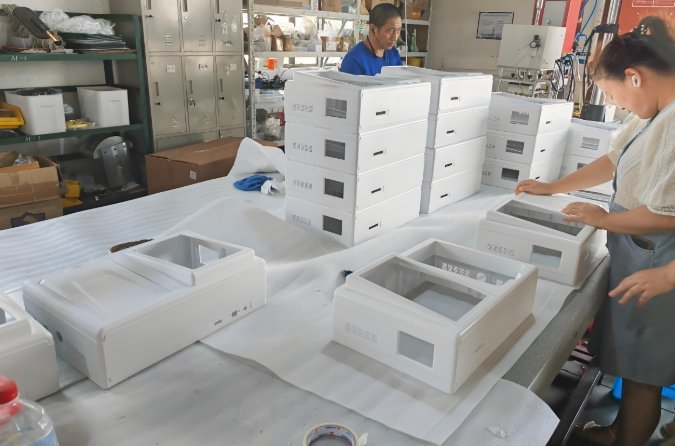
5G technology is growing fast. It needs high-precision parts. Electronic injection molding plays a key role. A mold maker ensures these components meet strict quality standards. This article explores how injection molding supports 5G development.
1. The Importance of 5G in Modern Technology
1.1 Faster Connectivity
5G provides ultra-fast data speeds. Devices need durable and precise components. Electronic injection molding ensures consistency in production.
1.2 Low Latency Requirements
5G networks need low latency. Signal interference must be minimized. A mold maker creates precise enclosures that protect delicate circuits.
1.3 Increased Data Transfer
More data requires better electronic shielding. Molding techniques enhance performance. Electronic injection molding supports advanced material use.
2. How Injection Molding Supports 5G Components
2.1 Precision Molding for Small Parts
5G components are tiny. They need accurate manufacturing. Electronic injection molding ensures exact dimensions.
2.2 Consistent Mass Production
5G devices require millions of parts. A mold maker produces identical components at high speed.
2.3 Advanced Materials for 5G Components
Materials must withstand heat and signal interference. Electronic injection molding allows the use of high-performance plastics.
3. Key 5G Components Made with Injection Molding
3.1 Antenna Housings
5G antennas need strong, lightweight covers. A mold maker produces precise casings with durable plastics.
3.2 Connectors and Sockets
5G devices need secure connections. Electronic injection molding creates high-precision connectors.
3.3 Heat-Resistant Casings
5G generates more heat than 4G. A mold maker uses heat-resistant materials for protection.
3.4 Circuit Board Enclosures
Sensitive electronics need shielding. Electronic injection molding creates enclosures that reduce interference.
4. Advanced Materials in 5G Injection Molding
4.1 High-Performance Plastics
Materials like PEEK and LCP resist high temperatures. A mold maker selects materials based on strength and durability.
4.2 EMI Shielding Polymers
Electromagnetic interference affects 5G signals. Electronic injection molding uses conductive plastics for shielding.
4.3 Heat-Resistant Composites
5G devices operate in extreme conditions. A mold maker chooses composites that prevent overheating.
5. Automation in 5G Injection Molding
5.1 Robotic Assembly
Automation speeds up production. Electronic injection molding benefits from robotic precision.
5.2 AI-Driven Quality Control
AI detects defects in real-time. A mold maker ensures every part meets strict specifications.
5.3 Smart Molds with Sensors
Sensors monitor temperature and pressure. Electronic injection molding achieves higher consistency.
6. Challenges in 5G Injection Molding
6.1 Miniaturization Complexity
Smaller components require higher precision. A mold maker must ensure flawless designs.
6.2 Material Selection Issues
Not all plastics work for 5G. Electronic injection molding requires extensive material testing.
6.3 Production Costs
High-quality materials increase costs. A mold maker must balance quality and affordability.
7. Future Trends in 5G Injection Molding
7.1 Smart Materials
New polymers improve durability. Electronic injection molding will integrate self-healing materials.
7.2 Fully Automated Factories
AI and robotics will handle production. A mold maker will oversee processes with minimal manual labor.
7.3 Sustainable Manufacturing
Eco-friendly plastics will reduce waste. Electronic injection molding will become more sustainable.
5G technology demands precision. Electronic injection molding ensures reliable, high-performance components. A mold maker plays a vital role in the future of 5G electronics.