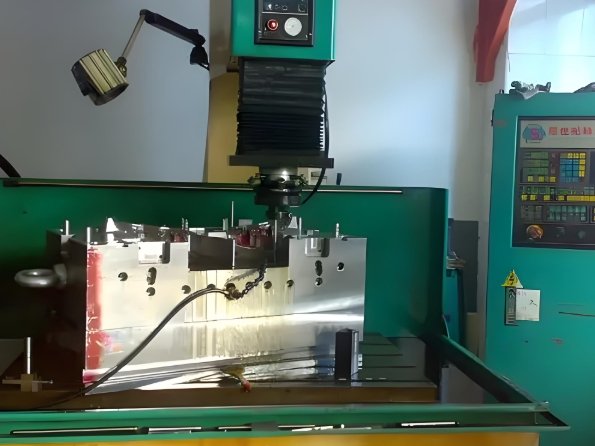
Uniform wall thickness is critical in injection molding. It ensures the quality and durability of products. Injection mould companies focus on precision to achieve this. Mold makers play a key role in creating designs that meet these standards. Advanced tools and methods are used to control thickness.
Why Uniform Wall Thickness Matters
Uniform walls reduce stress in products. Uneven thickness leads to warping and cracking. It also causes defects like sink marks. With consistent thickness, injection molds create stronger and more reliable parts.
Products with uniform walls are lighter and more efficient. They save material and cost. In injection molding, uniformity improves cycle times. Parts cool evenly, reducing production delays.
Challenges in Maintaining Uniform Thickness
Maintaining uniform walls is not easy. Complex designs often have varying features. Creating molds for these designs is challenging.
Material flow is another issue. Plastic flows unevenly in irregular shapes. This causes thickness variations. Cooling systems also impact wall uniformity. Poor cooling leads to inconsistent results.
Techniques Used by Injection Mould Companies
Injection mould companies use specific methods to ensure uniform walls.
- Flow Analysis
Mold makers use simulation software. These tools analyze plastic flow in the mold. Flow patterns reveal problem areas. Adjustments are made to improve consistency. - Proper Gate Placement
Gate placement controls material flow. Gates are positioned to distribute plastic evenly. This reduces thickness variations. - Balanced Cooling Channels
Cooling channels remove heat uniformly. Mold makers design channels to match the product’s shape. Balanced cooling prevents warping and shrinkage. - Uniform Mold Cavity Design
Mold cavities must have smooth transitions. Sharp corners are avoided. Smooth designs promote even material flow. - Material Selection
Material properties affect flow and cooling. Mold makers choose materials with consistent shrinkage rates. This improves wall uniformity. - Multi-Cavity Molds
Multi-cavity molds are used for large volumes. Each cavity is designed for uniform walls. This ensures consistency across all parts.
The Role of Mold Makers
Mold makers are crucial in achieving uniform walls. They create precise injection molds. Their expertise ensures designs meet industry standards.
Mold makers work closely with clients. They study product requirements. This helps create molds tailored to specific needs.
Experienced mold makers understand material behavior. They adjust mold designs based on material properties. This prevents issues during production.
How Injection Mould Companies Improve Wall Thickness
Injection mould companies invest in technology. CAD and CAE tools help design better molds. These tools simulate real-world conditions.
Automation improves consistency. Robots handle molding processes with precision. Automated systems monitor wall thickness in real-time.
Quality control is also important. Companies inspect molds before production. They test prototypes for wall uniformity. Clients receive accurate and reliable products.
Benefits of Uniform Wall Thickness
Uniform walls improve product strength. They reduce stress and prevent defects. Parts last longer and perform better.
Consistency saves material. Thin, uniform walls use less plastic. This lowers production costs.
In injection molding, uniform walls improve cooling. Faster cooling reduces cycle times. Companies produce parts faster and more efficiently.
Innovations in Wall Thickness Control
Technology continues to advance. Smart sensors are now used in molds. These sensors measure wall thickness during production. They provide instant feedback to adjust the process.
AI is helping mold makers. AI predicts issues in mold designs. It suggests changes to improve wall uniformity.
Nanotechnology is also emerging. Nano-additives enhance material flow. This ensures better thickness control in complex designs.
Sustainability is another focus. Many companies use eco-friendly materials. These materials maintain uniform walls without harming the environment.
Applications of Uniform Wall Thickness
Uniform walls are essential in many industries. Automotive parts need consistent strength. Uneven thickness weakens structural integrity.
In medical devices, precision is key. Uniform walls ensure functionality and safety.
Consumer goods benefit from better aesthetics. Products with even walls look and feel premium.
Electronics use uniform parts for better performance. Consistent thickness improves fit and durability.
Future Trends in Wall Thickness Control
The future of wall thickness control looks promising. Smart factories are adopting advanced techniques. AI and IoT will play a bigger role in injection molding.
Sustainability will remain important. Companies will continue to use recyclable materials. Eco-friendly practices will dominate the industry.
Collaboration will increase. Injection mould companies and material scientists will work together. This will lead to better materials and designs.
Uniform wall thickness is critical in injection molding. It improves product quality, strength, and efficiency. Injection mould companies use advanced techniques to meet these demands.
Mold makers design precise injection molds. Their expertise ensures consistent results. Innovations like AI and smart sensors improve the process further.
As technology evolves, wall thickness control will become even more precise. Clients can expect better products from trusted injection mould companies. The future of injection molding looks bright with these advancements.