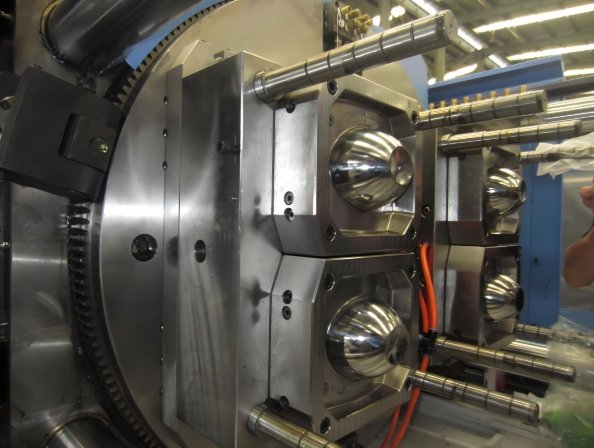
An injection mould company plays a key role in producing heat-resistant parts. The process of injection molding is well-suited to creating parts that must endure high temperatures. From automotive components to electronics, heat-resistant parts are crucial in many industries. Skilled mold makers ensure the molds are designed to handle extreme conditions, making sure the final product meets all requirements for durability and performance.
The Role of Injection Molding in Heat-Resistant Parts
Injection molding is a manufacturing process that involves injecting molten material into a mold. Once cooled, the material hardens into the desired shape. This method is highly effective for producing parts that require precise dimensions and tight tolerances, especially when dealing with heat-resistant materials. By using specialized polymers or composites, an injection mould company can produce parts that retain strength even at high temperatures.
Why Heat-Resistant Parts Matter
Heat-resistant parts are critical in many applications. They are used in areas where parts are exposed to high temperatures. For example, in the automotive industry, parts like engine components and exhaust systems must withstand extreme heat. In the electronics industry, devices like phone chargers and power supply units require components that don’t overheat.
Creating these parts using injection molding ensures they can withstand these conditions without degrading. The use of heat-resistant materials ensures long-lasting performance.
Advantages of Injection Molding for Heat-Resistant Parts
1. High Precision
Injection molding is known for its precision. This is especially important when creating heat-resistant parts. These parts must fit perfectly to work correctly under high temperatures. Injection mould companies use advanced machines to ensure the parts are made with accuracy. The mold maker ensures that every detail of the mold is precise, which helps in producing high-quality heat-resistant parts.
2. Material Variety
An injection mould company can use a variety of materials designed for high-heat applications. Injection molding can accommodate materials like:
- Heat-resistant plastics such as polyphenylene sulfide (PPS), polyetheretherketone (PEEK), and polyimide.
- Metallic materials like aluminum and stainless steel, which are ideal for heat-resistant parts in automotive and industrial applications.
The ability to choose the right material for each specific application is one of the key benefits of injection molding. Mold makers work with clients to select the best material that can handle the required temperature conditions.
3. Cost-Effective for High Volumes
Injection molding is highly cost-effective when producing heat-resistant parts in large quantities. After the initial mold creation, the cost per part decreases as production volume increases. An injection mould company can help businesses achieve cost savings while maintaining high quality. This makes injection molding a preferred method for industries that require large numbers of durable, heat-resistant parts.
4. Durability and Strength
Parts made with injection molding are known for their durability. Heat-resistant materials used in injection molding retain their strength even in extreme conditions. For example, heat-resistant plastics like PEEK are known to have high strength and resistance to wear and tear. These parts can be exposed to high temperatures without losing their structural integrity.
5. Complex Geometries
In many cases, heat-resistant parts require complex shapes and intricate details. Injection molding is capable of producing these complex geometries with ease. Whether the part has multiple cavities, intricate features, or specific thicknesses, injection molding can accommodate these designs. This is especially important in industries like electronics and automotive, where parts often need to meet both design and heat resistance standards.
The Role of Mold Makers in Heat-Resistant Parts Production
A mold maker plays a crucial role in creating heat-resistant parts. They design and build molds that are capable of withstanding high temperatures. A mold maker must understand the behavior of the materials used in injection molding under heat stress. This knowledge is essential to ensure the molds are durable enough to handle the pressures of high-temperature applications.
Mold makers also work closely with the design team to ensure the parts are engineered correctly. They ensure that the mold allows for proper cooling and that the material flows evenly into the cavity. This is especially important when working with heat-resistant materials that may have different cooling rates.
Common Applications for Heat-Resistant Parts
Heat-resistant parts are used in a variety of industries, including:
- Automotive: Engine components, exhaust systems, and heat shields need to endure high temperatures. Injection molding ensures these parts are both durable and precise.
- Electronics: Parts like connectors, housings, and cooling systems need to withstand high temperatures generated by electronic devices. Injection molding ensures these parts are heat-resistant while maintaining their functionality.
- Aerospace: Aircraft parts must be able to handle extreme temperatures without breaking down. Injection molding creates components that are both heat-resistant and lightweight.
- Industrial Equipment: Machinery parts like valves, pumps, and seals often operate in hot environments. Injection molding allows for the production of durable, heat-resistant parts for industrial use.
Challenges in Producing Heat-Resistant Parts with Injection Molding
Despite its advantages, producing heat-resistant parts using injection molding does come with challenges. One of the main challenges is selecting the right material for the application. Different heat-resistant materials have different properties, such as thermal expansion rates, strength, and flexibility. The mold maker must ensure the chosen material is compatible with the design and will perform well under high heat.
Another challenge is the high initial cost of creating the mold. For heat-resistant parts, the mold must be built with precision and durability in mind. While the initial costs can be high, these costs are offset by the cost-effectiveness of mass production.
An injection mould company provides a wealth of expertise in creating heat-resistant parts. Using injection molding, they can produce durable, high-quality parts that perform well in high-temperature applications. Whether it’s for the automotive, electronics, or aerospace industries, injection molding ensures that the parts meet the necessary heat resistance standards. The role of a skilled mold maker is essential in ensuring that the molds are designed for optimal performance. By choosing an experienced injection mould company, businesses can ensure they get the heat-resistant parts they need for their applications.