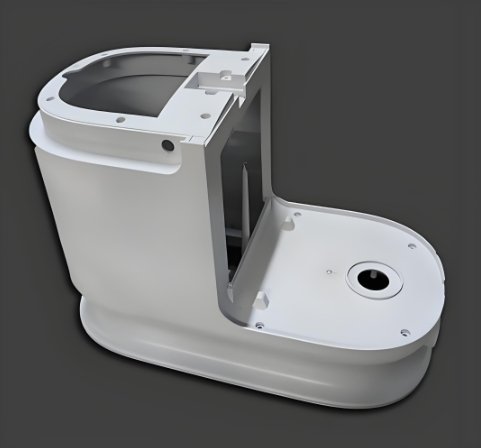
Electronic Injection Molding is key for creating durable electronic parts. Overmolding is a technique where one material is molded over another. This can improve functionality and appearance. But adhesion problems often arise.
Proper adhesion is crucial for the success of the overmolding process. A weak bond can cause failure. Let’s look at the challenges and how a skilled Mold Maker can solve them.
1. What Is Overmolding?
Overmolding is a process where a second layer of material is molded over an existing part. In Electronic Injection Molding, this is often done with plastics, rubber, or silicones.
The goal is to combine two materials into one part. These materials must bond strongly.
2. Why Adhesion Matters in Overmolding
Adhesion is the bond that holds the two materials together. In overmolding, if the bond is weak, parts can break apart. This can lead to product failure, especially in electronic devices.
For example, overmolded parts might be exposed to stress or heat. Without strong adhesion, the parts can separate, causing malfunction.
3. Material Compatibility
Not all materials bond well. When using Electronic Injection Molding, choosing the right materials is crucial. Some plastics, for example, are hard to bond with rubber.
A skilled Mold Maker helps select materials that bond better. They know which materials work well together. They also know which ones don’t.
4. Surface Preparation for Better Adhesion
Surface treatment is key for improving adhesion. If the surface is not prepared, the second material won’t stick properly.
The Mold Maker can use various techniques to prepare surfaces. For example, plasma treatment or chemical etching increases surface roughness. This makes it easier for the second material to bond.
5. Choosing the Right Injection Pressure
Injection pressure is critical in the overmolding process. Too much pressure can push the material out of place. Too little pressure can lead to poor bonding.
The Mold Maker adjusts injection pressure carefully. They balance it to create the perfect adhesion between the two materials.
6. Control of Mold Temperature
Mold temperature also affects adhesion. If the mold is too hot, the materials can flow improperly. If it’s too cold, they may not bond well.
A Mold Maker carefully controls the temperature of the mold. They keep it at the right level for optimal adhesion. This helps the materials fuse together better.
7. The Importance of Timing
Timing is another factor in adhesion. The second material needs to be injected while the first material is still hot. This helps the two materials fuse together.
If the timing is off, the materials might not bond well. A good Mold Maker ensures that the timing is right for perfect adhesion.
8. Use of Adhesion Promoters
Sometimes, even the best materials need a little help. Adhesion promoters are chemicals that improve the bond between materials.
The Mold Maker can add these promoters to the process. They help create a stronger bond. This improves the overall quality of the overmolded part.
9. Mold Design for Better Adhesion
The mold design itself can affect adhesion. If the mold doesn’t allow for proper material flow, the second material may not bond well.
A good Mold Maker designs the mold to ensure that both materials flow together properly. This allows them to bond during the injection process. The design also ensures that the bond is strong and reliable.
10. Post-Molding Treatment for Adhesion
After overmolding, parts may need additional treatment to improve adhesion. Some Electronic Injection Molding parts are exposed to heat or pressure to cure the bond.
The Mold Maker can recommend post-molding processes. These may include heat curing or surface treatments to strengthen the bond between the materials.
11. Preventing Delamination
Delamination is when the two layers of material peel apart. This is often caused by poor adhesion. Delamination is a serious problem in overmolded electronic components.
A skilled Mold Maker knows how to prevent delamination. They ensure proper bonding by using the right materials, techniques, and controls throughout the process.
12. The Role of Material Flow in Adhesion
Material flow affects how well the two materials bond. If one material doesn’t flow properly, it can create weak spots.
The Mold Maker designs the mold to guide material flow effectively. They ensure that both materials fill the mold properly, creating a strong bond between them.
13. The Impact of Environmental Conditions
Environmental factors can impact adhesion. For example, humidity can weaken some materials’ ability to bond.
A skilled Mold Maker will adjust for environmental factors. They design the molding process with these considerations in mind to ensure strong adhesion even in difficult conditions.
14. Testing for Adhesion Strength
Before production begins, it’s important to test adhesion strength. This ensures the bond will hold up during use.
The Mold Maker can conduct tests to check adhesion strength. These tests help catch any potential problems before large-scale production begins.
15. Reducing Warping and Shrinkage
When overmolding, warping and shrinkage can affect adhesion. If one material shrinks more than the other, the bond can weaken.
The Mold Maker can control these issues by adjusting cooling rates and mold design. This helps reduce warping and shrinkage, ensuring strong adhesion.
16. Customizing the Overmolding Process
Each part is different. The materials, design, and application all affect the overmolding process. Customizing the process for each part ensures the best results.
The Mold Maker customizes the overmolding process for each project. This increases the chances of a successful bond and strong adhesion.
17. Optimizing Cycle Time for Adhesion
Cycle time is important in Electronic Injection Molding. If the cycle time is too long, parts can overheat. If it’s too short, the bond may not form properly.
The Mold Maker optimizes the cycle time to ensure proper bonding. This helps create high-quality overmolded parts that perform well in electronic applications.
18. Quality Control for Adhesion
Quality control is crucial in the overmolding process. It ensures that all parts meet adhesion standards.
A skilled Mold Maker implements quality control measures throughout production. This includes testing for adhesion strength and inspecting the finished parts for defects.
Improving adhesion in overmolded electronic components is essential for product success. With the right techniques and the expertise of a skilled Mold Maker, you can avoid common adhesion problems.
From selecting the right materials to optimizing the molding process, every step matters. With the right approach, you can ensure strong, reliable bonds in your overmolded parts, resulting in high-quality electronic components.