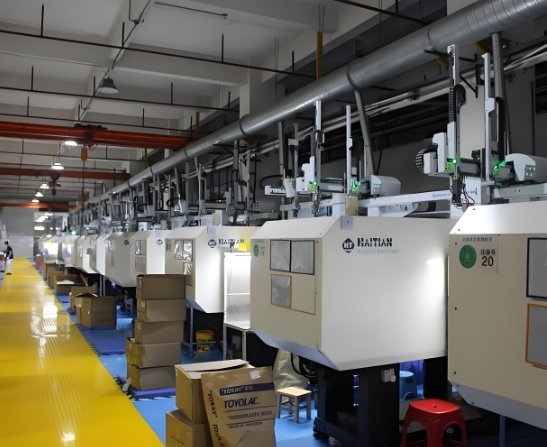
Speed matters.
So does quality.
In today’s world, waste is not an option.
Electronic Injection Molding must be fast and lean.
A smart Mold Maker knows how to do this.
They cut waste.
They boost output.
They save costs.
Let’s explore lean strategies.
And how they change electronic part production.
What Is Lean Manufacturing?
Lean means less waste.
Less downtime.
More value.
It focuses on flow.
It improves every step.
In Electronic Injection Molding, lean is vital.
It keeps the line moving.
It reduces cost.
It helps Mold Makers stay ahead.
Why Lean Matters in Electronics
Electronics need precision.
Tolerances are tight.
Time-to-market is short.
Mistakes cost money.
Wasted parts hurt margins.
Lean helps prevent all that.
And it keeps customers happy.
Key Lean Principles in Electronic Injection Molding
1. Value Stream Mapping
Map every step.
From mold design
to final packing.
Look for delays.
Look for waste.
A skilled Mold Maker helps with this.
They understand each point.
2. Just-In-Time Production
Make what you need.
When you need it.
No big inventory.
No storage waste.
This keeps costs down.
It keeps flow smooth.
Electronic Injection Molding runs faster this way.
Parts go straight from mold
to the next step.
3. Continuous Improvement
Always improve.
Fix small problems daily.
This is called Kaizen.
Mold Makers who follow lean
review every mold run.
They ask,
“How can we make this better?”
4. Standard Work
Every operator works the same way.
Same steps.
Same tools.
This reduces errors.
And cuts downtime.
In molding, repeatability means quality.
5. 5S Workplace Organization
Sort.
Set in order.
Shine.
Standardize.
Sustain.
Keep the shop clean.
Keep tools in place.
This saves time.
And boosts safety.
In Electronic Injection Molding, it improves part quality too.
Role of the Mold Maker in Lean
A Mold Maker is key to lean success.
They design the mold.
They choose the steel.
They set the cooling.
A lean mold runs faster.
With fewer defects.
Smart Mold Makers use simulation.
They predict part flow.
They reduce warpage.
They ensure balance.
They also plan for easy maintenance.
That means less downtime.
And longer tool life.
Reducing Cycle Time
Cycle time affects cost.
Less time = more parts.
Use hot runners.
Use high-flow resins.
Use quick-cooling molds.
Your Mold Maker will know what works best.
In Electronic Injection Molding, fast cycles save thousands.
Reducing Defects and Scrap
Scrap costs money.
And time.
Lean molds are precise.
They use venting.
They have balanced gates.
Mold Makers inspect every mold.
They test every shot.
They stop defects before mass production.
Using Automation in Lean Molding
Automation saves labor.
And reduces human error.
Robots remove parts.
Sensors check sizes.
Conveyors move bins.
Everything flows.
A Mold Maker can design molds
ready for automation.
In Electronic Injection Molding, this cuts cost
and speeds delivery.
Real-Time Monitoring
Modern presses collect data.
They track pressure.
They watch temperature.
This data goes to dashboards.
It shows trends.
It helps fix problems fast.
Lean systems use this data daily.
It helps the team improve.
Quick Mold Changes
In lean, changeovers must be fast.
Use mold carts.
Use pre-set settings.
Use smart controllers.
With a good Mold Maker,
tools change in minutes.
Not hours.
This allows flexible production.
And smaller batch sizes.
Flexible Tooling
Lean loves flexibility.
Use inserts.
Use modular molds.
One base.
Many parts.
Your Mold Maker can help plan this.
It saves money.
And saves space.
Training and Cross-Training
Lean teams know their work.
And their neighbor’s work too.
Train everyone.
Keep them sharp.
This means fewer mistakes.
And faster response.
Electronic Injection Molding benefits greatly
from a skilled team.
Visual Controls
Use signs.
Use lights.
Use labels.
Show the current status.
Let everyone see the flow.
It helps managers.
It helps workers.
And it keeps production smooth.
Supplier Involvement
A lean factory needs lean suppliers.
Your Mold Maker must deliver fast.
And deliver right.
Choose partners who understand lean.
On-time.
In spec.
No excuses.
Preventive Maintenance
Don’t wait for tools to break.
Fix before failure.
Clean molds regularly.
Check alignment.
Polish runners.
A top Mold Maker builds easy-to-maintain molds.
That keeps uptime high.
Using SMED (Single-Minute Exchange of Die)
SMED means fast mold swaps.
Less than 10 minutes.
This allows more flexibility.
And smaller orders.
Your Mold Maker must plan this during design.
It saves hours every week.
Results of Lean in Electronics
Lower costs.
Fewer rejects.
Faster lead times.
Better customer reviews.
Lean helps win more business.
It helps Electronic Injection Molding stay competitive.
And it helps Mold Makers grow with customers.
Lean is not a buzzword.
It’s a real strategy.
And it works.
From mold design
to packing,
lean cuts waste.
And boosts value.
Electronic Injection Molding needs speed.
And precision.
Lean provides both.
Work with a smart Mold Maker.
One who knows lean.
And builds for the future.