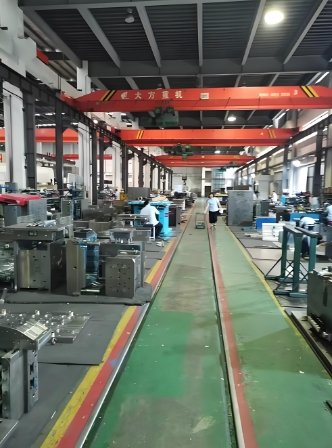
Injection molding is a precise and efficient manufacturing process. Cooling plays a big role in the process. Cooling time affects the quality of injection molds and production speed. Advanced cooling systems have become essential. An injection mould company must focus on innovation to stay competitive.
Why Cooling is Critical
Cooling reduces defects in injection molds. Warping and shrinking often occur without proper cooling. Temperature control improves accuracy and surface finish. Injection molding cycles depend heavily on cooling systems. Faster cooling leads to higher output.
Mold makers design cooling channels carefully. A good cooling system keeps the mold at the right temperature. This ensures even cooling across the product.
Innovations in Cooling
Technology has brought new cooling methods. Modern injection mould companies use advanced systems. These systems reduce cooling time and improve efficiency.
- Conformal Cooling Channels
Conformal cooling channels are 3D-printed. They follow the mold’s shape closely. This allows even cooling. Heat is removed quickly and uniformly. Many mold makers prefer this method. - High-Performance Coolants
New coolants are faster and more efficient. These fluids remove heat better than traditional ones. Injection molds stay cool even during high-speed production. - Automated Cooling Systems
Automation improves cooling precision. Sensors monitor mold temperature in real-time. Automated systems adjust the cooling process instantly. This ensures constant quality in injection molding. - Vacuum-Assisted Cooling
This innovation removes trapped air from the mold. It improves heat transfer and reduces defects. Vacuum-assisted cooling is ideal for thin-wall products. - Dynamic Mold Temperature Control
Mold makers now use dynamic systems. These systems heat and cool the mold at specific times. This helps produce better details in complex designs.
Benefits of Advanced Cooling Systems
Advanced cooling systems benefit every injection mould company. Faster cooling shortens the production cycle. This increases efficiency. Improved cooling also reduces energy consumption. Companies save on costs while being environmentally friendly.
For mold makers, innovative cooling systems reduce defects. They produce better-quality injection molds. Customers get consistent and reliable products.
Challenges in Cooling
Despite advances, challenges remain. Designing cooling systems for complex molds is difficult. Injection molding often involves intricate designs. Cooling channels must match the mold’s geometry.
Another challenge is maintenance. Cooling systems must work under extreme conditions. Regular maintenance is critical. Improper care leads to inefficiency.
Some injection mould companies face cost barriers. Advanced systems can be expensive. Smaller businesses may struggle to adopt them. However, the long-term benefits outweigh the costs.
How Mold Makers Solve Cooling Challenges
Mold makers focus on research and development. They invest in tools like CAD software. These tools help design efficient cooling channels.
Collaboration with material experts also helps. Choosing the right materials for injection molds is vital. Some materials transfer heat better than others. Mold makers often choose materials that balance strength and cooling efficiency.
Regular maintenance ensures smooth operation. Many injection mould companies schedule inspections. They clean cooling systems to prevent blockages.
Future Trends in Cooling Systems
The future looks bright for cooling technology. Smart systems are on the rise. These systems use AI to monitor and adjust cooling. AI can predict issues before they occur.
Sustainability is another trend. Many companies aim to reduce their carbon footprint. Eco-friendly coolants and energy-efficient systems are becoming popular.
Nanotechnology is also gaining attention. Nanofluids enhance heat transfer. This technology could revolutionize cooling in injection molding.
Cooling systems are critical in injection molding. They improve product quality and production speed. Innovations continue to shape the industry. Mold makers and injection mould companies benefit from these advancements.
Investing in advanced cooling is a smart choice. It ensures better efficiency and higher-quality injection molds. The future of cooling in injection molding looks promising. Advanced systems will continue to enhance the industry.