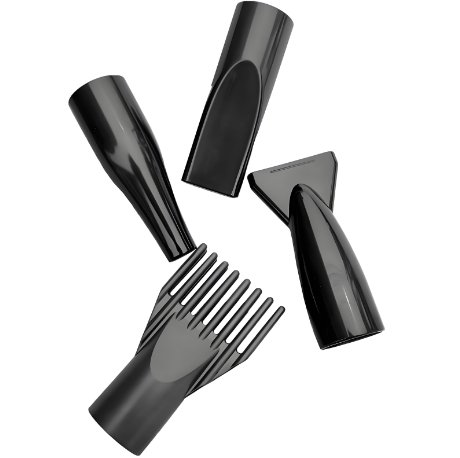
When it comes to plastic enclosures, every product begins with a plan—and often, tight deadlines. Whether you’re launching a new electronic device or updating a tool casing, speeding up your housing injection molding project without compromising quality is essential. Time lost in mold design or production can mean missed deadlines and lost revenue.
This article will guide you through practical steps to move faster, from concept to finished parts. The key lies in smart planning and strong teamwork with your mold maker.
Start with a Clear Design
One of the best ways to speed up your housing injection molding project is to begin with a clean and finalized 3D design. A detailed CAD model with all dimensions, tolerances, and part features ensures that your mold maker doesn’t waste time fixing unclear specifications.
Tips:
- Avoid last-minute changes after submitting your design
- Include draft angles for easy part release
- Minimize undercuts or complex parting lines
- Maintain uniform wall thickness
Every design improvement leads to faster toolmaking and better parts.
Work with an Experienced Mold Maker
Choosing the right mold maker is one of the biggest time-saving decisions you can make. An experienced mold maker has likely worked on many housing injection molding projects and knows the shortcuts that save time without hurting quality.
Benefits of working with the right partner:
- Accurate design for manufacturability (DFM) analysis
- Faster mold design turnaround
- Reliable lead time estimates
- In-house capabilities that reduce outsourcing delays
A professional mold maker can anticipate problems before they occur, making the process smoother and quicker.
Use Rapid Prototyping Early
Before committing to steel tooling, it helps to create a 3D printed or CNC-machined prototype of your plastic housing. This step verifies the fit, function, and look of your design.
Why this matters:
- You catch and fix design flaws before building the mold
- It reduces changes after tooling starts
- Your mold maker works with confidence on a proven design
Quick prototyping adds a few days upfront but can save weeks of rework later.
Choose the Right Mold Material
Tool steel grade affects both durability and lead time. For short production runs or fast-turn projects, using pre-hardened steel like P20 or aluminum molds can cut weeks off your schedule.
Ask your mold maker about:
- Aluminum molds for very short runs (fastest to machine)
- P20 steel molds for quick builds and moderate production
- H13 or S136 steel for high-volume molds with longer lifespans
Choosing the right material for your housing injection molding project ensures faster delivery without unnecessary expense.
Go with Modular or Standard Mold Bases
One smart way to reduce lead time is to use standard or modular mold bases. These bases are pre-made and stocked by many mold suppliers.
Your mold maker can then focus on cutting only the core and cavity inserts. This shortcut can save 1–2 weeks in tooling.
Advantages:
- Less machining needed
- Fewer design steps
- Faster mold assembly
This method is perfect for quick-turn housing injection molding jobs.
Approve Designs Quickly
Speed also depends on how fast you respond. Once your mold maker sends you the mold design for approval, review it promptly and return feedback as soon as possible.
Delays often happen when approvals sit unanswered. Clear, fast communication between you and your mold maker keeps the project moving forward.
Set a review timeline in advance to help both sides stay on track.
Reduce Mold Complexity When Possible
Complex mold features—like sliders, lifters, or hot runner systems—take more time to build and test. If your housing design allows, try to simplify it.
Work with your mold maker to:
- Avoid moving cores
- Remove unnecessary textures or inserts
- Stick to cold runner systems when high production isn’t needed
Simple molds are faster to produce and easier to maintain.
Combine Parts with Family Molds
If your plastic housing includes several parts, ask your mold maker if a family mold is possible. This mold type allows multiple components to be made in one cycle.
Advantages:
- Faster production
- Reduced mold count
- Lower total tooling cost
While it adds design complexity, a family mold can save a lot of time over separate molds.
Set Realistic Yet Firm Deadlines
Setting clear milestones and final deadlines helps keep the project on track. Work with your mold maker to create a timeline from design approval to final part delivery.
Use stages like:
- Design freeze
- Mold fabrication
- T1 trial
- T2 revisions
- Production launch
Having a detailed plan with buffer time reduces rush stress and supports better results.
Communicate Daily in Critical Stages
When your housing injection molding project enters tooling or testing, daily updates from your mold maker can make a big difference. Frequent communication allows issues to be solved quickly.
Use tools like:
- Video calls
- Shared folders (for CAD, QC reports, trial videos)
- Task tracking systems
A fast response loop prevents days of delay due to miscommunication.
Pre-Approve Materials and Colors
Waiting on material samples or color matches can stall a project. Discuss your resin choice and color options early. Ask your mold maker to source or pre-order materials while tooling is in progress.
Also consider:
- Using off-the-shelf resins instead of custom blends
- Using standard colors when fast delivery is needed
- Approving materials via digital samples (if possible)
Everything you can finalize ahead of mold trials saves valuable time.
Consider Overseas vs. Local Mold Makers
Some overseas mold makers—especially in China—can offer fast, affordable tooling for housing injection molding. However, shipping and customs may add delays.
Compare:
- Local makers: Easier communication, faster delivery, higher cost
- Overseas makers: Lower prices, sometimes longer lead times unless express options are used
If choosing an overseas mold maker, ask about:
- Express tooling options
- Air shipping instead of sea
- Local mold testing in your region
Find the balance that works for your deadline and budget.
Prepare for Production Early
Don’t wait for the mold to be done before planning production. Line up your packaging, assembly line, or final inspections early. Your mold maker can also help coordinate low-volume runs or send samples ahead of the full batch.
This parallel planning shortens the gap between mold completion and product launch.
Final Thoughts
Speed doesn’t have to mean risk. By working smartly with your mold maker and planning every step, you can reduce lead times without sacrificing quality. From design to delivery, every day counts in a housing injection molding project.
Remember:
- Clean design = faster mold making
- Clear communication = fewer delays
- The right mold maker = everything done better and faster
Partnering with a responsive, skilled mold maker gives your product a strong, timely start in the market. When you move fast and plan smart, you win.