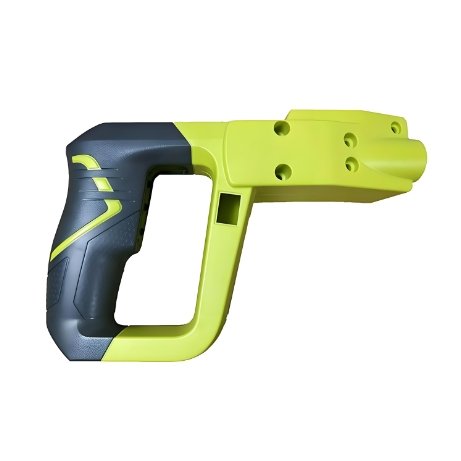
Designing plastic housings takes skill, knowledge, and planning. If done correctly, the housing will be strong, attractive, and easy to produce. If done poorly, the part might warp, crack, or cost too much. That’s why Housing Injection Molding is such an important topic in product development today.
This article will guide you through how to design plastic housings for injection molding. You will learn about proper wall thickness, draft angles, ribs, support features, and the important role of the Mold Maker in this process. Every point will help you make better, more efficient housings that are easier to mold and more durable in real-world use.
Understand the Basics of Housing Injection Molding
Housing Injection Molding involves shaping melted plastic inside a mold. Once cooled, the part takes on the exact shape of the mold. It’s fast, repeatable, and ideal for making strong plastic housings for electronics, appliances, machinery, and more.
The process depends heavily on good design. Every curve, hole, and thickness must follow the rules of injection molding. Without these, the part might not mold correctly. The Mold Maker also relies on your design to create a tool that fills evenly, cools quickly, and lasts long.
Keep Wall Thickness Uniform
Wall thickness is one of the most critical design elements in Housing Injection Molding. A good rule is to keep all walls as uniform as possible. Uneven walls cause uneven cooling, which leads to warping, sink marks, or internal stress.
Most housings use a wall thickness between 1.5 mm and 3 mm. If certain areas need to be thicker for strength, use ribs instead of making the walls thick. A skilled Mold Maker will advise you on what works best for the material and process.
Add Draft Angles
Every surface that touches the mold needs a slight angle, called a draft. This helps the part release from the mold after cooling. Without a draft, the part might stick, causing scratches or damage to both the housing and the mold.
Most vertical walls need a draft of at least 1 to 2 degrees. Larger surfaces might need more. A good Mold Maker will check your design and suggest the right amount of draft for your part’s shape and finish.
Use Ribs for Strength
Many housings need to be strong but also light. Ribs help with this. Ribs are thin walls added inside the housing to give it extra strength and stiffness. They support larger flat surfaces without adding too much plastic.
For best results, ribs should be no more than 60% of the main wall thickness. They should also have a draft and fillet at the base. Proper rib design reduces warping and makes Housing Injection Molding more stable. The Mold Maker will help you place ribs to avoid sink marks and ensure good mold filling.
Design Bosses for Fasteners
Most housings need bosses—cylindrical features that hold screws, clips, or pegs. These must be strong enough to hold together under stress. But they must also follow molding rules.
Keep boss walls thin and connect them to the rest of the housing with ribs or gussets. If bosses are too thick, they may cause sink marks. If too thin, they might crack. A good Mold Maker can advise you on ideal size, position, and support.
Avoid Undercuts When Possible
Undercuts are features that trap the part in the mold. These require slides or lifters, which increase cost and complexity. If possible, design your housing without undercuts.
If undercuts are needed for clips or latches, talk with your Mold Maker early. They will suggest the best way to mold the part without damage. Sometimes, the part can be redesigned to avoid the need for complex tooling.
Include Assembly Features
Plastic housings often come in two parts: a top and bottom. These must fit together perfectly. You can design snaps, slots, or screw holes for this.
During Housing Injection Molding, these assembly features must also follow draft and thickness rules. A good design ensures the housing can be assembled quickly and securely without damaging the part.
Choose the Right Material
The material you choose affects part strength, appearance, and moldability. Each plastic resin behaves differently during Housing Injection Molding.
Common housing materials include:
- ABS: Good strength, finish, and easy to mold
- Polycarbonate: Tough and impact-resistant
- Nylon: High strength and temperature resistance
- Polypropylene: Flexible and chemical resistant
A reliable Mold Maker can help match the right resin with your design needs.
Plan for Cooling and Ejection
Cooling time affects cycle time and part quality. Good design helps the mold cool the part evenly. Thick sections cool slowly, which increases time and cost.
Also, plan where ejector pins will push the part out. These must be placed on strong areas, not thin walls or cosmetic surfaces. Your Mold Maker will review the design and adjust pin location if needed.
Think About Mold Flow and Parting Lines
Plastic flows from the gate into the mold. Your part’s shape can make this easy—or hard. Long, narrow sections might not fill properly. Sharp corners can block flow. Thick areas can trap air.
A good design helps plastic flow evenly and fill the mold fully. You must also plan for the parting line—the place where the mold halves meet. Avoid placing this line across important surfaces.
Your Mold Maker uses mold flow software to check how plastic will move. Early design review helps fix problems before tooling begins.
Work with a Professional Mold Maker
Your choice of Mold Maker is just as important as your design. A professional Mold Maker will:
- Review your design for moldability
- Suggest changes that improve strength and reduce cost
- Build a precise, durable mold
- Use good steel and mold components
- Help with trial runs and first articles
The success of your Housing Injection Molding project depends on this partnership.
Final Tips for Better Housing Design
- Use radii instead of sharp corners to improve strength and mold filling
- Keep cosmetic surfaces smooth and consistent
- Avoid deep pockets or tall walls without support
- Design snap fits with care to avoid breakage
- Test prototypes before finalizing the mold
With these rules, your plastic housing will mold easily and perform well.
Designing a plastic housing for Housing Injection Molding takes careful thought and planning. Uniform wall thickness, proper draft, support features, and smart material choices are all key to success. A strong design reduces defects, lowers costs, and ensures your part functions as intended.
Most importantly, a trusted Mold Maker is your best partner. They turn your 3D design into a working mold that delivers part after part with consistency. Together, good design and expert mold making create a winning product.