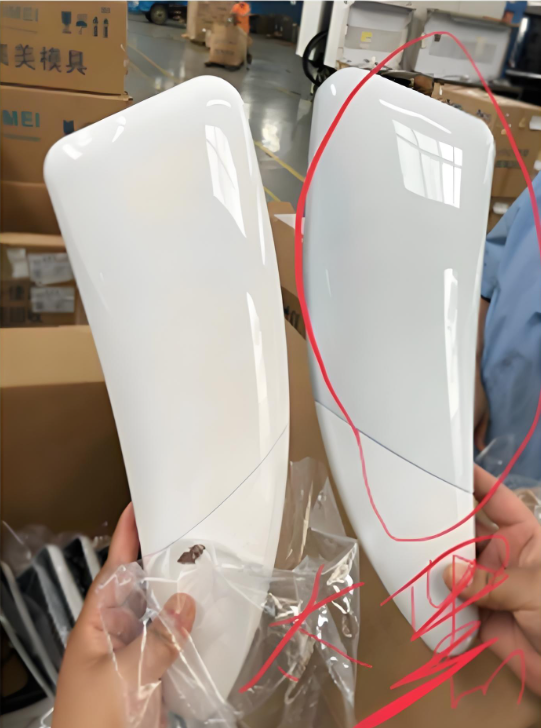
Color difference is a common problem in injection molding. It affects the appearance of products and may lower their quality. Solving this issue requires action in different areas of the process. In this article, we will discuss five key aspects that help solve color difference. These solutions will ensure your products have a consistent color.
1. Eliminate Machine and Mold Factors
The injection molding machine and mold can cause color differences. The machine’s stability plays a big role in producing consistent results. Check if the machine is working at stable temperatures, speeds, and pressures. Any fluctuation in these parameters can change the product’s color. The mold also needs to be in good condition. A mold with poor surface finish or incorrect size can change how the resin flows. This can lead to differences in color. If the machine or mold is not working well, it becomes hard to control color.
Regular machine maintenance is a good way to avoid problems. Check the mold for any damage, wear, or dirt. Fix these issues early to avoid costly rework later. Mold makers also need to ensure the mold design allows smooth resin flow. A mold with even flow channels prevents color changes caused by uneven resin distribution.
2. Eliminate the Influence of Resin and Masterbatch
The resin and masterbatch you use must be of good quality. Resin is the base material, while the masterbatch adds color. If either of these materials has poor quality, you will see color differences. Some resins may absorb moisture, which can change their color during molding. To avoid this, make sure the resin is stored in a dry place. Before using it, dry the resin to remove any moisture.
Masterbatch quality is also important. Different batches of masterbatch may have slight color differences. Always use masterbatch from a reliable supplier. Stick to the same batch for large production runs. This ensures all products have the same color.
3. Eliminate Uneven Mixing of Resin and Masterbatch
Uneven mixing of resin and masterbatch leads to color differences. This happens when the masterbatch is not evenly distributed in the resin. The uneven mix will show up as light or dark spots on the finished product. The best way to prevent this is by improving the mixing process.
Use the right mixing equipment to ensure even distribution of the masterbatch. Slow or poor mixing can create color variations in the molded part. Mixing at a stable speed and time helps solve this problem. You can also use pre-colored resin instead of masterbatch. Pre-colored resin has the color already mixed into it. This removes the risk of uneven mixing.
4. Reduce the Impact of Barrel Temperature
Barrel temperature is crucial in injection molding. If the temperature is too high or low, it will affect the color of the product. High barrel temperatures may cause the resin to overheat. Overheating changes the resin’s color, making it darker or lighter. On the other hand, low barrel temperatures may cause incomplete melting. This can lead to color inconsistencies.
To solve this, set the barrel temperature according to the resin type. Always follow the resin supplier’s recommendations. Monitor the temperature closely throughout the process. Keep the temperature stable to avoid sudden changes. Stability will ensure that the resin and masterbatch melt properly, resulting in consistent color.
5. Control Injection Molding Process Adjustment
Adjusting the injection molding process can affect color. When you change the injection speed, pressure, or cooling time, it may cause color differences. Small changes can affect how the resin and masterbatch behave. For example, higher injection speed might cause the product to appear darker. Lower cooling time might result in color streaks.
To reduce the risk of color difference, keep process adjustments to a minimum. Once you set the machine for a specific resin and masterbatch, avoid making frequent changes. If adjustments are necessary, make them gradually. Sudden or large changes in speed, pressure, or cooling can make it harder to achieve consistent color.
Color difference is a challenge for any injection mold maker. By addressing key areas, you can reduce or eliminate this issue. Start by ensuring your injection molding machine and molds are in good condition. Then, focus on using quality resin and masterbatch. Make sure that both are mixed evenly to avoid color streaks. Set the right barrel temperature and maintain it throughout the process. Finally, be cautious when making adjustments to the injection molding process.
By following these five steps, you can produce high-quality injection-molded products with consistent color. This will improve the appearance and overall quality of your products. In turn, you’ll gain the trust of your customers. Injection molding is a complex process, but solving color difference doesn’t have to be. Consistency is key to achieving excellent results.