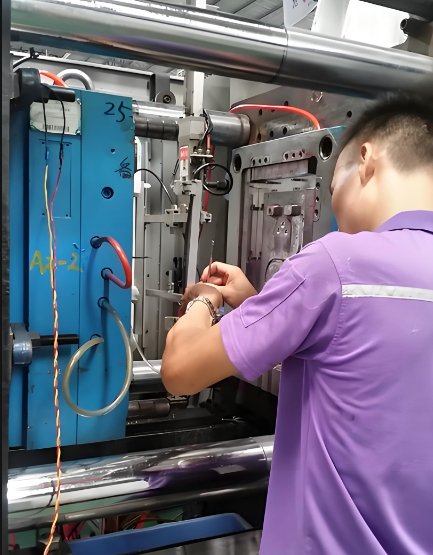
In injection molding, quick and efficient mold changes are vital. They reduce downtime and increase production. Injection mould companies focus on speed. Mold makers can design molds to improve efficiency. In this article, we will explore ways to enhance mold changing processes. The goal is to minimize downtime and maximize output.
Importance of Efficient Mold Changes
Mold changes are common in injection molding. When production switches between products, molds need to be changed. If the process takes too long, it affects productivity. Injection mould companies look for ways to shorten this time. A faster mold change means more products. This is critical for companies that handle various products. A mold maker plays a big role in making changes easier.
Use Quick Mold Change Systems
Quick mold change (QMC) systems are designed to save time. They allow for faster switching of molds. Many systems use clamps that can be adjusted easily. These clamps hold the mold securely. Traditional bolts take time to loosen and tighten. QMC systems reduce the need for manual adjustments. A good mold maker understands the value of QMC. They design molds to fit these systems.
Standardize Mold Base Design
Standardizing mold bases is another way to improve efficiency. When mold bases have similar designs, switching is easier. Standardization eliminates the need for major adjustments. Mold makers who design standardized bases help speed up the process. Injection mould companies should work with mold makers to create standard designs. This practice also reduces the chance of error.
Use Automatic Mold Changing Systems
Automation can further improve mold changes. Automatic systems allow for a completely hands-free process. These systems can remove one mold and replace it with another. The operator does not need to intervene. Automation reduces errors caused by manual handling. Mold makers can design molds specifically for automatic systems. An injection mould company can then benefit from faster changes.
Optimize Cooling Systems
The cooling system plays a large role in the mold change process. Traditional systems require time to cool down before molds can be changed. Optimizing the cooling system speeds up the process. Quick-release connectors help disconnect water lines quickly. Mold makers can design molds with these connectors in mind. This reduces the time spent on cooling and makes mold changes faster.
Reduce Downtime with Preheated Molds
Preheating molds can save time. When molds are preheated, there is no need to wait for them to reach the correct temperature. The mold is ready for production immediately. Preheating can be done outside of the machine while another mold is still in use. Mold makers should create molds that allow easy preheating. This can greatly benefit injection mould companies looking to reduce downtime.
Use Modular Molds
Modular molds are another solution. A modular mold can be divided into different parts. Instead of changing the whole mold, you can change just a section. This is especially useful for molds that produce multiple parts. A mold maker can design modular systems that make this possible. Injection mould companies can then swap sections instead of entire molds, reducing time spent on changes.
Implement a Preventive Maintenance Program
Preventive maintenance is key to efficient mold changes. Regular checks and maintenance help identify problems early. If a mold breaks during production, it can cause delays. Maintaining molds ensures they are always ready. A mold maker can provide guidance on the best maintenance practices. An injection mould company that follows a strict maintenance schedule reduces the risk of breakdowns. This leads to smoother mold changes.
Improve Operator Training
Operator skill affects mold change speed. Proper training helps operators work faster and more accurately. They should know how to use QMC systems and automated machines. Injection mould companies should invest in regular training. A well-trained operator can change molds faster and with fewer mistakes. Mold makers can also offer training to ensure their designs are used effectively.
Organize Workstations for Efficiency
A clean and organized workspace can speed up mold changes. Tools and equipment should be easily accessible. If operators spend time looking for tools, the mold change will take longer. Injection mould companies should focus on organizing their workstations. Mold makers can recommend the best tools to use. Proper organization saves time and reduces stress.
Improving mold changing efficiency is essential. Injection mould companies benefit from faster production and reduced downtime. Mold makers play a crucial role in designing molds that support quick changes. Solutions include quick mold change systems, standardizing mold bases, and using automation. Optimized cooling systems and modular molds also help. Preheating molds, preventive maintenance, and operator training further increase efficiency. In the end, every small improvement makes a difference. A focus on efficiency leads to better production results. Mold makers and injection mould companies should work together to implement these strategies.