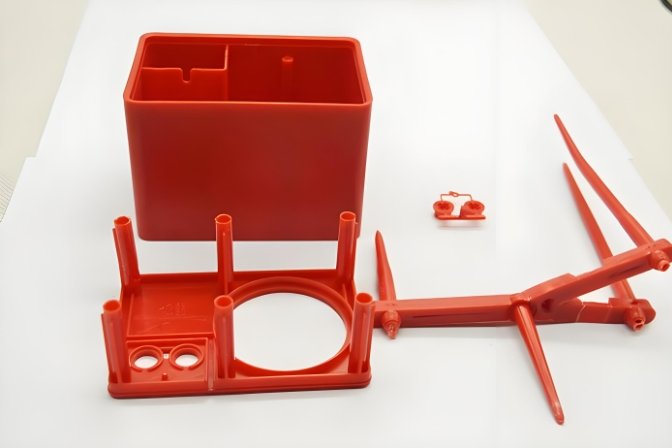
In today’s manufacturing world, housing injection molding is a critical process used to produce plastic housings for electronics, appliances, automotive parts, and more. These housings protect internal components and give products their outer shape. As demand for these products rises, manufacturers look for ways to make production faster, more precise, and cost-effective.
One powerful solution is robotics. Robots now play a major role in housing injection molding. They help with everything from part handling to inspection, packaging, and even machine maintenance. When used properly, robots can save time, reduce errors, and improve safety.
Of course, this level of automation only works well if the mold is designed to support it. That’s where a skilled mold maker comes in. A great mold maker understands how to design molds that work with robots to deliver excellent performance and long-term durability.
Let’s explore how robots help in housing injection molding and why a trusted mold maker is key to success.
Robots Improve Speed and Efficiency
One of the biggest reasons to use robots in housing injection molding is speed. Robots can:
- Load inserts into the mold
- Remove molded parts quickly
- Stack or place parts on conveyors
- Prepare the mold for the next cycle
These actions happen fast—often in just a second or two. Humans can’t match this speed. By reducing time between molding cycles, robots increase output.
However, not all molds can support this. A mold maker must design the mold to allow easy access for robot arms. That includes:
- Clear part release from the mold
- Room for the robot to move
- Fast, consistent ejection
A good mold maker knows how to do this without affecting part quality or cycle time.
Consistent Part Quality
In housing injection molding, product quality is critical. Small flaws in the plastic housing can cause problems during assembly or use. Robots help avoid these issues.
Because robots move with precision, they handle parts the same way every time. This reduces:
- Scratches or dents during part removal
- Incorrect placement on conveyors or trays
- Variation caused by human handling
Also, robots can check parts using vision systems. If a part has a defect, the robot removes it before it reaches the next stage.
A smart mold maker will design the mold and part to make visual inspection easy for the robot. That includes flat surfaces, defined edges, and visible quality marks.
Robots Improve Safety
Molding machines are hot, heavy, and dangerous. When people work close to these machines, the risk of injury is high.
Robots take over the dangerous tasks. They:
- Remove parts from hot molds
- Move parts away from machines
- Reduce the need for workers to reach into the press
With robots handling these steps, workers stay safe. They can focus on safer, skilled tasks like quality checks and machine monitoring.
For safety to work smoothly, the mold maker must design the mold with sensors and safety systems that work with robotic controls.
Lower Labor Costs and Higher Output
Robots don’t get tired. They work 24/7 without breaks. This lets manufacturers run housing injection molding machines day and night.
Over time, this reduces labor costs and increases part output. With fewer people needed to run the line, factories become leaner and more efficient.
Still, robots are not plug-and-play. The mold maker must build molds that are strong and consistent. The mold must run smoothly even after thousands of cycles.
A top-level mold maker uses hardened steel, quality cooling channels, and precision machining to keep the mold running with robots for years.
Robots Help with Insert Molding
In housing injection molding, many parts require inserts—metal or plastic pieces placed inside the mold before plastic is injected.
Robots help by:
- Picking and placing inserts
- Checking insert position with sensors
- Ensuring the mold closes only when inserts are in place
This makes insert molding fast and accurate. Manual loading often leads to errors or slow cycles.
The mold maker must design special guide pins, insert pockets, and sensors to support robotic insert molding. Without this, insert shifting or part failure can happen.
Robots Enable Smart Packaging
Once the housing is molded, it needs to be sorted, packed, or sent to the next process. Robots handle this too.
They can:
- Place parts into trays
- Stack them for box packaging
- Sort parts by cavity or barcode
- Move parts to painting or assembly areas
With this automation, the whole line becomes more efficient.
Again, the mold maker plays a key role. By designing a mold with cavity numbering, ejector pin balance, and part tracking, they make it easier for robots to sort and handle parts correctly.
Robots and Predictive Maintenance
Some advanced robots in housing injection molding use sensors to monitor mold performance. These include:
- Ejector stroke sensors
- Mold temperature sensors
- Pressure sensors
These robots can detect small changes that show the mold needs cleaning, lubrication, or part replacement. This prevents breakdowns and extends mold life.
For this to work, the mold maker must install the right sensor ports and wiring during mold construction. A forward-thinking mold maker builds the mold to fit future automation needs.
Collaboration Between Robot Integrators and Mold Makers
Robots don’t work alone. They need software, grippers, and layout planning. That’s why it’s important for robot integrators and mold makers to work together.
A strong mold maker will:
- Share 3D mold designs with robot engineers
- Adjust mold layouts to match robot reach
- Offer input on part orientation and stacking
- Allow robot access to ejector pins or cavity numbers
When the robot team and mold maker collaborate, the result is a clean, efficient production line.
Real-World Example
Consider a factory making TV remote housings. The product needs high gloss, precise shape, and tight screw holes.
Robots remove the part from the mold, check the surface with a vision system, then place it in a tray. Another robot stacks trays into boxes.
Thanks to the work of a skilled mold maker, the mold:
- Releases parts smoothly
- Leaves no gate marks
- Ejects parts evenly
- Allows visual access for the robot’s camera
With the mold and robots working together, the factory produces 5,000 parts per day with only two workers.
Final Thoughts
Robots are reshaping the world of housing injection molding. They bring speed, safety, and consistency to the process. But robots only succeed when paired with a high-quality mold.
That’s where the mold maker shines. A good mold maker understands robotic needs and builds molds that support automation from the start.
If you want your housing injection molding project to succeed in the modern age, work with a mold maker who thinks about robots, sensors, part flow, and long-term performance.
Together, robots and mold makers are building the future of smart, high-output plastic housing production.