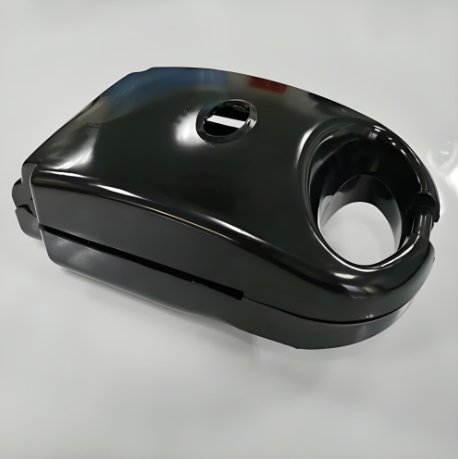
Short shots are a common issue in housing injection molding. A short shot occurs when the molten plastic does not completely fill the mold cavity, leaving incomplete or missing parts. This problem can delay production, waste material, and damage customer trust.
For a skilled mold maker, preventing short shots is part of producing reliable plastic housings. These defects must be understood from both a mold design and process control perspective. In this article, we explore the causes of short shots and give you clear, practical solutions to fix them.
Our goal is to help you achieve high-quality results in housing injection molding, reduce scrap, and improve overall efficiency.
What Is a Short Shot in Housing Molding?
A short shot means the injected plastic does not completely fill the mold cavity. In housing injection molding, this may show up as:
- Incomplete screw bosses
- Thin wall sections with gaps
- Unfilled corners or ribs
- Soft or weak areas on the part
This issue directly affects structural performance. Especially in consumer products or electronic housings, strength and appearance are key. If short shots persist, the mold maker and processing team must work together to solve the root cause.
Common Causes of Short Shots
Several factors can lead to short shots in housing injection molding. Let’s break them down into three main categories:
1. Material Issues
- Low melt temperature: If the plastic is not hot enough, it will solidify too early.
- High viscosity resin: Thick material may not flow far enough to fill thin sections.
- Moisture content: Wet resin can create steam and bubbles, blocking flow.
2. Machine and Process Settings
- Insufficient injection pressure: Not enough force to push plastic into all areas.
- Low injection speed: Slow fill can cause cooling before the mold is full.
- Inadequate shot size: The machine may not deliver enough plastic per cycle.
3. Mold Design and Mold Maker Errors
- Thin walls: Long, narrow sections can resist flow.
- Improper gate location: Plastic may not reach far corners of the mold.
- Poor venting: Air trapped in the cavity can stop the melt from flowing.
- Worn or damaged gates: Deformed gates can restrict flow paths.
These issues must be checked and corrected by a professional mold maker familiar with the challenges of housing injection molding.
Step-by-Step Solutions to Fix Short Shots
Here’s a step-by-step approach to solving short shot problems in housing injection molding:
Step 1: Raise the Melt Temperature
Ensure the plastic melts thoroughly.
- Increase barrel temperature
- Check nozzle temperature settings
- Use temperature sensors to verify consistency
Warmer plastic flows better into thin or complex shapes—especially important in tight housing designs.
Step 2: Increase Injection Pressure and Speed
This step boosts the force behind the plastic as it enters the mold.
- Raise first-stage injection pressure
- Increase injection speed
- Adjust holding pressure to maintain flow
Pressure and speed are key tools for any mold maker to combat short shots in housing molds.
Step 3: Dry the Resin Thoroughly
Moisture is a hidden enemy. Use a proper resin dryer before feeding material into the hopper.
- Dry as per material data sheet
- Monitor dew point of the dryer
- Use moisture analyzers for accuracy
This step is especially critical for polycarbonate and nylon used in housing injection molding.
Step 4: Check and Redesign Gate Size and Location
The mold maker should analyze whether the gate is in the right spot and is large enough.
- Move gate closer to unfilled areas
- Increase gate diameter or width
- Try multiple gates for large parts
Improper gating is a top cause of short shots in multi-featured housings.
Step 5: Improve Mold Venting
Air needs to escape for plastic to flow in.
- Add vents at the end of flow paths
- Clean or deepen existing vents
- Use vacuum venting if needed
Without vents, even perfect plastic will stop short. This is a detail every smart mold maker pays attention to.
Step 6: Use Flow Simulation Software
Simulate flow before steel cutting.
- Use mold flow analysis to predict short shots
- Identify cold zones, air traps, and weld lines
- Optimize gate and runner layout
This step saves time and money in housing injection molding, especially for high-volume parts.
Step 7: Review Part and Wall Design
Thin walls, sharp corners, and deep ribs resist flow. Adjust design when needed:
- Increase wall thickness in problem areas
- Use radii instead of sharp transitions
- Reduce rib depth or increase rib spacing
If a design change is impossible, ask your mold maker for an improved mold layout or temperature control.
Step 8: Check for Mold Wear or Damage
Molds wear out. This is often missed in old tools.
- Inspect gates, runners, and vents for wear
- Look for flash, parting line damage, or corrosion
- Resurface or refurbish worn inserts
A reliable mold maker does regular maintenance to ensure consistent housing injection molding quality.
Step 9: Confirm Shot Size and Cushion
The shot size must match the cavity volume.
- Verify cushion is present at end of fill
- Increase shot size if cushion is too small
- Check screw position during injection
An underfilled cavity is a direct path to short shots. Fix this by balancing machine and mold capacity.
Step 10: Use Proper Holding Time
Holding pressure keeps plastic flowing into shrinking areas as it cools.
- Increase hold time for thick parts
- Avoid premature packing cutoff
- Use gate freeze time as a guide
Holding too short results in shrink voids and short shots. In housing injection molding, appearance and strength both matter.
Prevention Tips for Future Projects
To prevent short shots from the beginning:
- Work with a skilled mold maker experienced in housing applications
- Use complete mold flow analysis in the design phase
- Choose materials matched to wall thickness and mold layout
- Use trial parts and test shots during tool qualification
A proactive approach is better than a reactive one in housing injection molding.
Conclusion: Solve Short Shots the Right Way
Short shots in housing injection molding are frustrating but fixable. The key is identifying the real cause—whether material, machine, or mold—and applying the correct solution.
With a skilled mold maker and a clear process, short shots can be eliminated. This leads to stronger parts, faster cycles, and happier customers.
To recap:
- Raise melt temperature
- Boost injection pressure and speed
- Dry the resin
- Redesign gates and vents
- Check wall thickness and mold health
By following these proven methods, you’ll produce complete, clean, and durable housings every time. In housing injection molding, the quality of your mold—and your mold team—makes all the difference.