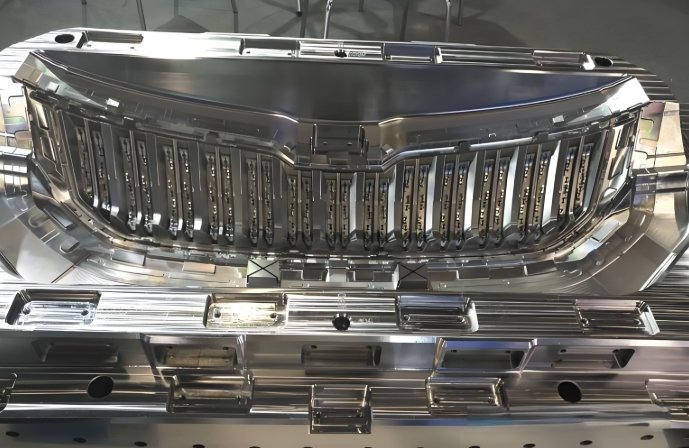
Automotive electronics are essential. They enhance vehicle safety and comfort. Automotive Injection Molds are crucial in producing electronic components. Skilled Mold Makers design these molds for precision. This ensures high-quality parts every time.
Why Automotive Injection Molds Matter
1. Precision Manufacturing
Electronics demand accuracy. Injection molds meet tight tolerances.
2. Efficient Production
Injection molds support mass production. This reduces costs.
3. Durability
High-quality molds ensure consistent results. This maintains product longevity.
Key Automotive Electronics Made with Injection Molds
1. Control Units
Injection molds shape control module housings. These protect sensitive circuits.
2. Sensors
Sensors need intricate designs. Molds create reliable sensor casings.
3. Lighting Systems
Molds produce LED and headlight housings.
4. Connectors
Connectors link multiple systems. Molds ensure precise fit and functionality.
Role of the Mold Maker
1. Custom Designs
Mold Makers tailor designs for specific needs. This ensures perfect component fit.
2. Material Expertise
Choosing the right material ensures durability.
3. Precision Tools
High-tech equipment ensures accurate molds.
4. Quality Testing
Mold performance is validated through rigorous tests.
Advantages of Injection Molds in Electronics
1. Lightweight Parts
Molds create lighter components. This improves fuel efficiency.
2. Consistent Quality
Injection molds ensure every part meets standards.
3. Cost-Effective Production
Durable molds reduce manufacturing costs.
4. Sustainability
Injection molding minimizes waste.
Challenges in Mold Design for Electronics
1. Complex Geometries
Electronic parts require intricate molds.
2. Thermal Stability
Materials must withstand heat and cold.
3. Miniaturization
Electronics are becoming smaller. Molds must adapt.
4. Material Selection
Molds must work with different plastics.
Innovations in Mold Design
1. 3D Printing
Prototyping speeds up mold creation.
2. Smart Sensors
Sensors monitor mold performance.
3. Sustainable Materials
Eco-friendly options reduce environmental impact.
4. Advanced Cooling Systems
Better cooling improves cycle times.
Steps in Creating an Automotive Injection Mold
1. Concept Design
Understanding the part’s use is key.
2. Material Selection
Choose the best material for durability.
3. Prototyping
Build and test a prototype mold.
4. Production
Use high-precision machines for manufacturing.
5. Testing and Validation
Ensure the mold meets design requirements.
Applications in Key Automotive Systems
1. Infotainment Systems
Injection molds produce display frames and buttons.
2. Safety Features
Molds shape airbag sensors and braking modules.
3. Energy Systems
Battery housings and charging ports rely on molds.
4. Comfort Controls
Switches and dials use injection molds.
Future Trends
1. AI Integration
AI optimizes mold designs for electronics.
2. Eco-Friendly Practices
Recycled materials will dominate.
3. Advanced Robotics
Automation improves mold production.
4. Miniaturized Molds
As electronics shrink, molds must evolve.
Automotive Injection Molds are vital for electronics. They ensure precision and durability. Skilled Mold Makers enhance mold efficiency. Innovation drives better mold designs. Investing in advanced molds secures high-quality electronic parts.