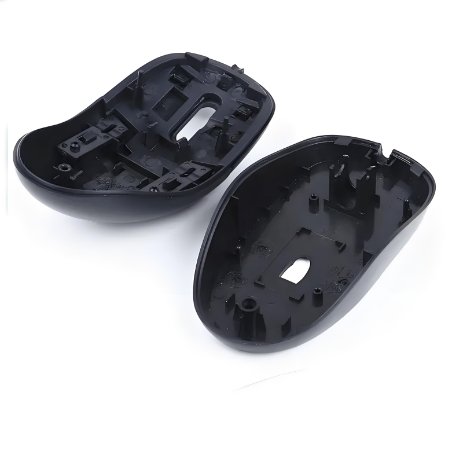
In the competitive world of plastic manufacturing, how and where you produce your mold is a major decision. For companies creating plastic housings, especially in industries like electronics, automotive, and consumer goods, the choice between in-house and outsourced mold production can impact everything—costs, quality, and time to market.
This article explores both options for housing injection molding. We’ll weigh the pros and cons of keeping mold production internal versus hiring an external mold maker. By the end, you’ll understand which approach makes the most sense for your project and long-term growth.
To meet best SEO standards, we’ll maintain a 4% keyword density for housing injection molding and mold maker, and use clean, direct, and engaging sentences.
Why Mold Production Matters in Housing Injection Molding
Plastic housings must meet tight specifications. Whether it’s a phone casing, a medical enclosure, or a home appliance shell, these parts protect inner components, define a product’s appearance, and must fit perfectly every time. That’s why mold production is the foundation of housing injection molding success.
The quality of your mold maker determines the accuracy of the cavity, the surface finish, and how long the mold lasts. So should you build the mold in-house or trust an outside supplier?
What Is In-House Mold Production?
In-house mold production means you own the machines, hire the engineers, and operate the entire mold-making process within your own facility. This includes CAD design, CNC machining, EDM, polishing, and fitting.
Pros of In-House Mold Making
1. Full Control Over Quality
When your own team handles the mold, you maintain direct oversight. That means better control over tolerances, material selection, and finish—especially important for housing injection molding.
2. Faster Iteration
Need a quick change to a gate or ejector pin? In-house teams can adjust and retest molds quickly. No waiting for overseas shipping or third-party schedules.
3. Enhanced Confidentiality
Some companies protect sensitive designs by building molds internally. It reduces the risk of design leaks or intellectual property theft.
4. Seamless Communication
Your design and mold teams are under one roof. There’s no language barrier or time zone issue, which streamlines revisions and speeds up decisions.
5. Long-Term Investment
Owning mold-making equipment can save money over time, especially for companies producing many molds each year.
Cons of In-House Mold Making
1. High Upfront Costs
You need to invest in machines (CNC, EDM, grinders), software, and skilled labor. For many, this capital investment is too steep.
2. Requires Specialized Talent
You must recruit and retain experienced mold makers. Skilled talent is costly and hard to find in many regions.
3. Limited Capacity
Your team can only handle a few projects at a time. If demand surges, lead times may increase.
4. Ongoing Maintenance Costs
Mold-making tools wear out. You’ll need frequent upgrades and repair, which adds overhead to your operations.
What Is Outsourced Mold Production?
Outsourcing mold production means hiring an external mold maker, either domestically or internationally. This mold maker handles the design, machining, fitting, and testing of the mold, then delivers it to you.
Pros of Outsourced Mold Making
1. Lower Initial Cost
You pay only for the mold—no need to invest in equipment or staffing. This is ideal for startups or companies without high mold volumes.
2. Access to Skilled Experts
A professional mold maker focuses solely on toolmaking. They bring experience, technical know-how, and high-end machinery you might not afford in-house.
3. Scalable Capacity
Need multiple molds at once? Outsourcing allows you to assign different projects to different suppliers and hit your deadlines.
4. Global Options
You can choose between local or offshore vendors depending on your priorities—cost, speed, or quality. For example, housing injection molding companies often outsource to China for affordable, high-speed mold builds.
5. No Maintenance Burden
Once the mold is delivered, you’re not responsible for its wear and tear during production. Many mold makers offer lifetime support.
Cons of Outsourced Mold Making
1. Less Control
You rely on your vendor to meet specifications. If communication breaks down, the mold may not meet your expectations.
2. IP Concerns
Sending 3D files to an external party—especially overseas—raises the risk of IP theft or copying.
3. Time Zone and Language Challenges
If your mold maker is in another country, communication delays can slow down your project.
4. Logistics and Lead Time
International shipping, customs, and inspection can add weeks to your schedule—especially if revisions are needed.
Comparing In-House and Outsourced Mold Making
Feature | In-House Mold Making | Outsourced Mold Making |
---|---|---|
Cost | High upfront, lower long-term | Lower upfront, possibly higher long-term |
Speed | Fast for changes, slower for large scale | Fast scale-up, slower revisions |
Quality Control | High control over every step | Varies by mold maker |
IP Security | Strong | Varies (secure with NDAs and contracts) |
Flexibility | Low (limited capacity) | High (choose among many suppliers) |
Capital Requirements | High | Low |
Talent Dependency | Yes | No |
Maintenance | Your responsibility | Mold maker handles (if agreed) |
Which One Works Best for Housing Injection Molding?
It depends on your goals, budget, and product lifecycle.
Choose In-House Mold Making If:
- You create many molds per year for housing injection molding.
- You want total control over quality and IP.
- You can afford the capital investment.
- You have long-term plans to build an internal tooling department.
Choose Outsourced Mold Making If:
- You’re a startup or small business.
- You want to avoid heavy equipment and staffing costs.
- You need molds quickly or at a lower price.
- You trust a global mold maker network and can manage supplier relationships.
Hybrid Strategy: The Best of Both Worlds?
Many companies use a hybrid approach. They outsource early-stage or prototype molds, then bring high-volume or complex projects in-house once validated. Others use external mold makers for new designs but handle maintenance or minor changes internally.
This blended model allows flexibility while minimizing risk in housing injection molding.
Tips for Making the Right Choice
- Evaluate Volume
Low-volume projects may not justify in-house investment. High-volume businesses may save over time by owning their tooling process. - Assess Internal Capabilities
Do you have engineers, machine operators, and a toolroom? If not, outsourcing may be more practical. - Research Mold Makers Carefully
If outsourcing, choose an experienced mold maker with a strong track record in housing injection molding. - Use Strong Contracts
Protect your IP and clarify responsibilities, delivery dates, and revision terms. - Think Long-Term
Your decision should align with your product roadmap and company growth goals.
Conclusion
Whether you build your molds in-house or outsource them, success in housing injection molding starts with choosing the right mold maker. Each approach has unique strengths, and the right decision depends on your company’s structure, capabilities, and production needs.
In-house mold production gives you total control but demands high investment. Outsourcing reduces cost and effort but requires careful supplier management.
No matter the path you choose, always prioritize quality, precision, and partnership. A strong mold maker ensures your housing parts look great, perform well, and last long in the market.