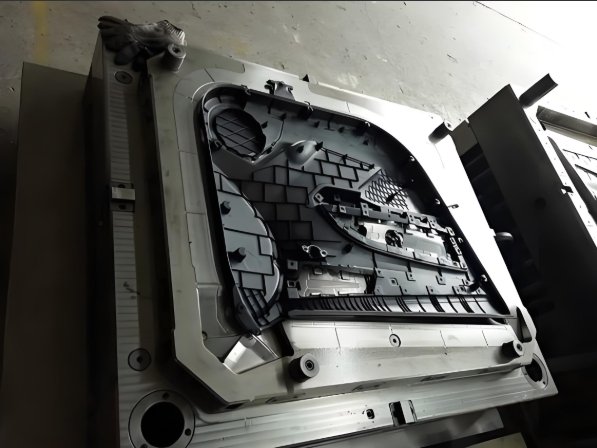
Modern vehicles need precise parts. Automotive injection molds shape these components. A skilled mold maker ensures accuracy. The right mold design improves efficiency. High-tech processes create strong, lightweight parts. Optimized designs reduce waste and costs.
Why Efficient Mold Design Matters?
1. Faster Production
Time is money. Automotive injection molds must work quickly. A mold maker designs molds for speed. Cycle time reduction increases efficiency.
2. Lightweight Components
Lighter cars use less fuel. Strong yet light parts improve performance. A mold maker selects advanced materials. Automotive injection molds create lightweight, durable components.
3. Reduced Waste
Material waste increases costs. Efficient molds use precise plastic amounts. A skilled mold maker minimizes excess. Automotive injection molds reduce production waste.
4. Cost Savings
Better designs lower manufacturing costs. Less material, faster cycles, and fewer defects save money. Mold makers focus on efficiency.
Key Elements of Efficient Injection Mold Design
1. Mold Flow Analysis
Simulations predict plastic flow inside molds. This ensures even distribution. A mold maker uses software to optimize designs. Automotive injection molds require precise flow control.
2. Gate Placement Optimization
Plastic enters the mold through gates. The right placement prevents defects. A skilled mold maker positions gates carefully. Automotive injection molds rely on smooth filling.
3. Cooling System Efficiency
Cooling affects cycle time. Poor cooling slows production. A mold maker designs efficient cooling channels. Automotive injection molds with fast cooling reduce costs.
4. Venting for Air Removal
Trapped air causes defects. Proper venting prevents bubbles. A mold maker adds vents in key areas. Automotive injection molds need smooth surfaces.
5. Multi-Cavity Molds
More cavities mean more parts per cycle. This boosts efficiency. A skilled mold maker balances cavity design. Automotive injection molds with multiple cavities speed up production.
6. Hot Runner Systems
Hot runners keep plastic melted inside the mold. This reduces waste. Mold makers use hot runners for efficiency. Automotive injection molds benefit from continuous flow.
7. Precision Core and Cavity Alignment
Misalignment causes defects. Precision alignment ensures quality. A mold maker uses advanced machining. Automotive injection molds need exact positioning.
High-Tech Materials for Efficient Mold Designs
1. High-Performance Polymers
Advanced plastics make cars lighter. Strong polymers improve durability. A mold maker selects the best materials. Automotive injection molds must resist heat and stress.
2. Composite Materials
Composites mix plastics and fibers. They reduce weight without losing strength. A mold maker uses composites for efficiency. Automotive injection molds create lightweight parts.
3. Metal Inserts for Strength
Some parts need extra reinforcement. Metal inserts add durability. A mold maker combines plastic and metal. Automotive injection molds with inserts create stronger components.
Applications of Efficient Injection Mold Designs
1. Interior Components
Dashboards, consoles, and trims need precise molding. Automotive injection molds ensure perfect fit. A mold maker focuses on fine details.
2. Exterior Panels
Bumpers, grilles, and fenders must be impact-resistant. Efficient molding enhances durability. A skilled mold maker designs molds for smooth finishes.
3. Engine and Fuel System Parts
Fuel tanks, pumps, and air ducts require precision. Automotive injection molds create leak-proof designs. A mold maker ensures tight tolerances.
4. Lighting Components
Headlights and taillights need clear, strong materials. Advanced molding improves clarity. A mold maker polishes molds for optical precision.
5. Safety Features
Seatbelt housings, airbag covers, and crash-resistant parts need durability. Automotive injection molds produce high-strength components. A mold maker ensures safety compliance.
Challenges in Designing Efficient Molds
1. Balancing Speed and Quality
Fast cycles must not reduce quality. A mold maker finds the right balance. Automotive injection molds need careful adjustments.
2. Managing Complex Shapes
Modern car parts have intricate designs. Automotive injection molds must capture fine details. Advanced CAD software helps a mold maker achieve precision.
3. Preventing Defects
Warping, shrinkage, and air bubbles cause rework. A mold maker reduces defects with optimized designs. Automotive injection molds must produce flawless parts.
4. Adapting to New Materials
The auto industry evolves quickly. Mold makers must stay updated. Automotive injection molds need constant improvements.
Future Trends in Automotive Mold Design
1. AI-Optimized Molds
Artificial intelligence will refine designs. AI detects weak points before production. Mold makers will use AI for better efficiency.
2. Smart Sensors in Molds
Sensors will track temperature and pressure. Automotive injection molds will self-adjust. A mold maker will monitor data in real time.
3. Sustainable Mold Design
Eco-friendly materials will reduce waste. Mold makers will use biodegradable plastics. Automotive injection molds will support sustainability.
4. Fully Automated Production Lines
Automation will streamline processes. Robots will assist mold makers in refining designs. Automotive injection molds will become smarter and faster.
Efficient automotive injection molds shape the future of car manufacturing. A skilled mold maker ensures precision and cost-effectiveness. Advanced designs reduce waste and improve performance. As technology evolves, injection mold efficiency will continue to improve.