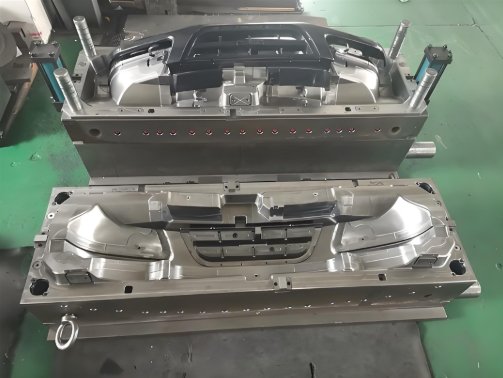
The demand for lightweight automotive parts is rising. Automotive Injection Molds play a vital role in meeting this need. Skilled Mold Makers create precise molds for such parts. These molds reduce weight without sacrificing strength.
Why Lightweight Parts Matter
1. Fuel Efficiency
Light parts improve fuel economy. Vehicles consume less energy with reduced weight.
2. Reduced Emissions
Lower weight leads to fewer emissions. This helps meet environmental regulations.
3. Improved Performance
Lighter vehicles accelerate faster. They also handle better on the road.
Role of Automotive Injection Molds
1. Precision Manufacturing
Injection molds ensure accurate designs. They create parts that fit perfectly.
2. Material Versatility
Molds work with lightweight plastics. These materials combine strength with low weight.
3. Repeatability
Injection molds allow mass production. Every part remains consistent in quality.
Benefits of Lightweight Parts
1. Cost Savings
Lighter materials reduce production costs. Shipping also becomes cheaper.
2. Sustainability
Recyclable plastics make manufacturing greener. This supports eco-friendly initiatives.
3. Durability
Advanced plastics withstand wear and tear. Lightweight parts last longer in vehicles.
How Mold Makers Create Lightweight Parts
1. Material Selection
Expert Mold Makers choose the best materials. These include polymers like polypropylene and ABS.
2. Design Optimization
CAD tools refine mold designs. This minimizes material use without losing strength.
3. Precision Tooling
CNC machines cut molds with high accuracy. This ensures perfect part dimensions.
4. Prototyping and Testing
Prototypes verify the mold’s performance. Adjustments improve results before mass production.
Innovations in Lightweight Mold Design
1. Advanced Cooling Systems
Cooling channels reduce production time. Faster cycles mean more parts in less time.
2. 3D Printing for Prototypes
3D printing speeds up prototype development. It also reduces design costs.
3. AI-Assisted Designs
AI tools optimize mold structures. They suggest ways to reduce weight further.
Challenges in Lightweight Parts Production
1. Material Limitations
Not all plastics suit automotive needs. Some lack the required strength or durability.
2. Higher Initial Costs
Advanced molds require significant investment. However, savings occur over time.
3. Precision Requirements
Lightweight parts need tight tolerances. Small errors can lead to defects.
Applications of Lightweight Parts
1. Interior Components
Dashboards, door panels, and seats are lighter now. Injection molds ensure a perfect fit for these parts.
2. Exterior Panels
Bumpers and fenders benefit from reduced weight. These parts remain durable and impact-resistant.
3. Engine Components
Plastic engine covers and housings reduce vehicle weight. They also withstand high temperatures.
4. Battery Cases
Electric vehicles use lightweight battery casings. This increases their range and efficiency.
How to Choose the Right Mold Maker
1. Experience
An experienced Mold Maker ensures quality molds. They understand industry needs.
2. Technology
Choose a provider with advanced tools. Modern equipment improves precision and efficiency.
3. Support
A reliable Mold Maker offers ongoing assistance. This includes design updates and maintenance.
Trends in Lightweight Automotive Molds
1. Reinforced Plastics
New materials combine plastic with fibers. This adds strength without increasing weight.
2. Sustainable Materials
Recycled plastics are becoming common. These materials reduce environmental impact.
3. Smart Molds
Sensors monitor mold performance. This ensures consistent quality.
Future of Lightweight Parts
1. Stronger Plastics
Ongoing research develops better materials. These plastics will further replace metals.
2. Increased Automation
Robots will handle more of the manufacturing process. This will improve speed and accuracy.
3. Personalization
Custom molds will meet unique design needs. This supports diverse automotive styles.
Why Lightweight Parts Dominate the Market
Lightweight parts meet modern demands. They save fuel, cut costs, and reduce emissions. Automotive Injection Molds make these parts possible. Skilled Mold Makers refine the process continually.
Efficient manufacturing relies on lightweight solutions. Automotive Injection Molds are central to this innovation. Experienced Mold Makers ensure top-quality molds for lightweight parts. Their expertise supports the automotive industry’s evolution.
Choosing the right Mold Maker is critical for success. With advanced processes and materials, the future of lightweight automotive parts looks promising.