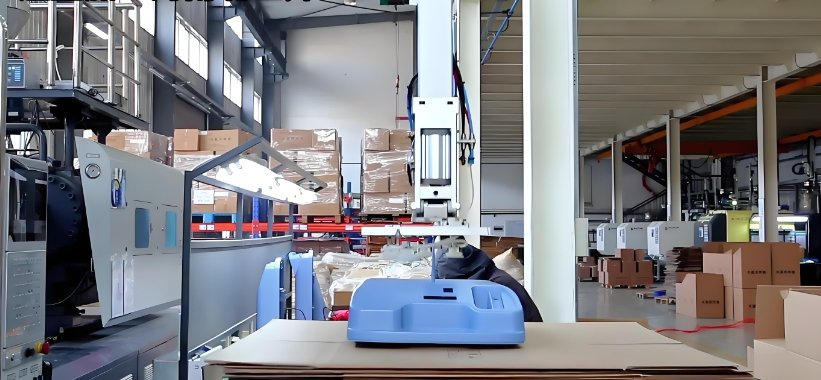
In the fast-paced world of communication technology, devices must be sleek, lightweight, and durable. Think of items like smartphones, routers, walkie-talkies, modems, and intercom systems. Each one relies on a sturdy, attractive housing to protect delicate internal parts and deliver an appealing look to users. This is where Housing Injection Molding shines.
Housing Injection Molding is a trusted solution for making enclosures for communication devices. It produces parts with excellent consistency, high strength, and refined aesthetics. Behind every successful housing is a skilled Mold Maker. This expert creates the molds that give shape and precision to every plastic housing.
In this article, we will explore the key benefits of Housing Injection Molding for communication devices, the materials used, the role of the Mold Maker, and real-world applications that highlight the value of this technology.
Why Communication Devices Need Strong Housings
Communication devices are used daily in many industries and personal settings. Their housings must meet several needs:
- Protection: They shield internal PCBs, antennas, and batteries from impact and moisture.
- Aesthetics: Users want devices that look modern and clean.
- Durability: Many devices are portable and face wear and tear.
- Precision: Small buttons, ports, and vents must be accurate.
Housing Injection Molding meets all these requirements. It allows manufacturers to make detailed housings quickly and at scale.
What is Housing Injection Molding?
Housing Injection Molding is a manufacturing process that injects melted plastic into a metal mold. When the plastic cools, it forms a hard, precise shape—perfect for device housings.
The process is ideal for producing high volumes of parts that need consistent quality. It supports complex shapes, tight tolerances, and various surface textures. Communication devices often feature small speaker holes, mounting bosses, and thin walls. Housing Injection Molding handles all of these with ease.
The Crucial Role of the Mold Maker
The Mold Maker is the person who builds the metal mold used in injection molding machines. Their work directly affects the final part quality.
A professional Mold Maker performs the following tasks:
- Designs the mold based on 3D part data
- Selects proper mold steel based on expected production volume
- Adds cooling channels, slides, and ejectors
- Finishes surfaces to create gloss or texture
- Tests and adjusts the mold to eliminate defects
For communication device housings, every port, curve, and latch must be accurate. Without a skilled Mold Maker, the final part may have flash, short shots, or warping. High-quality tooling is key to success in Housing Injection Molding.
Common Materials for Communication Device Housings
Communication devices must be strong, heat-resistant, and sometimes anti-static. Popular materials used in Housing Injection Molding include:
- ABS (Acrylonitrile Butadiene Styrene) – Tough and easy to mold; good for casings
- PC (Polycarbonate) – Clear and impact-resistant; ideal for covers and screens
- PC/ABS Blends – Offers a balance of strength and aesthetic quality
- Nylon (PA) – Used for rugged outdoor communication housings
- TPU (Thermoplastic Polyurethane) – For flexible covers and grip areas
Each plastic behaves differently when molded. A seasoned Mold Maker must design the mold according to the selected material’s shrinkage, flow rate, and cooling time.
Key Design Features Enabled by Injection Molding
Housing Injection Molding supports a range of features that benefit communication devices:
- Snap-fit joints – Easy assembly without screws
- Built-in cable guides – Clean internal layout
- Textured grip areas – For handheld radios and phones
- Light pipes – For LED visibility
- EMI shielding options – With special coatings or inserts
These features can be molded in one cycle, reducing labor and part count. That makes Housing Injection Molding efficient and affordable for high-tech device housings.
Applications of Housing Injection Molding in Communication
This technology is used in many types of communication equipment. Examples include:
- Two-way radios – Durable housings with rubber overmold grips
- Wireless routers – Stylish ABS enclosures with vents
- VOIP phones – Precise button cutouts and screen frames
- Smartphones – Inner shells and mounting trays
- Signal amplifiers – Rugged outdoor enclosures
- Intercom panels – Weatherproof housings with speaker covers
Each of these applications benefits from the speed and precision of Housing Injection Molding and the skill of a dedicated Mold Maker.
Advantages of Injection Molding for Communication Housings
There are many reasons manufacturers choose Housing Injection Molding:
1. High Precision
Tight tolerances are critical for fitting circuit boards, buttons, and ports. Injection molding delivers this precision.
2. Fast Cycle Times
Once the mold is built, each part takes only seconds to produce—ideal for large production volumes.
3. Lower Unit Cost
The upfront mold cost is balanced by low cost per part, especially in high-volume production.
4. Consistent Quality
Parts from Housing Injection Molding are nearly identical. That helps with assembly and customer satisfaction.
5. Design Flexibility
You can mold logos, textures, mounts, and other features directly into the housing.
6. Lightweight but Durable
Plastic housings reduce overall device weight while remaining strong.
All these benefits depend on the mold’s quality. A well-designed and well-maintained mold from a trusted Mold Maker makes the difference.
Challenges and How the Mold Maker Solves Them
Despite its strengths, Housing Injection Molding comes with some challenges:
- Thin wall sections can be hard to fill
- Part warpage can occur if cooling is uneven
- Complex shapes may require mold slides or lifters
- Surface defects can ruin the device’s appearance
The Mold Maker addresses these issues by:
- Optimizing gate location and cooling channels
- Using simulation software to test designs
- Adding venting and flow leaders to ensure full filling
- Finishing mold surfaces to match visual requirements
Their skill ensures that every molded housing meets the highest standards.
Quality Checks for Communication Device Housings
To ensure durability and fit, Housing Injection Molding parts go through quality checks such as:
- Dimensional inspection using calipers and 3D scanners
- Drop and impact testing for rugged devices
- Visual inspection for scratches and flow lines
- Fit testing with internal components
The Mold Maker often supports this process, helping tune the mold to prevent future defects.
Communication devices are part of our daily lives. Whether at home, work, or in the field, these devices must perform reliably. Their housings play a major role in protection, appearance, and functionality. That’s why Housing Injection Molding is the go-to method for producing plastic enclosures for communication equipment.
The quality of each housing depends on the expertise of the Mold Maker. A skilled Mold Maker ensures that every design detail is transferred into the final product with accuracy and care. Their work is essential to making high-quality, high-volume communication device housings.
For any business seeking efficient production, attractive product finishes, and long-lasting housings, Housing Injection Molding backed by a professional Mold Maker is the smart choice.
Would you like help turning this into a downloadable technical sheet or sales page for your communication product line?