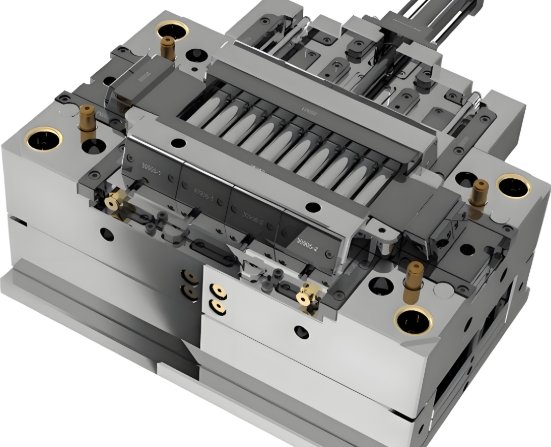
Efficiency is crucial in medical injection molding. Smart manufacturing is revolutionizing the industry. Mold makers are using automation, AI, and IoT to improve quality and reduce costs. These technologies increase productivity while maintaining compliance with strict medical regulations.
What is Smart Manufacturing?
1. Definition
Smart manufacturing integrates AI, robotics, IoT, and real-time data analysis. It improves efficiency in medical injection molding.
2. Why It’s Important
- Reduces defects and waste.
- Speeds up production cycles.
- Ensures compliance with FDA and ISO regulations.
- Lowers overall manufacturing costs.
Key Smart Manufacturing Technologies in Medical Injection Molding
1. AI-Powered Quality Control
- Uses machine learning to detect defects in real time.
- Reduces errors by automatically adjusting molding parameters.
- Ensures consistent production of high-quality medical components.
2. IoT-Connected Injection Molding Machines
- Sensors monitor pressure, temperature, and cycle times.
- Real-time data helps optimize performance.
- Reduces downtime by predicting machine failures before they occur.
3. Robotics and Automation
- Robotic arms handle material loading and part removal.
- Increases production speed while minimizing contamination risks.
- Reduces labor costs and improves precision.
4. Digital Twin Technology
- Creates a virtual model of the molding process.
- Predicts potential issues before production starts.
- Enhances mold design by simulating real-world conditions.
5. Predictive Maintenance Systems
- AI tracks mold wear and tear.
- Alerts mold makers before failures happen.
- Reduces machine downtime and extends mold lifespan.
How Smart Manufacturing Increases Efficiency
1. Faster Production Cycles
- Automated systems speed up injection molding processes.
- AI optimizes cycle times for maximum efficiency.
- Reduces lead times for medical device manufacturing.
2. Improved Material Usage
- Smart systems minimize material waste.
- AI predicts the exact amount of plastic needed for each part.
- Reduces costs and supports sustainable manufacturing.
3. Higher Product Consistency
- Smart sensors ensure every part meets exact specifications.
- Eliminates human error in quality control.
- Maintains compliance with strict medical industry standards.
4. Lower Energy Consumption
- Smart machines adjust energy use based on demand.
- Servo-driven motors reduce power consumption.
- Improves sustainability while cutting operational costs.
5. Real-Time Production Monitoring
- IoT systems provide instant data on production performance.
- Manufacturers can make immediate adjustments.
- Ensures smooth operations and minimizes downtime.
The Role of Mold Makers in Smart Manufacturing
1. Designing High-Precision Molds
- Mold makers create advanced molds optimized for automation.
- Smart molds improve efficiency and reduce defects.
2. Implementing AI-Driven Mold Maintenance
- Predictive analytics track mold wear.
- Prevents unexpected breakdowns and production delays.
3. Using 3D Printing for Rapid Prototyping
- 3D-printed molds allow faster design testing.
- Reduces costs before full-scale production begins.
4. Enhancing Cooling Systems
- Conformal cooling channels improve mold temperature control.
- Reduces cycle times and improves part quality.
Challenges of Implementing Smart Manufacturing
1. High Initial Investment
- Upgrading to smart systems requires capital.
- Long-term savings outweigh the initial costs.
2. Integration with Existing Equipment
- Older machines may not support smart technology.
- Manufacturers must invest in IoT-compatible systems.
3. Data Security Risks
- Connected systems can be vulnerable to cyber threats.
- Strong cybersecurity measures are needed.
4. Employee Training
- Workers need training to operate and manage smart machines.
- Companies must invest in education and skill development.
Latest Innovations in Smart Medical Injection Molding
1. AI-Driven Process Optimization
- AI adjusts molding parameters for peak efficiency.
- Improves precision and reduces material waste.
2. Fully Automated Injection Molding Cells
- Robots manage the entire molding process.
- Reduces human intervention and contamination risks.
3. Blockchain for Supply Chain Transparency
- Tracks material sourcing and production data.
- Ensures compliance with medical industry regulations.
4. Cloud-Based Quality Control Systems
- Manufacturers can monitor production remotely.
- Improves efficiency and ensures real-time troubleshooting.
5. Energy-Efficient Smart Machines
- Uses AI to reduce power consumption.
- Supports sustainability efforts in medical manufacturing.
Future Trends in Smart Manufacturing for Medical Injection Molding
1. Fully AI-Controlled Factories
- AI will manage entire manufacturing plants.
- Smart machines will operate with minimal human supervision.
2. Personalized Medical Device Production
- AI will enable customized medical components at scale.
- Smart manufacturing will adapt processes to meet individual patient needs.
3. Sustainable Smart Manufacturing
- Green energy solutions will power smart factories.
- AI will optimize resources for zero-waste production.
4. Advanced IoT Integration
- Real-time data sharing between machines will improve efficiency.
- IoT will enable predictive analytics across the entire production chain.
5. Smart Cleanroom Technology
- Automated air filtration and sterilization will reduce contamination risks.
- AI-controlled environments will maintain ISO 14644 standards.
Smart manufacturing is revolutionizing medical injection molding. AI, IoT, and automation improve efficiency, reduce costs, and ensure product consistency. Mold makers play a vital role in developing advanced molds for smart systems. As technology advances, the future of medical molding will become even faster, safer, and more precise.