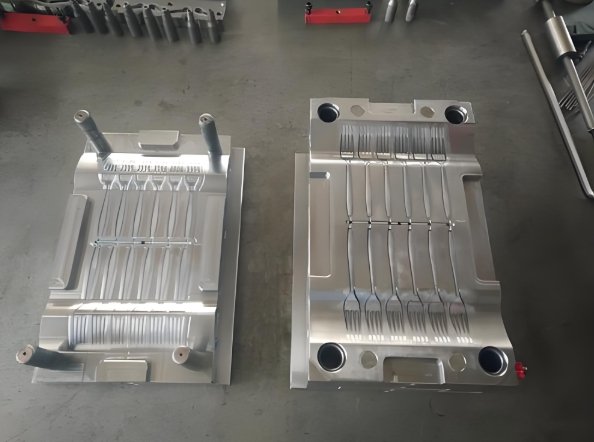
An injection mould company often faces the challenge of producing parts that meet specific requirements. One of the key ways to achieve this is through custom material blending. Custom material blending is the process of combining different materials to create a unique compound with specific properties. This technique is important for creating parts that need special characteristics, such as increased strength, flexibility, or resistance to harsh environments. In this article, we will explore how injection molding and custom material blending work together to provide high-quality, tailored solutions.
What is Custom Material Blending?
Custom material blending is the process of combining two or more materials to create a new material with specific properties. By mixing different materials, an injection mould company can develop compounds that meet the unique needs of their customers. The goal is to improve the performance of the final product, whether by making it stronger, more durable, or better suited to a particular environment.
Materials used in custom blending can range from plastics to metals, depending on the desired outcome. An experienced mold maker works with the client to select the best materials and determine the right blend for the application.
The Role of Injection Molding in Custom Material Blending
Injection molding is a manufacturing process in which melted material is injected into a mold to form a part. This process is versatile and can be used with a wide range of materials. For custom material blending, injection molding allows the blended material to be injected into the mold cavity, where it takes the desired shape.
The key advantage of using injection molding for custom material blending is that it allows for precision and consistency. The mold ensures that the blended material is shaped exactly as needed, with high levels of detail and accuracy. The injection mould company can adjust the process parameters, such as temperature and pressure, to ensure that the blended material flows smoothly and creates high-quality parts.
Custom Material Blending for Specific Properties
One of the main reasons companies opt for custom material blending is to achieve specific properties that cannot be found in a single material. For example, a client may need a part that is both lightweight and highly resistant to chemicals. By blending different materials, the injection mould company can create a compound that meets these requirements.
A mold maker plays an essential role in selecting the right combination of materials. They understand the properties of various materials and how they will interact with each other. This knowledge ensures that the final product has the desired characteristics, such as strength, durability, or flexibility.
Examples of Custom Material Blending in Injection Molding
There are several common applications for custom material blending in injection molding. Below are some examples of how an injection mould company can use material blending to enhance a product:
1. Automotive Industry
In the automotive industry, custom material blending is often used to create parts that are lightweight yet strong. For example, an injection mould company might blend plastics with glass fibers to create a compound that is both strong and light. This is ideal for parts like dashboards, door panels, and engine components. The custom blend ensures that the parts are durable enough to withstand the stresses of daily use, yet light enough to contribute to fuel efficiency.
2. Consumer Electronics
Consumer electronics often require materials that are heat-resistant and impact-resistant. In this case, injection molding with custom material blending can create materials that meet these demands. For example, blending thermoplastic materials with carbon fiber can create parts that are resistant to high temperatures while remaining lightweight. This is especially useful for parts like smartphone cases, laptop housings, and electrical connectors.
3. Medical Devices
Medical devices require materials that are biocompatible, sterilizable, and durable. Custom material blending is often used to meet these requirements. For instance, blending medical-grade plastics with other materials can create compounds that are resistant to chemicals and able to withstand sterilization processes. This is essential for creating medical tools, surgical instruments, and implantable devices.
4. Packaging
Packaging materials need to be both strong and flexible to protect the products they contain. By using custom material blending, an injection mould company can create materials that offer the right balance of strength, flexibility, and cost-effectiveness. For instance, blending different types of plastics can create packaging materials that are durable yet lightweight, perfect for food and beverage containers.
Advantages of Custom Material Blending
Custom material blending offers several advantages, including:
- Enhanced Performance: By blending different materials, an injection mould company can create a product with superior strength, flexibility, or resistance to heat or chemicals.
- Cost-Effective: Blending less expensive materials with more expensive ones can reduce costs while still achieving the desired performance.
- Tailored Solutions: Custom material blending allows the mold maker to create a material that meets the specific needs of the client.
- Increased Durability: Blended materials often perform better than standard materials, resulting in longer-lasting products.
The Role of Mold Makers in Custom Material Blending
A mold maker is essential to the success of custom material blending. The mold maker works closely with the injection mould company to select the best materials for the application. They ensure that the materials will blend well together and will perform as expected in the final product.
Once the materials have been selected, the mold maker designs the mold to accommodate the custom blend. The mold must be designed to ensure that the blended material flows smoothly and fills the mold cavity evenly. This is particularly important when working with materials that have different flow characteristics.
Challenges in Custom Material Blending
While custom material blending offers many benefits, it also comes with challenges. One of the main challenges is ensuring that the blended materials will work together as expected. Some materials may not blend well with others, which can lead to weak spots or defects in the final product. An experienced mold maker helps overcome these challenges by selecting materials that are compatible and designing molds that ensure a smooth flow of material.
Another challenge is achieving consistency in the blending process. Injection molding with custom material blends requires precise control over the temperature, pressure, and other factors. Any variations in these factors can lead to inconsistent results. An injection mould company ensures that the blending process is carefully monitored and controlled to ensure high-quality results.
Custom material blending is a powerful tool for creating products with specific properties. When combined with injection molding, this technique allows an injection mould company to produce high-quality, tailored products. The role of a mold maker is crucial in selecting the right materials and designing molds that ensure the success of the blending process. Custom material blending offers several advantages, including enhanced performance, cost-effectiveness, and increased durability. By working with an experienced injection mould company, businesses can achieve the custom solutions they need for their products.