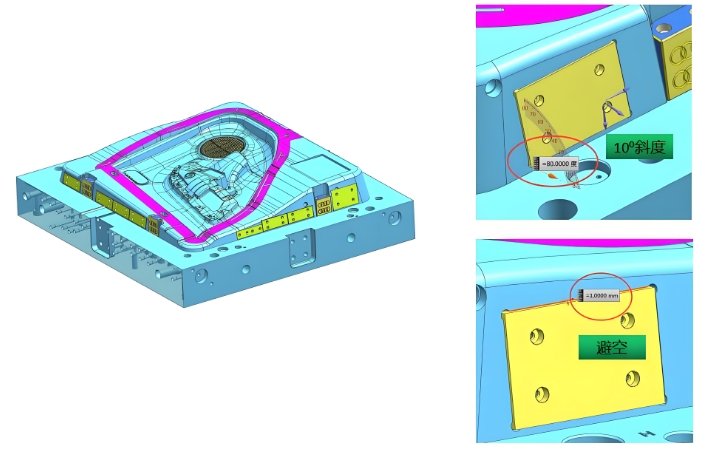
Automotive cooling systems need precision. Automotive injection molds create accurate parts. A skilled mold maker ensures durability. Proper mold design improves heat resistance and flow efficiency.
Key Cooling System Components
1. Radiator Housings
Radiator housings protect cores. Automotive injection molds shape durable housings. A mold maker ensures perfect fit and strength.
2. Coolant Reservoirs
Reservoirs store coolant. Automotive injection molds create leak-proof tanks. A mold maker selects heat-resistant plastics.
3. Water Pump Components
Water pumps circulate coolant. Automotive injection molds produce pump casings and impellers. A mold maker ensures smooth fluid movement.
4. Thermostat Housings
Thermostat housings regulate temperature. Automotive injection molds form precise enclosures. A mold maker ensures heat resistance.
5. Cooling Fan Blades
Cooling fans prevent overheating. Automotive injection molds shape aerodynamic blades. A mold maker balances weight and durability.
Materials for Automotive Cooling System Molds
1. Heat-Resistant Polymers
High temperatures demand strong materials. Automotive injection molds use PEEK and PPS plastics. A mold maker selects the best options.
2. Reinforced Nylon
Nylon adds strength. Automotive injection molds create impact-resistant parts. A mold maker ensures long-lasting performance.
3. ABS for Lightweight Durability
Lighter parts improve efficiency. Automotive injection molds use ABS for reservoirs. A mold maker enhances design flexibility.
4. Polypropylene for Chemical Resistance
Coolant contains chemicals. Automotive injection molds use polypropylene to prevent damage. A mold maker ensures proper formulation.
Types of Injection Molds for Cooling Components
1. Multi-Cavity Molds
Mass production needs efficiency. Automotive injection molds with multiple cavities increase output. A mold maker ensures uniformity.
2. Hot Runner Molds
Less waste, faster cycles. Automotive injection molds with hot runners improve material flow. A mold maker optimizes gating.
3. Insert Molding for Hybrid Parts
Some components combine plastic and metal. Automotive injection molds with insert molding integrate both. A mold maker enhances part strength.
4. Overmolding for Multi-Material Parts
Cooling parts need flexibility and strength. Automotive injection molds use overmolding for better performance. A mold maker ensures seamless bonding.
Precision in Mold Design for Cooling Components
1. Tight Tolerances for Leak Prevention
Cooling systems require zero leaks. Automotive injection molds create exact fits. A mold maker ensures tight tolerances.
2. Smooth Surface Finishes
Fluid flow depends on surface quality. Automotive injection molds with smooth finishes improve efficiency. A mold maker polishes every detail.
3. Uniform Wall Thickness
Uneven walls cause weak spots. Automotive injection molds ensure even thickness. A mold maker balances strength and flexibility.
4. Custom Cooling Channels in Molds
Mold cooling affects cycle time. Automotive injection molds with advanced cooling channels reduce warping. A mold maker optimizes heat dissipation.
Automation in Mold Manufacturing
1. CNC Machining for Precision
CNC machines improve accuracy. Automotive injection molds require perfect cutting. A mold maker programs high-precision machining.
2. Robotic Mold Handling
Robots enhance consistency. Automotive injection molds use automation for repeatability. A mold maker ensures defect-free parts.
3. AI-Powered Quality Control
Smart technology detects flaws. Automotive injection molds with AI reduce errors. A mold maker ensures top-tier quality.
4. Automated Injection Molding Machines
Less manual labor speeds production. Automotive injection molds work with automated presses. A mold maker fine-tunes machine settings.
Sustainability in Automotive Cooling Molds
1. Recycled Materials in Molding
Eco-friendly manufacturing matters. Automotive injection molds now use recycled plastics. A mold maker reduces waste.
2. Energy-Efficient Molding Machines
Less energy, more output. Automotive injection molds run on efficient machines. A mold maker optimizes power usage.
3. Waste Reduction Strategies
Scrap costs money. Automotive injection molds minimize excess. A mold maker implements lean production.
4. Biodegradable Polymers for Future Cooling Systems
Innovation supports sustainability. Automotive injection molds explore bio-based plastics. A mold maker researches greener materials.
Challenges in Manufacturing Cooling System Molds
1. High-Temperature Resistance
Coolant parts must endure heat. Automotive injection molds require heat-proof materials. A mold maker selects the best compounds.
2. Chemical Compatibility
Coolant fluids are corrosive. Automotive injection molds use resistant plastics. A mold maker ensures longevity.
3. Complex Part Geometries
Cooling parts have intricate shapes. Automotive injection molds must handle these designs. A mold maker ensures flawless execution.
4. Reducing Production Costs
Costs must stay low. Automotive injection molds with optimized designs save money. A mold maker balances quality and efficiency.
Future Trends in Cooling System Molding
1. AI-Designed Molds
AI improves mold design. Automotive injection molds get smarter. A mold maker uses data-driven optimization.
2. 3D Printing for Prototypes
Faster prototyping saves time. Automotive injection molds benefit from 3D-printed samples. A mold maker validates designs quickly.
3. Lightweight Cooling Components for EVs
Electric vehicles need lighter parts. Automotive injection molds reduce weight. A mold maker optimizes material selection.
4. Smart Cooling System Integration
Cars are getting smarter. Automotive injection molds create components for intelligent cooling systems. A mold maker adapts to new technologies.
Advanced automotive injection molds shape critical cooling parts. A skilled mold maker ensures precision, efficiency, and durability. The future of molding is faster, smarter, and more sustainable.