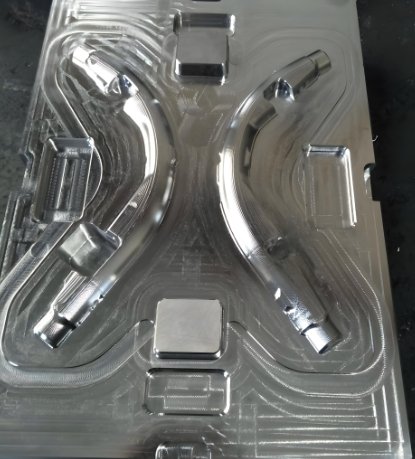
In today’s market, speed matters.
Electronic products must launch fast.
Delays can cost a lot.
That’s where rapid tooling helps.
It has changed how Electronic Injection Molding works.
It makes the process faster.
And it helps the Mold Maker deliver results quickly.
What Is Rapid Tooling?
Rapid tooling means fast mold making.
It uses soft materials or quick methods.
The goal is to cut time and cost.
It helps companies make test molds fast.
These test molds are often temporary.
But they are good for small runs or samples.
Traditional tooling takes weeks or months.
Rapid tooling can take just days.
This is a huge change for Electronic Injection Molding.
The Role of the Mold Maker
A Mold Maker is key to rapid tooling.
They choose the right material.
They design the mold carefully.
Speed matters, but quality matters too.
The Mold Maker must balance both.
They use fast machining or 3D printing.
They often work with aluminum or resin.
The Mold Maker also checks for issues.
They fix flow problems early.
This helps avoid mistakes later.
It saves time and cost.
Benefits of Rapid Tooling in Electronic Injection Molding
Rapid tooling offers many benefits.
It supports fast-paced industries.
And Electronic Injection Molding is one of them.
1. Faster Time to Market
Rapid tooling speeds up development.
It lets you test parts quickly.
You can launch products sooner.
In tech, this is a big win.
2. Lower Cost for Prototypes
Making a prototype mold used to be expensive.
Now it’s cheaper.
You can test before making final molds.
This reduces risk.
3. Easy Design Changes
Designs often change.
Rapid tooling allows updates fast.
The Mold Maker can tweak the mold.
There’s no long delay.
4. Supports Small Batch Production
Not all products need mass production.
Rapid tooling is perfect for small batches.
It keeps costs low.
And still offers high quality.
Common Materials Used
Rapid tools are made from different materials.
Each has pros and cons.
The Mold Maker selects the best fit.
1. Aluminum
It’s easy to machine.
It cools fast.
Great for 1000–5000 shots.
Perfect for testing.
2. Epoxy Resin
Used for very short runs.
Low cost.
Good for shape checks.
3. Steel (Sometimes)
Not common in rapid tooling.
But used if parts need more strength.
The Mold Maker may mix materials too.
Applications in Electronics
Electronic Injection Molding serves many industries.
Rapid tooling makes it even more flexible.
1. Device Prototypes
You can test device cases fast.
This helps check fit and feel.
Great for handheld tools or remote controls.
2. Connectors and Clips
Small parts can be tested quickly.
Rapid tooling lets teams evaluate function early.
3. Housings for Circuits
Circuit boards need protective shells.
You can mold these fast for testing.
Then move to final tooling later.
Challenges in Rapid Tooling
Rapid tooling isn’t perfect.
There are limits.
1. Limited Lifespan
Soft tools wear out.
They’re not for large-scale runs.
But they’re good for testing.
2. Lower Heat Resistance
Plastic types may be limited.
Not all tools can handle high heat.
3. Less Surface Finish
Final parts may need polishing.
The Mold Maker can improve finish, but it adds time.
How the Mold Maker Solves These Problems
A good Mold Maker knows the risks.
They plan ahead.
They pick the right tool type.
They test mold flow early.
They also monitor wear.
If a tool fails, they fix or remake it fast.
They also design with future changes in mind.
If you need to scale up, they are ready.
They can help shift from rapid to full-scale molds.
Future of Rapid Tooling in Electronic Injection Molding
Technology is moving fast.
Rapid tooling will get better.
3D printing is improving.
Machines are faster and cheaper.
This helps the Mold Maker even more.
Soon, full molds may be 3D printed.
Or at least the inserts.
This saves even more time.
And it opens new design ideas.
Software is also getting smarter.
It can predict problems before making the mold.
This helps the Mold Maker work faster and safer.
When to Use Rapid Tooling
Rapid tooling is not for everything.
But it fits many cases:
- Early prototypes
- Product testing
- Small batch runs
- Pilot production
- Short-term market testing
The Mold Maker can guide the choice.
They know when rapid tooling is best.
And when to switch to standard molds.
Combining Rapid and Traditional Tooling
Sometimes both are needed.
Start with rapid.
Test the part.
Then switch to hard tooling for large runs.
This reduces waste.
It also avoids late-stage design problems.
The Mold Maker can plan this path.
They set up for both fast start and long production.
Case Study: Small Device Launch
A tech firm wanted to launch a new device.
They needed a plastic housing.
But the design was not final.
They used Electronic Injection Molding with rapid tooling.
The Mold Maker created a test mold in five days.
They ran 500 samples.
The team tested size and fit.
They made changes.
Then they built the final steel mold.
The result?
Product launched in two months.
Faster than ever before.
Rapid tooling is a game-changer in Electronic Injection Molding.
It allows fast testing, lower costs, and quicker launches.
For small batches or early tests, it’s ideal.
The Mold Maker plays a key role.
They ensure quality, even at high speed.
As tools and machines improve, so will rapid tooling.
The future is faster, smarter, and more efficient.
With the help of a skilled Mold Maker, you can take full advantage of rapid tooling today.
Whether it’s a prototype or a small run, it’s the smart choice for modern electronic parts.