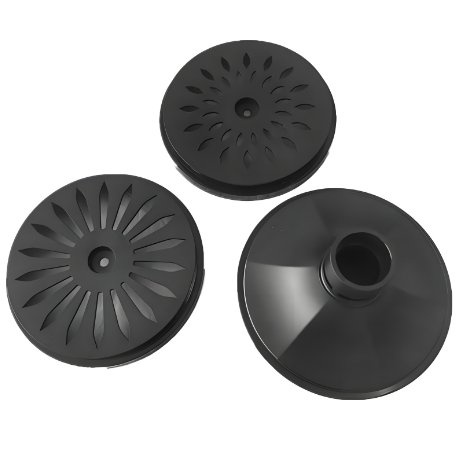
In today’s world, lighting fixtures are more than just sources of illumination. They are part of our home décor, workspaces, and public environments. Whether it’s a ceiling lamp, a wall sconce, or a modern LED tube light, each fixture needs a strong and stylish housing. That’s where Housing Injection Molding becomes essential.
Housing Injection Molding is a fast and cost-effective way to produce plastic housings for lighting fixtures. These housings are durable, fire-resistant, and can be customized for shape, size, and finish. Behind every successful molded housing is an experienced Mold Maker. The Mold Maker creates the precision mold tools that give shape and detail to each part.
This article will explore why Housing Injection Molding is the top choice for making lighting housings and how the Mold Maker plays a vital role in this process.
The Importance of Housing in Lighting Fixtures
Lighting housings serve several key functions:
- Protect internal parts – They shield wiring, LED boards, and drivers.
- Support heat dissipation – Some are designed with vents or fins.
- Improve safety – Flame-retardant materials prevent fire risks.
- Add style – Smooth finishes and custom colors match décor themes.
From a basic lamp cover to a complex industrial light fixture, plastic housings are found in nearly every type of light. Housing Injection Molding provides a reliable way to make these components with accuracy and repeatability.
What Is Housing Injection Molding?
Housing Injection Molding is a manufacturing method where molten plastic is injected into a mold cavity. The plastic cools and hardens, taking the exact shape of the mold. The result is a solid plastic part that needs little or no extra finishing.
Lighting fixture housings require high precision, attractive surfaces, and excellent material performance. Housing Injection Molding delivers all of these while allowing for mass production at a reasonable cost.
This method also supports the creation of complex shapes, thin walls, and integrated design features such as clips, holes, and vents.
The Role of the Mold Maker
The success of any Housing Injection Molding project depends heavily on the Mold Maker. A Mold Maker is a specialist who designs, builds, and maintains the steel molds used in the injection molding machines.
Here’s what the Mold Maker does:
- Creates detailed 3D designs for the mold
- Selects the right steel and components
- Ensures proper cooling and ejection systems
- Polishes surfaces to get the desired texture or gloss
- Tests and adjusts the mold for perfect fit and function
Lighting housings often have intricate shapes and surface details. A skilled Mold Maker ensures these are replicated perfectly in every shot.
Materials Used in Lighting Fixture Housing Injection Molding
Choosing the right plastic is key. Lighting fixtures need materials that are:
- Heat-resistant
- Flame-retardant
- UV-stable (for outdoor use)
- Strong and lightweight
Common materials include:
- Polycarbonate (PC) – Great for transparency and heat resistance
- Acrylonitrile Butadiene Styrene (ABS) – Easy to mold, strong, and low-cost
- Polyamide (Nylon) – Tough and heat-stable
- PC/ABS blends – A mix of strength, toughness, and aesthetics
The Mold Maker must account for each material’s behavior. Different plastics shrink and flow differently. The mold must be designed to match the chosen resin.
Types of Lighting Housings Made by Injection Molding
There are many lighting products that benefit from Housing Injection Molding, such as:
- Ceiling light covers
- Tube light enclosures
- Floodlight housings
- LED panel frames
- Decorative lamp bases
- Outdoor light casings
Each type requires special features. Outdoor lights may need waterproof seals. Ceiling lights often have screw mounts and diffusers. Injection molding allows all these to be molded as one part or as a few easy-to-assemble parts.
The Benefits of Using Housing Injection Molding in Lighting
There are many advantages to using Housing Injection Molding for lighting fixture production:
1. High Precision
Each molded part is nearly identical to the next. This is important when multiple parts must fit together tightly.
2. Fast Production
Once the mold is ready, thousands of parts can be produced quickly. This keeps up with demand in a fast-moving market.
3. Cost Savings
Large production runs reduce the per-part cost. Plus, minimal post-processing is needed.
4. Design Flexibility
Want a smooth white ceiling light or a textured black outdoor fixture? Housing Injection Molding supports it.
5. Strength and Safety
The right plastic and mold design ensure the housing meets mechanical and fire safety standards.
6. Lightweight and Durable
Plastic housings are lighter than metal, which is ideal for ceiling and wall-mounted products.
These advantages are only possible when the Mold Maker does their job right. A poor mold can cause defects like sink marks, flash, or part warpage.
Challenges in Lighting Housing Production
Despite the benefits, there are challenges in molding lighting housings:
- Thin walls – Risk of short shots or incomplete filling
- Clear materials – Require smooth, clean molds to avoid blemishes
- Heat build-up – Needs smart cooling channel design
- Complex shapes – May require slides or lifters in the mold
The Mold Maker must solve these with smart mold design, material selection, and process control.
Quality Control in Lighting Housing Injection Molding
To ensure product quality, the Mold Maker and molding team conduct several checks:
- Dimensional inspection – To ensure proper fit with other parts
- Visual inspection – To catch surface defects
- Functional testing – To check impact resistance, heat tolerance, etc.
Reliable quality control ensures each lighting fixture housing is safe, attractive, and ready for assembly.
Real-World Applications
Let’s look at some actual uses:
- A PC molded LED ceiling light housing that resists heat and keeps its shape
- A textured ABS garden lamp case with built-in mounts and UV protection
- A clear polycarbonate lamp cover for industrial warehouse lighting
- A nylon floodlight housing with cooling fins and waterproof seals
All these were made using Housing Injection Molding with molds crafted by expert Mold Makers.
In the lighting industry, success depends on both form and function. Light housings must be strong, heat-resistant, and visually appealing. Housing Injection Molding delivers all this and more. It’s fast, efficient, and ideal for mass production.
But the real hero behind the scenes is the Mold Maker. Without their careful design, precision tooling, and attention to detail, even the best molding machine can’t produce quality parts.
When choosing a partner for lighting fixture production, look for experience in Housing Injection Molding and mold-making. A skilled Mold Maker ensures your product performs well, lasts long, and looks great.