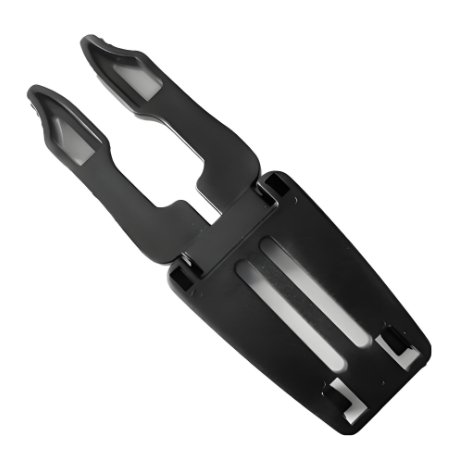
Housing Injection Molding is the top choice for producing strong, reliable plastic enclosures. Whether it’s for electronics, appliances, or medical devices, manufacturers turn to this method to create durable, high-performance housings. The process is efficient and precise. But most importantly, it makes products last longer under stress, wear, and harsh environments.
At the core of this success is the expertise of the Mold Maker. A good Mold Maker ensures every part of the housing meets the highest standards of strength, consistency, and quality.
This article explains why Housing Injection Molding is perfect for durable plastic housings, what role the Mold Maker plays, and how the process ensures long-lasting products.
Why Durable Plastic Housings Matter
Durability is a key part of any plastic housing design. These housings protect inner components from damage caused by:
- Drops and impacts
- Moisture and dust
- Heat and chemicals
- Long-term wear
Whether it’s a smartphone case or a car dashboard, housings must be strong enough to survive daily use.
That’s where Housing Injection Molding comes in. It gives you the ability to design tough housings with consistent shapes and sizes. A skilled Mold Maker helps you get the strength your product needs while keeping costs low and quality high.
How Housing Injection Molding Adds Strength
Several factors contribute to the durability of injection-molded plastic housings:
1. Material Selection
Different plastics have different strengths. For example:
- Polycarbonate is tough and impact-resistant
- ABS is strong and easy to mold
- Nylon resists wear and chemicals
In Housing Injection Molding, material choice is critical. The Mold Maker works with you to pick the right plastic for the housing’s job. They understand how each resin flows, cools, and holds up over time.
2. Mold Design
A good mold equals a good part. In Housing Injection Molding, the mold must be built to deliver consistent pressure and flow. Weak spots often form in corners or thin sections. A knowledgeable Mold Maker designs the mold to avoid air pockets, weld lines, and thin areas that could break.
Mold design also includes adding ribs, gussets, or rounded corners—all of which improve part strength without adding too much material.
3. Controlled Injection Process
Precision is everything. The process involves exact control of:
- Injection pressure
- Melt temperature
- Cooling time
- Clamp force
Each step affects how the plastic flows into the mold and how strong the final part will be. The Mold Maker sets up the mold with the right tolerances and helps fine-tune machine settings during trial runs.
Key Design Features That Boost Durability
To get strong plastic housings, you must start with good part design. Some features that improve strength include:
1. Uniform Wall Thickness
Thick or uneven walls cool at different rates. This can lead to stress, warping, or cracking. Uniform thickness helps the part cool evenly and stay strong.
2. Rounded Corners
Sharp corners can lead to cracks or stress marks. Rounded edges reduce this risk and improve load distribution.
3. Structural Ribs
Ribs increase stiffness without using more plastic. They are common in large housings and covers.
4. Bosses and Inserts
Threaded bosses or metal inserts allow you to screw, snap, or fasten parts securely. These must be placed carefully to avoid weak spots. A good Mold Maker ensures that these features fit well with the mold and avoid stress during molding.
Materials That Withstand Harsh Conditions
The choice of material is essential when creating housings for harsh use. Common durable plastics used in Housing Injection Molding include:
- Polycarbonate (PC): High impact resistance, transparent, good heat resistance
- ABS: Tough, cost-effective, widely used in electronics
- Nylon (PA): Excellent wear and chemical resistance
- PBT: Good for electrical housings, resists heat and chemicals
- PPS: Used in automotive and high-heat environments
The Mold Maker will help evaluate the exact needs of the housing—impact strength, UV exposure, moisture resistance—and recommend the right resin.
Quality Assurance and Testing
Durable housings must pass several tests before they go to market. These can include:
- Drop tests
- Thermal cycling
- Water and dust resistance tests
- UV exposure
- Chemical resistance tests
The process of Housing Injection Molding includes trial runs, dimensional checks, and strength testing. A responsible Mold Maker helps run these tests during the mold approval phase, before full production starts.
Reducing Defects and Waste
Durable parts require defect-free molding. Common problems like warping, voids, or flash can weaken the housing.
A skilled Mold Maker builds the mold to avoid these issues. They also inspect the mold regularly for wear and damage. Their expertise helps cut down on scrap, saving you money and ensuring each part is strong and consistent.
Sustainable Durability
Today’s products must last—but also reduce their impact on the environment. Housing Injection Molding helps with both.
Durable housings mean less product failure and fewer replacements. Recycled materials and efficient designs can reduce plastic use. The Mold Maker can guide these choices, ensuring strength while meeting sustainability goals.
Real-World Applications of Durable Plastic Housings
- Consumer electronics: Smartphones, routers, game consoles
- Automotive: Dashboards, control panels, mirror housings
- Medical: Enclosures for diagnostic and monitoring devices
- Industrial: Equipment covers, control box housings
- Appliances: Washing machine panels, microwave housings
In each case, Housing Injection Molding ensures strength, appearance, and long life. The role of the Mold Maker is crucial at every step.
Durability doesn’t happen by accident. It’s the result of smart design, the right materials, and expert tooling. Housing Injection Molding brings all of these together. But to get the most out of it, you need a reliable Mold Maker.
From mold design to material advice and testing, the Mold Maker ensures each plastic housing meets your expectations for strength and performance.
If you want to create housings that last, Housing Injection Molding is your best option—and the right Mold Maker is your best partner.