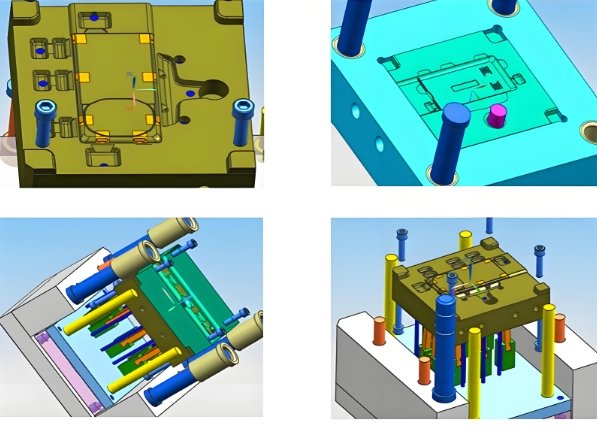
Yield rate matters.
It means more good parts.
Less waste.
Better profits.
In Electronic Injection Molding, every detail counts.
Tiny parts.
Thin walls.
Precise shapes.
For any Mold Maker, improving yield is key.
It cuts cost.
It boosts quality.
It speeds delivery.
Let’s see how.
Why Yield Rates Matter
Yield rate = good parts / total parts.
A high yield means less scrap.
Lower costs.
Faster timelines.
In Electronic Injection Molding, errors cost more.
Electronic parts need perfection.
One defect can break the circuit.
So yield must stay high.
Role of the Mold Maker
The Mold Maker controls the process.
They build the mold.
They design for strength.
They reduce risks.
Good molds equal better parts.
Bad molds kill yield.
So mold quality is critical.
Precise Mold Design
Every cavity must be perfect.
No mismatch.
No flash.
No warpage.
Tight tolerances help.
The Mold Maker uses advanced software.
CAD.
CAM.
Simulation.
They see issues before cutting steel.
High-Quality Mold Materials
Tool steel matters.
Poor steel wears fast.
This creates defects.
The Mold Maker chooses strong metals.
P20.
H13.
S136.
Each suits different needs.
For Electronic Injection Molding, corrosion resistance is key.
Gate and Runner Design
Wrong gate location causes voids.
Short shots.
Warped edges.
The Mold Maker places gates wisely.
Direct gates.
Hot runners.
Valve gates.
This ensures smooth flow.
Venting the Mold
Trapped air causes burns.
Or short shots.
The Mold Maker adds vents.
Tiny slots.
Strategic spots.
This keeps the mold breathing.
And improves yield.
Using Scientific Molding
Data rules.
Not guesswork.
Scientific molding uses sensors.
It tracks pressure.
It records flow.
It studies cooling.
Electronic Injection Molding must be exact.
So data helps control every step.
Controlling Process Settings
Temperature.
Pressure.
Time.
All must be set right.
A few degrees off?
Yield drops.
The Mold Maker works with the processor.
They tune machines together.
Avoiding Flash and Burrs
Flash ruins small parts.
Especially in connectors.
Tight clamping helps.
Proper shut-off design matters.
The Mold Maker keeps the mold aligned.
Even under high pressure.
Better Cooling Layouts
Poor cooling warps parts.
Or slows the cycle.
Both hurt yield.
The Mold Maker uses baffles.
Conformal cooling.
Even temp across the mold.
Cool faster.
Cool evenly.
Yield goes up.
Drying Materials Properly
Wet plastic causes bubbles.
Or weak spots.
Drying is a must.
Especially for ABS.
PC.
PBT.
Electronic Injection Molding needs stable materials.
No moisture.
No risk.
Using the Right Plastic
Wrong plastic causes flow issues.
Burn marks.
Or shrinkage.
The Mold Maker recommends the best resin.
Based on shape.
Function.
Tolerance.
This ensures clean, accurate parts.
Regular Mold Maintenance
Dirty molds = bad parts.
Oil leaks.
Dust.
Worn pins.
All reduce yield.
Maintenance is key.
Clean often.
Check fit.
Polish surfaces.
The Mold Maker sets the schedule.
In-Mold Sensors
Sensors detect pressure and temp.
They alert early.
If flow changes, stop the cycle.
Fix the issue.
That saves bad shots.
And keeps yield high.
Vision Systems for Quality
Cameras inspect parts fast.
Check shape.
Size.
Surface.
AI compares good and bad.
It flags problems early.
This boosts confidence in yield.
Preventing Contamination
Dust hurts electronics.
Cleanroom molding helps.
No hair.
No oil.
No air bubbles.
Electronic Injection Molding must stay clean.
Always.
Minimizing Parting Line Shift
Shift causes mismatch.
Leads to short circuits.
The Mold Maker uses tight tolerances.
Strong guides.
Balanced pressure.
Parts stay aligned.
Yield improves.
Using Hot Runners
Hot runners save material.
No sprue waste.
Also better flow.
Less shear.
Stable temp.
The Mold Maker tunes the system.
This adds to yield rate.
Mold Flow Simulation
Before building, simulate flow.
Check air traps.
Balance gates.
The Mold Maker uses mold flow software.
This fixes design issues early.
Better design = better yield.
Shorter Cycle Times
Faster cycles help.
But not at cost of quality.
Balance is key.
The Mold Maker designs for speed and strength.
No rushing.
Just smart design.
Error Logs and Monitoring
Track every cycle.
Log faults.
Check trends.
This data shows root causes.
So you fix them fast.
Electronic Injection Molding becomes reliable.
Employee Training
Skilled operators matter.
They know signs of trouble.
They adjust fast.
Train them well.
Show them how yield links to profit.
This keeps quality high.
Smart Automation
Robots reduce handling.
Less damage.
Less dust.
Smart automation aids yield.
Consistent pick and place.
No dropped parts.
Molded parts stay clean.
Stay perfect.
High yield equals high success.
In Electronic Injection Molding, yield is king.
Each Mold Maker must plan for it.
Design right.
Build right.
Maintain right.
Use data.
Use sensors.
Use skill.
That’s how you boost yield.
And lead the market.