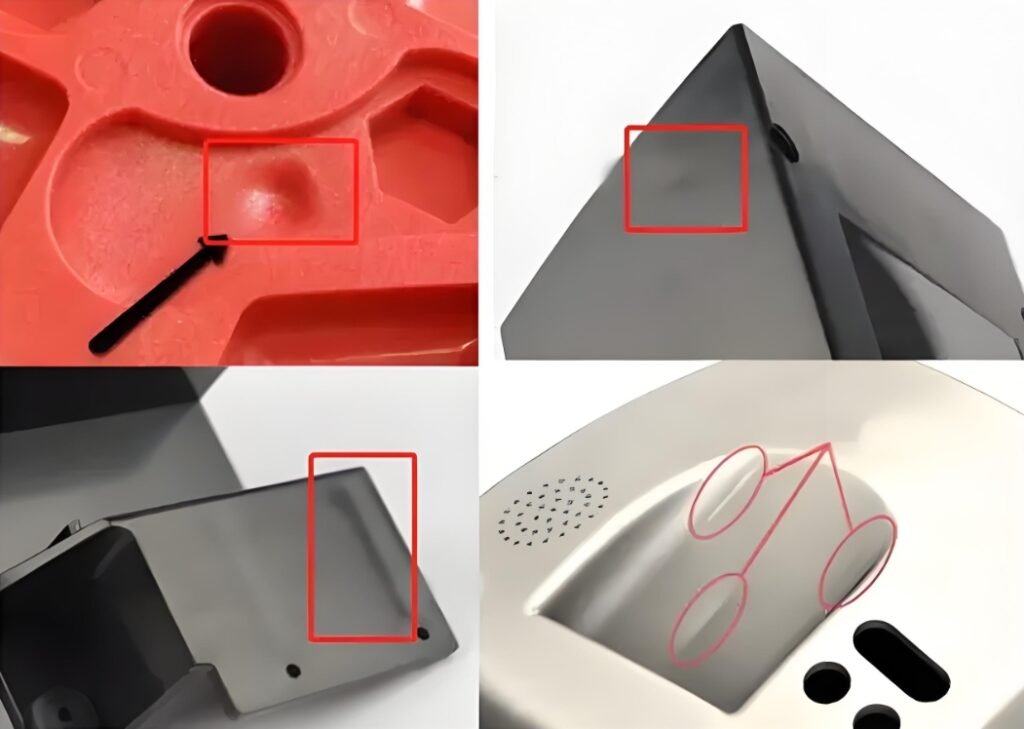
Shrinkage is a common issue in injection molding. It happens when the molded parts become smaller than expected after cooling. Mold makers and injection mould companies often face this problem. Knowing the reasons for shrinkage and how to reduce it is essential for producing quality parts.
Causes of Shrinkage in Injection Molding
One major cause of shrinkage is material cooling. When the material cools, it contracts. Different plastics shrink at different rates. This is a natural process. Mold makers understand that they need to account for this in mold design. If they don’t, the final part may be smaller than required.
Injection pressure is another factor. Low pressure can lead to shrinkage. The pressure forces the melted plastic into the mold cavity. If the pressure is too low, the material won’t fully fill the mold. As a result, the part may shrink.
Cooling rate is also crucial. If the part cools too quickly, it may shrink more. A slow and even cooling process can help prevent this. Mold makers often adjust the cooling system to maintain consistent temperatures.
Part thickness
Part thickness plays a role too. Thicker parts tend to shrink more. This happens because thicker sections hold more heat. As they cool, they shrink more than thinner areas. Mold makers need to consider this when designing molds.
Material choice affects shrinkage too. Some plastics are more prone to shrinking. Each material has different shrinkage rates. Mold makers must choose the right plastic for each project.
Lastly, mold design can cause shrinkage. Poorly designed molds can create uneven shrinkage. A good mold maker considers all factors. This includes material, pressure, and cooling. An injection mould company must ensure the design accounts for shrinkage.
Improving Shrinkage in Injection Molding
Now that we know the causes, let’s look at solutions. Mold makers and injection mould companies use several methods to improve shrinkage. Here are the main techniques.
Increase Injection Pressure
Using higher pressure helps the plastic fill the mold better. It forces the material into every corner of the mold. This reduces shrinkage. Mold makers often adjust pressure settings to find the perfect balance. Too much pressure, however, can cause flash or warping.
Optimize Cooling Rate
A slower cooling rate can reduce shrinkage. Mold makers set up cooling systems to control the cooling process. Cooling the part evenly helps avoid excessive shrinkage. An injection mould company should always aim for controlled cooling.
Use a Uniform Wall Thickness
Designing parts with even thickness is important. Uneven thickness causes uneven cooling. Thicker areas may shrink more. Mold makers design parts with uniform walls to prevent this. It leads to less shrinkage and better quality parts.
Choose the Right Material
Different plastics behave differently. Some have high shrinkage rates. Mold makers should select materials with lower shrinkage. This is especially important for precision parts. An injection mould company must test materials to find the best option for the job.
Improve Mold Design
Good mold design is key to reducing shrinkage. The mold must account for all variables, like pressure, cooling, and material. A skilled mold maker will analyze the part and make the necessary adjustments. They may modify the size of the mold cavity to compensate for shrinkage.
Use Packing Pressure
Packing pressure is applied after the initial injection. This pressure helps keep the plastic in the mold as it cools. It can prevent shrinkage by ensuring the material stays compact. Injection mould companies often use this technique for high-quality parts.
Control the Molding Temperature
Temperature control is vital. Both mold and material temperatures affect shrinkage. Mold makers monitor these temperatures closely. Keeping the material at the right temperature reduces shrinkage. An injection mould company can adjust the mold temperature to optimize cooling.
Add Reinforcements
Some materials can be reinforced with fillers. These fillers help reduce shrinkage. They also improve the strength of the part. Mold makers use materials like glass fibers to reduce shrinkage in some projects. This technique is common in high-performance applications.
Increase Mold Cavity Size
A mold maker might increase the size of the mold cavity. They do this to allow for shrinkage. As the material cools and shrinks, it will still match the required dimensions. This is a useful technique for materials with high shrinkage rates.
Conclusion
Shrinkage is a challenge in injection molding. Mold makers and injection mould companies face this problem often. However, by understanding the causes and using improvement methods, they can reduce it. The key factors to control are pressure, cooling, and mold design. Using uniform thickness, proper materials, and packing pressure also helps. An experienced mold maker will know how to reduce shrinkage and improve part quality. Injection mould companies that focus on these methods will produce better parts.