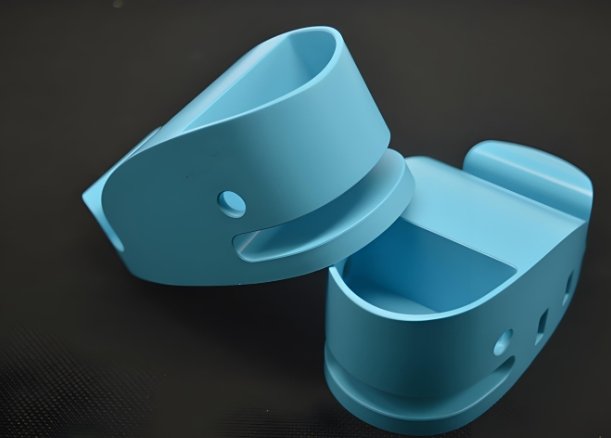
Plastic waste is a big problem.
It hurts the planet.
It costs money too.
In Electronic Injection Molding, waste adds up fast.
That’s why smart changes matter.
And every good Mold Maker plays a big role.
Why Plastic Waste Happens
Waste doesn’t just happen by accident.
Many causes create it.
Understanding them is the first step.
Poor Mold Design
If a mold is not right, it leaks.
Or it overflows.
This creates scrap plastic.
A skilled Mold Maker can prevent this.
Setup Errors
Wrong settings cause bad parts.
Temperature.
Pressure.
Speed.
Each one matters.
Mistakes cause waste.
Trial and Error
Testing new molds wastes plastic.
Every trial run adds to the bin.
Better planning can cut this waste.
Runner Systems
Old runner systems leave waste.
Cold runners need trimming.
That extra plastic is often thrown out.
Hot runners can help.
Role of the Mold Maker in Waste Reduction
The Mold Maker is not just a builder.
They are the waste fighter too.
They choose the right materials.
They design for low scrap.
They help factories run clean.
Smart Mold Design Reduces Waste
A good mold does more than shape plastic.
It saves material too.
Balanced Cavities
All parts fill at the same time.
No short shots.
No overflows.
Proper Venting
Good vents stop trapped air.
That means fewer defects.
And less waste.
Smooth Ejection
Parts pop out clean.
No cracks.
No sticking.
No broken pieces.
All these steps need a skilled Mold Maker.
Use Hot Runner Systems
Cold runners waste plastic.
That plastic must be trimmed and tossed.
Hot runners keep it molten.
No waste runners.
Only clean, full parts.
Many modern Electronic Injection Molding setups now use hot runners.
And top Mold Makers recommend them.
Use Recycled Materials
Don’t toss scrap plastic.
Use it again.
Some plastics allow regrind.
That means ground-up scrap gets used again.
With smart ratios, quality stays strong.
The Mold Maker helps plan this.
They guide material mixing.
They test the results.
Use Scientific Molding Methods
Guessing creates mistakes.
And mistakes waste plastic.
Scientific molding uses facts.
It sets the best pressure.
The right heat.
And perfect speed.
This process makes repeatable results.
It lowers scrap rates.
And saves time.
A good Mold Maker supports this process.
They test molds with real data.
Not just feel.
Monitor and Adjust
Even the best setups drift.
Over time, machines change.
That creates small errors.
Which lead to big waste.
Use sensors.
Track part quality.
Check temperatures and cycle times.
React fast.
Fix small issues before they grow.
That’s how modern Electronic Injection Molding stays clean.
Train Your Team
People make mistakes.
But trained people make fewer.
Teach workers how molds work.
How to set machines.
And how to spot defects early.
This stops bad parts.
And saves plastic.
Your Mold Maker can help train.
They can explain how the mold works.
And show best practices.
Choose Better Materials
Not all plastics are equal.
Some flow better.
Some cool faster.
Some are more forgiving.
A skilled Mold Maker knows this.
They pick the right plastic.
That means fewer rejects.
And less wasted plastic.
Make Lighter Parts
Use only what you need.
Don’t overbuild parts.
Thin walls save plastic.
Strong ribs can add support.
Smart design saves weight.
Your Mold Maker can help here too.
They know where to reduce thickness.
Without losing strength.
Consolidate Parts
Too many parts means more molding.
More tools.
More waste.
Combine parts when possible.
One big mold instead of two small ones.
Fewer joins.
Less scrap.
This cuts plastic use.
It speeds up assembly too.
Use High-Cavity Molds
More parts per shot means less waste.
Less runner material per part.
Better cycle use.
More parts.
Less scrap.
This is perfect for Electronic Injection Molding.
Mass production gets more efficient.
Only a skilled Mold Maker can design high-cavity molds well.
They make sure each cavity works the same.
Improve Quality Control
Catch problems early.
Use cameras.
Use sensors.
Check dimensions.
Check color and finish.
If a part is bad, stop the line.
Fix the issue fast.
Don’t wait to see a bin full of bad parts.
Reuse and Recycle Internally
Don’t throw scrap away.
Grind it.
Mix it.
Reuse it.
Even runners can be reprocessed.
As long as quality allows.
The Mold Maker can help with this too.
They choose materials that support recycling.
Clean Machines Regularly
Dirty machines leak.
They clog.
They mess up flow.
That leads to bad parts.
Clean machines stay sharp.
They mold better.
They waste less.
Track Your Waste
Don’t guess.
Measure.
Track:
- Rejected parts
- Runner scrap
- Setup waste
- Cleaning waste
This shows where the problems are.
Fix the worst ones first.
Over time, reduce all waste.
Many Electronic Injection Molding factories use software to track this.
And the best Mold Makers support that system.
Set Goals and Improve
No system is perfect.
But every one can improve.
Set a waste goal.
Share it with the team.
Work with your Mold Maker to meet it.
Each month, check your progress.
Reward success.
Try new ideas.
Soon, waste goes down.
And profits go up.
Plastic waste hurts everyone.
It fills landfills.
It raises costs.
And it slows production.
Electronic Injection Molding must reduce waste.
Every smart factory knows it.
Every smart Mold Maker supports it.
Use better molds.
Choose smart systems.
Train your team.
Track your numbers.
Small changes matter.
Together, they make a big difference.
Cutting waste is not just green.
It’s smart business too.