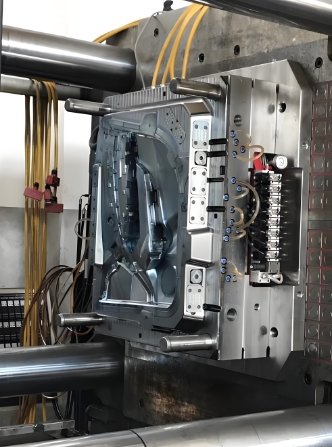
The automotive industry is evolving. New automotive injection molds improve production. A skilled mold maker ensures accuracy and durability. Innovation drives better efficiency, speed, and cost savings.
Advancements in Automotive Injection Molding
1. High-Precision CNC Machining
Accuracy is critical. CNC machining improves automotive injection molds. A mold maker programs machines for extreme precision.
2. 3D Printing for Rapid Prototyping
Speed matters. 3D printing accelerates mold development. Automotive injection molds benefit from faster testing. A mold maker verifies designs quickly.
3. Smart Mold Monitoring Systems
Sensors track performance. Automotive injection molds use real-time data. A mold maker detects defects early.
4. Hot Runner Technology
Material waste is a problem. Hot runners eliminate excess plastic. Automotive injection molds become more efficient. A mold maker reduces scrap.
5. Conformal Cooling Channels
Faster cooling improves production. Automotive injection molds with conformal cooling cut cycle times. A mold maker optimizes cooling paths.
Materials for Advanced Automotive Injection Molds
1. Hardened Steel for Durability
Tough molds last longer. Automotive injection molds use hardened steel. A mold maker ensures maximum strength.
2. Aluminum for Faster Production
Aluminum molds cool quickly. Automotive injection molds benefit from rapid processing. A mold maker selects aluminum for speed.
3. High-Performance Polymers
Some molds use engineered plastics. Automotive injection molds with polymer cores reduce costs. A mold maker balances durability and expense.
Types of Advanced Automotive Injection Molds
1. Multi-Cavity Molds for High Output
More cavities mean faster production. Automotive injection molds increase efficiency. A mold maker reduces cycle time.
2. Family Molds for Complex Parts
One mold, multiple parts. Automotive injection molds with family designs save costs. A mold maker improves part alignment.
3. Two-Shot Molding for Dual Materials
Two materials, one process. Automotive injection molds with two-shot designs improve part function. A mold maker ensures seamless transitions.
4. Insert Molding for Hybrid Components
Plastic and metal combine. Automotive injection molds integrate metal inserts. A mold maker strengthens final parts.
Automation in Automotive Injection Molding
1. Robotic Mold Handling
Automation boosts precision. Automotive injection molds use robotic arms. A mold maker programs seamless operations.
2. AI-Powered Defect Detection
Smart systems prevent defects. Automotive injection molds with AI catch issues early. A mold maker ensures quality control.
3. Automated Material Feeding
No manual loading needed. Automotive injection molds with automated feeding speed up production. A mold maker optimizes material flow.
4. Real-Time Production Analytics
Data drives efficiency. Automotive injection molds collect real-time data. A mold maker makes adjustments instantly.
Sustainability in Automotive Injection Molding
1. Recycled Plastic Usage
Eco-friendly production is key. Automotive injection molds use recycled resins. A mold maker reduces environmental impact.
2. Energy-Efficient Machines
Less power, better output. Automotive injection molds now work with energy-efficient equipment. A mold maker minimizes waste.
3. Biodegradable Polymers
Future cars need sustainable parts. Automotive injection molds support bio-based plastics. A mold maker explores new materials.
4. Waste Reduction Techniques
Scrap costs money. Automotive injection molds with optimized gating reduce excess. A mold maker ensures maximum material usage.
Applications of Advanced Automotive Injection Molds
1. Interior Components
Seats, dashboards, and trim need precision. Automotive injection molds shape these parts. A mold maker ensures seamless production.
2. Exterior Body Parts
Bumpers, grilles, and side panels require strength. Automotive injection molds create durable parts. A mold maker ensures perfect fit.
3. Engine and Under-the-Hood Parts
Heat resistance is essential. Automotive injection molds shape durable engine components. A mold maker selects the best materials.
4. Lighting and Electronic Housings
Transparent and heat-resistant plastics are crucial. Automotive injection molds form complex lighting parts. A mold maker ensures optical clarity.
Future Trends in Automotive Injection Molding
1. AI-Designed Molds
Smart algorithms improve design. Automotive injection molds become more efficient. A mold maker leverages AI for precision.
2. Lightweighting for EVs
Electric vehicles need lighter parts. Automotive injection molds optimize material use. A mold maker ensures strength with less weight.
3. Digital Twin Technology
Virtual testing saves time. Automotive injection molds benefit from digital simulations. A mold maker perfects molds before production.
4. Smart Factories
Fully automated plants are coming. Automotive injection molds will integrate with Industry 4.0 systems. A mold maker will work alongside AI and robotics.
New technologies push automotive injection molds forward. A skilled mold maker ensures precision, efficiency, and cost savings. The future of molding is smarter, faster, and more sustainable.