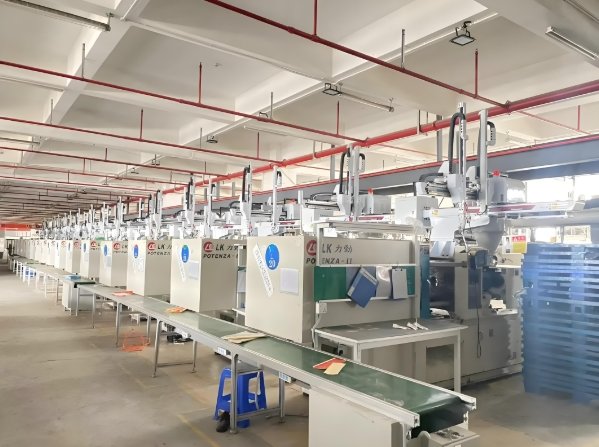
Electronics need durable parts. Weak components cause failures. Electronic injection molding ensures strength and longevity. A skilled mold maker plays a key role. This article explores molding techniques that improve durability.
1. Why Durability Matters in Electronic Components
1.1 Preventing Device Failure
Fragile parts break easily. Electronic injection molding creates strong, impact-resistant components.
1.2 Withstanding Heat and Moisture
Electronics generate heat. They also face moisture. A mold maker selects materials that resist these factors.
1.3 Reducing Maintenance Costs
Stronger components last longer. Electronic injection molding lowers repair and replacement expenses.
2. Key Molding Techniques for Stronger Electronic Parts
2.1 Overmolding for Extra Protection
Overmolding adds layers. A mold maker combines materials for better shock resistance.
2.2 Insert Molding for Secure Connections
Metal inserts increase strength. Electronic injection molding ensures firm bonding.
2.3 Multi-Shot Molding for Versatility
Different materials improve durability. A mold maker uses multi-shot molding for added toughness.
3. Material Selection for Stronger Electronic Components
3.1 High-Performance Plastics
Durable plastics resist wear. Electronic injection molding uses materials like PEEK and LCP.
3.2 Conductive Polymers for Stability
Electronics need stable signals. A mold maker chooses conductive materials that reduce interference.
3.3 Heat-Resistant Compounds
Excess heat damages parts. Electronic injection molding includes heat-resistant resins for protection.
4. Improving Structural Integrity with Advanced Molding
4.1 Uniform Wall Thickness
Uneven walls cause weak spots. A mold maker ensures even thickness for strength.
4.2 Reinforced Rib Designs
Ribs add support. Electronic injection molding includes ribs to prevent warping.
4.3 Tight Tolerances for Precision
Loose parts fail quickly. A mold maker ensures precise tolerances for durability.
5. Surface Finishing for Extra Durability
5.1 Textured Coatings
Coatings prevent scratches. Electronic injection molding adds protective textures.
5.2 Sealed Surfaces for Moisture Resistance
Sealed parts block moisture. A mold maker enhances component lifespan.
5.3 Anti-Corrosion Treatments
Some plastics degrade. Electronic injection molding applies coatings that resist corrosion.
6. Automation in Durable Component Production
6.1 AI-Powered Quality Control
AI detects defects. A mold maker ensures perfect parts with automated checks.
6.2 Robotic Precision in Molding
Robots improve accuracy. Electronic injection molding benefits from precise, automated processes.
6.3 Smart Sensors for Process Optimization
Sensors monitor molding conditions. A mold maker adjusts settings for the best results.
7. Challenges in Strengthening Electronic Components
7.1 Miniaturization Difficulties
Small parts need high precision. Electronic injection molding ensures fine details without defects.
7.2 Balancing Cost and Quality
Better materials cost more. A mold maker finds cost-effective solutions for durability.
7.3 Environmental Resistance
Some environments are extreme. Electronic injection molding adapts materials for harsh conditions.
8. Future Trends in Durable Electronic Molding
8.1 Self-Healing Materials
New plastics repair small cracks. Electronic injection molding will integrate smart materials.
8.2 Sustainable Durable Plastics
Eco-friendly and strong materials are rising. A mold maker focuses on greener solutions.
8.3 Advanced Testing for Longevity
More testing ensures better results. Electronic injection molding will use AI-driven durability tests.
Durability is key in electronics. Electronic injection molding enhances strength. A skilled mold maker ensures reliable, long-lasting components. The future promises even stronger and smarter materials.