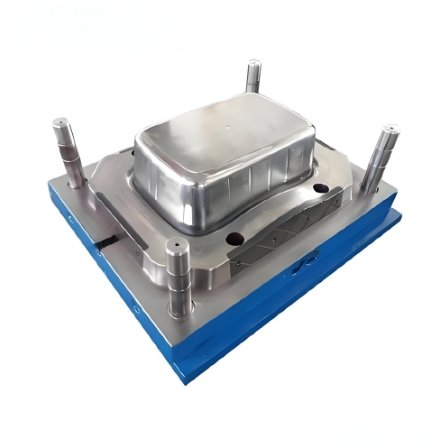
Lightweighting is becoming a key focus in many industries. Reducing the weight of products can save costs and improve efficiency. An experienced injection mould company plays a key role in achieving this goal. With the right injection molding techniques, companies can produce high-quality, lightweight products. This article explores the various methods used by an injection mould company to create lightweight solutions.
What is Lightweighting?
Lightweighting refers to the process of reducing the weight of a product while maintaining its performance and strength. For many industries, including automotive, aerospace, and consumer products, lightweighting is important. Lighter products are easier to handle, more energy-efficient, and more cost-effective. An injection mould company can use various injection molding techniques to produce lightweight products.
The Role of Injection Molding in Lightweighting
Injection molding is a widely used manufacturing process. It involves injecting molten material into a mold to create a specific shape. The process allows for high precision and complex designs. For lightweighting, an injection mould company uses injection molding to produce parts that are both strong and light. The materials used and the design of the mold are key factors in achieving a lightweight product.
Material Selection for Lightweighting
The first step in creating a lightweight product is choosing the right material. An injection mould company can work with a variety of materials, including plastics, metals, and composites. Each material has different properties, so selecting the right one is essential. Lightweight materials, such as reinforced plastics, are often used in injection molding for their strength-to-weight ratio.
Mold makers play a vital role in selecting the material. They understand the properties of different materials and how they will behave in the injection molding process. By choosing the right material, an injection mould company ensures that the final product will meet the weight and strength requirements.
Use of Thin-Walled Molding
Thin-walled molding is a technique used to create lightweight products. In this process, the wall thickness of the molded part is reduced while maintaining the part’s strength and functionality. This is a common technique used by injection mould companies for lightweighting solutions. The thinner walls reduce the amount of material used, which in turn reduces the weight of the final product.
Thin-walled molding requires precision. A skilled mold maker ensures that the mold is designed to support thin walls without compromising the structural integrity of the part. Injection molding with thin walls allows for faster production times and cost savings in material costs.
Incorporating Inserts and Reinforcements
Another way to achieve lightweighting is by incorporating inserts or reinforcements into the molded parts. These inserts can be made of materials such as metal or composite fibers. They help reinforce the strength of the part without adding significant weight. An injection mould company can use this technique to enhance the strength of lightweight plastic parts. This method is commonly used in automotive and aerospace industries, where both lightweight and strength are required.
A mold maker designs the mold to hold the inserts securely during the injection molding process. The insert is placed into the mold cavity before the injection of the plastic material. Once injected, the material bonds with the insert, creating a part that is both lightweight and strong.
Use of Gas-Assisted Injection Molding
Gas-assisted injection molding is another technique used by an injection mould company to create lightweight parts. In this process, gas is injected into the mold cavity along with the molten material. The gas creates hollow sections within the part, reducing the amount of material required. This results in a lightweight product with the desired shape and strength.
This technique is particularly useful for creating larger parts with complex shapes. The gas-assisted process helps reduce the material used and the weight of the part. It also allows for more uniform wall thicknesses, which improves the overall quality of the part.
Foaming and Microcellular Molding
Foaming is another method used to reduce the weight of injection-molded parts. In this process, a blowing agent is added to the material before it is injected into the mold. The agent causes the material to expand, creating small bubbles within the part. This creates a foam-like structure, which significantly reduces the weight of the part while maintaining its strength.
Microcellular molding is a more advanced version of foaming. It uses tiny gas bubbles to create an even lighter structure. An injection mould company can use foaming and microcellular molding to create lightweight parts with excellent mechanical properties. This technique is often used for parts that need to be both strong and light, such as automotive components.
Optimizing Mold Design for Lightweighting
An experienced mold maker plays a key role in optimizing the design of the mold for lightweighting. The mold design must support the manufacturing process while reducing the weight of the final product. By designing molds that are optimized for thin walls, inserts, and other lightweighting techniques, the injection mould company can create parts that meet both weight and strength requirements.
The mold must also allow for efficient material flow. Poor material flow can lead to defects or weak spots in the part, compromising its performance. A skilled mold maker ensures that the mold is designed to handle the material efficiently, which helps create a strong, lightweight part.
Reducing Material Waste
Reducing material waste is another important factor in lightweighting. An injection mould company works to minimize waste during the injection molding process. By optimizing the design of the mold and the injection molding process, the company ensures that the right amount of material is used for each part. This reduces waste and helps keep production costs low.
Using lightweight materials also helps reduce waste. Lighter materials tend to be less expensive and have a lower environmental impact. By choosing these materials, an injection mould company can help clients meet sustainability goals while still achieving high-quality products.
The Advantages of Lightweighting
Lightweighting offers several benefits. First, it can reduce production costs. Less material is needed, which means lower raw material costs. Second, lightweight parts are easier to handle and transport. This can reduce shipping and handling costs. In industries like automotive and aerospace, lightweight parts can also improve fuel efficiency and performance.
Working with a skilled injection mould company allows clients to take advantage of these benefits. By using advanced injection molding techniques, the company can create parts that are not only lightweight but also strong and durable.
Lightweighting is an important goal for many industries. An injection mould company uses a variety of techniques to create lightweight solutions. By choosing the right materials, using thin-walled molding, and incorporating inserts and reinforcements, an injection mould company can produce parts that are both lightweight and strong. Advanced techniques like gas-assisted molding, foaming, and microcellular molding help reduce the weight of the parts while maintaining their performance. With the help of a skilled mold maker, businesses can achieve the lightweight solutions they need for their products.