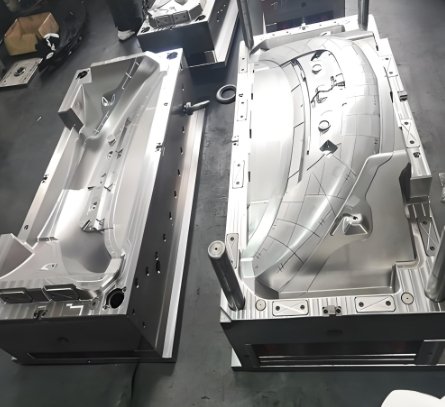
Dashboards are crucial in vehicles. They must be strong, durable, and stylish. Automotive injection molds create high-quality dashboards. A skilled mold maker ensures precision and efficiency.
Why Injection Molding for Dashboards?
1. High Precision
Dashboards need exact shapes. Automotive injection molds provide perfect dimensions. A mold maker ensures smooth edges and accurate details.
2. Strong and Durable
Dashboards face heat, cold, and impact. Automotive injection molds use tough materials. A mold maker selects the best plastics for long life.
3. Cost-Effective Production
Mass production reduces costs. Automotive injection molds make dashboards quickly. A mold maker improves efficiency and minimizes waste.
4. Design Flexibility
Manufacturers need various designs. Automotive injection molds allow complex shapes. A mold maker ensures customization without defects.
Materials Used in Dashboard Injection Molding
1. ABS (Acrylonitrile Butadiene Styrene)
ABS is strong and lightweight. Automotive injection molds use ABS for impact resistance. A mold maker prefers ABS for high durability.
2. Polypropylene (PP)
PP is flexible and tough. Automotive injection molds use PP for dashboards with smooth finishes. A mold maker chooses PP for cost-effective production.
3. Polycarbonate (PC)
PC is heat-resistant. Automotive injection molds use PC for dashboards exposed to sunlight. A mold maker selects PC for its strength and transparency.
4. PVC (Polyvinyl Chloride)
PVC resists chemicals. Automotive injection molds use PVC for dashboards in harsh conditions. A mold maker values PVC for its durability.
Key Processes in Dashboard Injection Molding
1. Mold Design
A perfect mold ensures quality. Automotive injection molds must have precise cavities. A mold maker creates designs with CAD software.
2. Material Selection
Choosing the right plastic is key. Automotive injection molds need heat-resistant and flexible materials. A mold maker tests various plastics for strength.
3. Injection Molding Process
Molten plastic fills the mold. Automotive injection molds shape dashboards under high pressure. A mold maker ensures consistent filling for perfect parts.
4. Cooling and Ejection
Cooling prevents warping. Automotive injection molds have efficient cooling channels. A mold maker optimizes cooling time for faster production.
5. Finishing and Quality Control
Dashboards need smooth surfaces. Automotive injection molds produce defect-free parts. A mold maker inspects for strength and precision.
Advantages of Injection Molding for Dashboards
1. Consistent Quality
Each part matches the design. Automotive injection molds ensure uniformity. A mold maker maintains high precision.
2. High Production Speed
Injection molding is fast. Automotive injection molds produce thousands of dashboards quickly. A mold maker enhances efficiency.
3. Reduced Material Waste
Excess plastic is minimized. Automotive injection molds use optimized gating systems. A mold maker reduces scrap for cost savings.
4. Enhanced Surface Finish
Smooth textures improve dashboard appearance. Automotive injection molds create glossy or matte finishes. A mold maker ensures a perfect look.
Challenges in Dashboard Injection Molding
1. Material Shrinkage
Plastic shrinks after cooling. Automotive injection molds must compensate for shrinkage. A mold maker adjusts mold dimensions for accuracy.
2. Warping and Distortion
Uneven cooling causes warping. Automotive injection molds require precise temperature control. A mold maker optimizes cooling times.
3. Complex Designs
Dashboards have detailed features. Automotive injection molds need accurate tooling. A mold maker ensures perfect cavity shapes.
4. Cost of High-Quality Molds
High-precision molds cost more. Automotive injection molds must balance quality and budget. A mold maker selects cost-effective solutions.
Innovations in Dashboard Injection Molding
1. Lightweight Materials
New plastics reduce weight. Automotive injection molds now use advanced composites. A mold maker selects lightweight yet strong materials.
2. Multi-Material Molding
Dashboards combine hard and soft plastics. Automotive injection molds integrate multiple materials in one process. A mold maker perfects multi-shot molding.
3. Automated Production
Robots improve efficiency. Automotive injection molds now use automation for consistency. A mold maker programs machines for precision.
4. Sustainable Manufacturing
Recycled plastics reduce waste. Automotive injection molds now use eco-friendly materials. A mold maker focuses on green production methods.
Future of Dashboard Injection Molding
1. Smart Dashboards
Embedded screens and sensors require precision. Automotive injection molds must adapt to new designs. A mold maker innovates for high-tech dashboards.
2. 3D Printing for Prototyping
Rapid prototyping speeds up design. Automotive injection molds benefit from 3D-printed samples. A mold maker tests new shapes quickly.
3. AI-Driven Mold Design
Artificial intelligence improves accuracy. Automotive injection molds are now optimized with AI. A mold maker uses data to refine designs.
4. More Sustainable Materials
Bio-based plastics are emerging. Automotive injection molds will soon use biodegradable materials. A mold maker explores eco-friendly options.
Dashboards need precision, strength, and style. Automotive injection molds ensure high-quality production. A skilled mold maker guarantees efficiency and durability. The future of dashboard molding will bring lighter, stronger, and smarter designs.