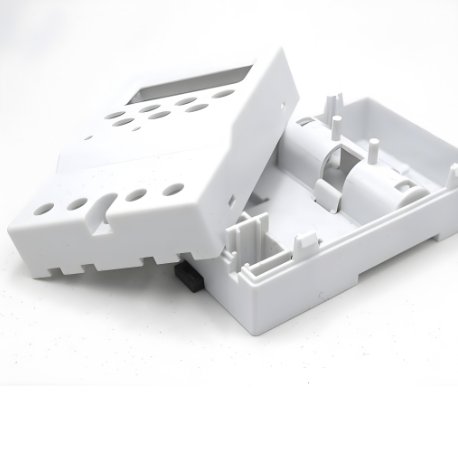
When creating plastic housings for electronics, consumer goods, or industrial devices, manufacturers must choose the right production method. The two most common options are housing injection molding and 3D printing. Each has its strengths and weaknesses. The best choice depends on part requirements, production volume, budget, and lead time.
While 3D printing is often seen as modern and flexible, housing injection molding remains the gold standard for mass production. A professional mold maker ensures high quality, repeatability, and strength. In this article, we compare both methods to help you choose the best one for your plastic housing projects.
What Is Housing Injection Molding?
Housing injection molding is a process where molten plastic is injected into a custom steel mold. After cooling, the plastic solidifies into the exact shape of the cavity. The mold is made by a mold maker, and once complete, it can produce thousands or millions of parts with consistent precision.
Key Benefits of Housing Injection Molding:
- Fast cycle time per part
- Excellent surface finish
- High dimensional accuracy
- Low cost per part at volume
- Strong mechanical properties
This method is ideal for projects that require durability, consistency, and large quantities.
What Is 3D Printing?
3D printing builds parts layer by layer from digital models. Also known as additive manufacturing, it uses materials like PLA, ABS, nylon, or resin. There are several technologies including FDM, SLA, and SLS.
Key Benefits of 3D Printing:
- No tooling required
- Great for prototypes
- Fast design changes
- Low upfront cost
- Easy customization
3D printing works best for one-offs, prototypes, or very low-volume production.
Comparison: Housing Injection Molding vs. 3D Printing
Let’s compare both processes across several important factors.
1. Part Quality and Strength
Housing injection molding delivers high strength, tight tolerances, and excellent surface finish. The pressure involved in the process compacts the plastic tightly, resulting in parts with consistent wall thickness and fewer voids.
3D-printed parts can be weaker, especially along the layer lines. Delamination, warping, and inconsistent thickness are common problems. FDM parts in particular may not be suitable for load-bearing or structural use.
✅ Winner: Housing Injection Molding
2. Production Speed
Once the mold is built by the mold maker, housing injection molding produces parts in seconds. A cycle time of 30 seconds or less is typical for housings. This makes it extremely fast for large volumes.
3D printing is much slower. A single housing can take several hours depending on size and complexity. Batch printing helps, but cannot match the speed of injection molding.
✅ Winner: Housing Injection Molding
3. Cost Efficiency
The cost equation changes depending on volume. For small runs (under 100 parts), 3D printing is cheaper. There’s no mold to make, and the setup is quick.
For high volumes (1,000 parts or more), housing injection molding becomes far more cost-effective. The upfront tooling cost is spread across all units. A skilled mold maker can build a durable mold that lasts for hundreds of thousands of cycles.
✅ Winner: Tie – depends on volume
4. Design Flexibility
3D printing excels at complex geometries. Internal channels, lattice structures, and undercuts can be built without tooling constraints. It allows fast design changes with minimal delay.
Housing injection molding has more limitations. Part design must follow molding rules—like draft angles, uniform wall thickness, and ejection clearance. However, with advanced tooling techniques, a good mold maker can still create complex housing designs.
✅ Winner: 3D Printing (for complex or evolving designs)
5. Material Options
Housing injection molding offers a wide range of engineering-grade plastics such as PC, ABS, PP, PA, and blends. Reinforced materials (glass-filled) or flame-retardant grades are also available. These materials are tested and trusted in real-world applications.
3D printing is limited to fewer materials. While high-performance filaments exist, many 3D-printed parts are not as durable or stable as injection-molded ones.
✅ Winner: Housing Injection Molding
6. Surface Finish
Housing injection molding produces smooth, clean finishes straight from the mold. A mold maker can even texture the mold to give the part a matte, glossy, or patterned surface.
3D-printed parts typically need post-processing to improve appearance. Layer lines are visible, and surfaces may feel rough or uneven.
✅ Winner: Housing Injection Molding
7. Tolerance Control
Precision matters in housing injection molding, especially for mating components or sealing applications. Molded parts typically have tight tolerances of ±0.1 mm or better.
3D printing often has looser tolerances. While SLA and SLS are better than FDM, they still may vary between prints. Dimensional repeatability is a challenge.
✅ Winner: Housing Injection Molding
When to Choose Each Method
Here’s a simple guideline:
Choose 3D Printing If:
- You need a prototype or concept model
- Quantity is low (under 100 pcs)
- You need rapid design iterations
- Complex internal geometry is required
Choose Housing Injection Molding If:
- You need 1,000 or more units
- Parts must be strong, consistent, and durable
- Surface finish and tight tolerance matter
- You want lower cost per part at scale
The Role of a Mold Maker
A great mold maker is essential for successful housing injection molding. They translate your CAD model into a steel tool, considering shrinkage, flow, and cooling.
The mold must:
- Deliver accurate shape
- Prevent defects (sink marks, warping, short shots)
- Withstand long production runs
- Allow for fast cycling and easy ejection
Investing in a professional mold maker ensures your plastic housings meet quality standards and reduce costly delays.
Final Verdict
Both housing injection molding and 3D printing have value. Each serves a different purpose. 3D printing gives you speed and flexibility for early design stages. Housing injection molding offers unbeatable part strength, surface finish, and cost efficiency for full production.
If you’re launching a new product, start with 3D printing. Once your design is locked in, partner with a trusted mold maker for production tooling. That way, you enjoy the best of both worlds—fast prototyping and reliable mass production.
Conclusion
Choosing the right method depends on your specific needs. But if you’re scaling up, housing injection molding is the smarter investment. It’s faster, stronger, and more precise—especially when backed by a skilled mold maker. While 3D printing shines in early-stage development, nothing beats the long-term performance and cost-efficiency of injection-molded plastic housings.
Whether you’re designing consumer electronics or industrial housings, let your project needs guide the decision—but remember: when quality and volume matter, housing injection molding leads the way.