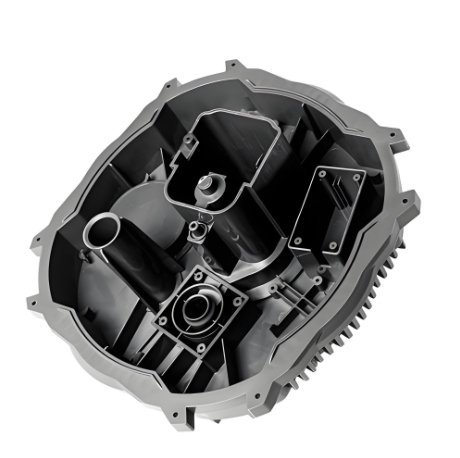
As electronic devices become more powerful and compact, they also become more sensitive to electromagnetic interference (EMI). EMI can disrupt signals, cause malfunctions, and even damage delicate components. This makes EMI shielding more important than ever.
One of the best ways to achieve strong EMI protection is through Electronic Injection Molding. Combined with the skills of an experienced Mold Maker, this process creates tough, protective housings that block harmful interference. Let’s explore how this method is changing the future of electronics.
What is EMI and Why is Shielding Necessary?
EMI stands for electromagnetic interference. It happens when external energy—like radio waves or static electricity—disrupts the operation of an electronic device.
Without protection, devices may:
- Drop communication signals
- Freeze or crash
- Perform incorrectly
- Suffer permanent damage
Smartphones, medical devices, drones, and industrial tools are just a few examples where EMI protection is critical. The smaller and more complex the device, the more important shielding becomes.
Electronic Injection Molding with EMI shielding materials gives devices the strong, durable defense they need. A skilled Mold Maker ensures the shield fits perfectly, maximizing protection.
How Electronic Injection Molding Helps EMI Shielding
Electronic Injection Molding is a process where molten plastic is injected into a mold cavity to form a solid part. For EMI shielding, special conductive materials or coatings are used during or after molding.
Here’s how Electronic Injection Molding supports strong EMI protection:
1. Conductive Materials
Special plastics filled with conductive fibers, like carbon or metal, can block or absorb electromagnetic waves. These materials are molded into precise shapes using Electronic Injection Molding.
An expert Mold Maker ensures that the molds are designed to flow these tricky materials smoothly, without defects that could weaken shielding.
2. Overmolding for Added Protection
In some cases, overmolding is used. This means a device is first enclosed in one material, then a second, conductive layer is molded over it.
This two-step process creates a complete EMI barrier around sensitive parts. Good design and mold building by the Mold Maker ensure a perfect bond between the two materials.
3. Precision Fit and Seam Control
Even small gaps can allow EMI to sneak in. Electronic Injection Molding offers very tight tolerances, creating parts that fit together with almost no spaces.
Precision by the Mold Maker is critical to guarantee complete coverage and avoid weak points where interference could enter.
4. Post-Molding Shielding
Sometimes, after Electronic Injection Molding, parts are coated with conductive paints or films. This gives added flexibility and allows selective shielding where needed.
Still, the base part must be molded perfectly by the Mold Maker to accept these coatings properly.
Common Materials Used for EMI Shielding in Injection Molding
For effective EMI protection, material choice is very important. Some popular options include:
- Conductive Polycarbonate/ABS Blends: Strong and tough for durable shields.
- Carbon-Fiber Reinforced Polymers: Lightweight and excellent for absorbing interference.
- Metal-Filled Plastics: Blend strength with high conductivity.
- Liquid Silicone Rubber (LSR) with conductive additives: Used for flexible shielding needs.
Choosing the right material depends on the device’s needs. A good Mold Maker understands how to handle these special materials during the Electronic Injection Molding process to maximize shielding and durability.
Applications of Injection-Molded EMI Shields
The demand for EMI protection spans many industries. Electronic Injection Molding is critical in applications like:
- Medical Devices: Protecting sensitive monitors and implants.
- Automotive Electronics: Shielding control units and sensors.
- Consumer Electronics: Safeguarding smartphones, tablets, and wearables.
- Telecommunications: Protecting networking equipment.
- Industrial Systems: Defending sensitive controllers and automation equipment.
In every case, the expertise of a top Mold Maker is what brings the design to life and ensures lasting EMI protection.
The Critical Role of the Mold Maker
When it comes to EMI shielding, the Mold Maker has a huge impact. Building molds for conductive materials is more difficult than for regular plastics.
A Mold Maker must:
- Design for complex shapes while maintaining consistent flow paths.
- Allow for fibers or metal particles in the material without blocking mold channels.
- Ensure venting is perfect to avoid trapped air, which could create weak spots.
- Polish molds to the correct level to ensure good material conductivity after molding.
Without the careful planning and execution of a skilled Mold Maker, EMI shielding parts would be unreliable and prone to failure.
Advantages of Using Electronic Injection Molding for EMI Shielding
Choosing Electronic Injection Molding for EMI shielding offers many benefits:
- Lower Cost: Molding conductive plastics is often cheaper than building metal housings.
- Lightweight Parts: Lighter than traditional metal shields, great for portable electronics.
- Complex Shapes: Easier to make intricate, compact designs.
- Mass Production: Perfect for high-volume production with consistent quality.
- Customization: Specific parts of a device can be shielded selectively.
With the help of an expert Mold Maker, manufacturers can take full advantage of these benefits.
Future Trends in EMI Shielding and Injection Molding
The world of EMI shielding is evolving fast, and Electronic Injection Molding will continue to lead the way.
Some exciting trends include:
- Nanomaterials: Super-fine additives for even better shielding with less material.
- Smart Materials: Plastics that adjust their conductivity based on the environment.
- Hybrid Shields: Combining multiple materials in a single molding step.
- Automated Quality Checking: Using AI to check shield performance during production.
Mold Makers who master these new technologies will play a crucial role in the next generation of protected electronics.
EMI shielding is more important than ever in our connected world. From medical equipment to smartphones, electronics must be protected from harmful interference to work reliably and safely.
Thanks to Electronic Injection Molding and the craftsmanship of skilled Mold Maker teams, it is now possible to create durable, lightweight, and cost-effective EMI shields. Using conductive materials, precision overmolding, and perfect mold designs, manufacturers can keep their devices safe from disruption.
As technology continues to shrink and grow more powerful, the role of Electronic Injection Molding and expert Mold Maker services will become even more critical. Companies that invest in these capabilities today will be the leaders of tomorrow’s electronic markets.