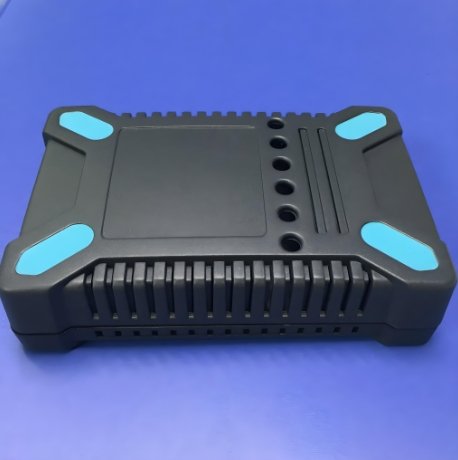
Ordering custom housing injection molding may seem complex at first. But when done right, it becomes a smooth and rewarding process. Many businesses—whether in electronics, medical devices, or automotive—rely on plastic housings to protect their products and shape their brand image. These housings must be accurate, durable, and cleanly finished.
Behind every high-quality plastic housing is a trusted mold maker who understands both the product and the production process. This guide will walk you through every step of ordering custom molded housings, so you can get the perfect results for your project.
Step 1: Define Your Product Requirements
Before contacting a supplier, you need to understand your product clearly. Define the size, shape, features, and functions of the housing. Ask yourself:
- What components will fit inside?
- Are there vents, slots, or ports required?
- What type of finish or color do you want?
- Will the housing be used indoors or outdoors?
- What are the strength, temperature, or chemical resistance needs?
These answers help the mold maker design the correct mold and suggest the right material for your housing injection molding project.
Step 2: Create or Collect 3D CAD Drawings
To start housing injection molding, you need a 3D CAD model of the housing. If you already have one, great. If not, many mold makers offer design services or can work with your concept to create the CAD files.
The 3D model is crucial. It includes all details like wall thickness, mounting holes, ribs, and snap fits. It also determines how the mold will be built.
An experienced mold maker will review your design and offer suggestions through a DFM (Design for Manufacturing) analysis. This ensures the design works well in real-world molding conditions.
Step 3: Choose the Right Material
Material choice affects strength, cost, appearance, and durability. Popular plastics for housing injection molding include:
- ABS – Tough and impact-resistant, with a good finish
- PC – Strong and clear, suitable for harsh environments
- PC/ABS blend – Combines strength and processability
- PA (Nylon) – High wear resistance
- PBT – Great for electrical housings
Your mold maker will guide you through the best choice based on your needs. For outdoor use, UV-stabilized materials might be required. For electronics, flame-retardant plastics are often essential.
Step 4: Find a Reliable Mold Maker
This is one of the most important steps. A good mold maker builds the tooling that creates your parts. If the mold is poor, the parts will be poor, no matter how advanced the machine is.
Look for the following qualities in a mold maker:
- Experience in housing injection molding
- Clean workshop and modern equipment
- Good communication in English
- Transparent pricing and clear lead times
- Ability to offer sample parts (T1 samples)
- Proven track record with international clients
Many businesses choose a mold maker in China due to the strong mix of quality and affordability. Top Chinese factories use advanced CAD/CAM tools, CNC machines, and follow ISO standards.
Step 5: Get a Quote and Confirm the Details
Once your design is ready and a mold maker is selected, request a detailed quote. The quote should include:
- Mold cost (one-time tooling fee)
- Unit price per part (based on order quantity)
- Lead time for mold building and sample approval
- Payment terms
- Shipping terms (EXW, FOB, DDP, etc.)
Be sure to clarify if the mold will be stored by the supplier or shipped to you. Some companies prefer to own and store their molds. Others let the mold maker keep them for future runs.
Step 6: Mold Design and Manufacturing
After you place your order, the mold maker will begin designing the mold. This includes:
- Core and cavity layout
- Gate and runner design
- Ejection system
- Cooling channel placement
- Mold base material selection
Once the mold design is approved by you, the mold maker will start machining the mold. This process typically takes 3–5 weeks depending on complexity. The mold is made using CNC machining, EDM, grinding, and polishing.
Step 7: T1 Samples and Testing
When the mold is ready, the mold maker will run a trial and send you T1 samples. This is the first set of molded parts. You should test the parts for:
- Fit with internal components
- Surface finish
- Dimensional accuracy
- Functionality
- Assembly compatibility
If changes are needed, the mold maker will adjust the mold and send a new batch. Once you approve the samples, mass production can begin.
Step 8: Mass Production and Quality Control
Now your housing injection molding project moves to the production phase. The mold is mounted on the injection machine, and production begins.
A good mold maker will have strong quality control procedures in place. This includes:
- First Article Inspection (FAI)
- In-process inspections
- Final inspection before shipping
Some clients request SPC (Statistical Process Control) for large-volume projects. Visual checks, functional tests, and dimensional reports help confirm consistency.
Step 9: Post-Processing and Assembly (Optional)
Depending on your needs, your mold maker may also offer post-processing services such as:
- Ultrasonic welding
- Printing or labeling
- Painting or coating
- Assembly and packaging
These services reduce your logistics and save time by keeping everything under one roof.
Step 10: Shipping and Delivery
Once the parts are approved and packed, the mold maker will arrange shipping. You can choose by air (faster) or sea (cheaper for large volumes). Make sure you receive tracking info, packing lists, and invoices for customs clearance.
Ongoing Support and Repeat Orders
A strong relationship with your mold maker is valuable. They will store your mold for future runs, help with design changes, and quickly deliver new batches.
If your demand grows, the mold maker can add more cavities to the mold or scale up production with more machines.
Summary
Ordering custom housing injection molding may involve many steps, but with the right approach, it’s simple and efficient. The key is to work with a trusted and skilled mold maker who understands your needs.
Here’s a quick recap of the process:
- Define your housing specs
- Prepare CAD drawings
- Choose the right material
- Find a reliable mold maker
- Get a clear quote
- Approve mold design
- Test T1 samples
- Start mass production
- Arrange shipping
- Repeat orders as needed
With these steps, your product can reach the market faster, with better quality and lower costs. Investing in professional housing injection molding and a capable mold maker is the smartest move you can make for your product success.