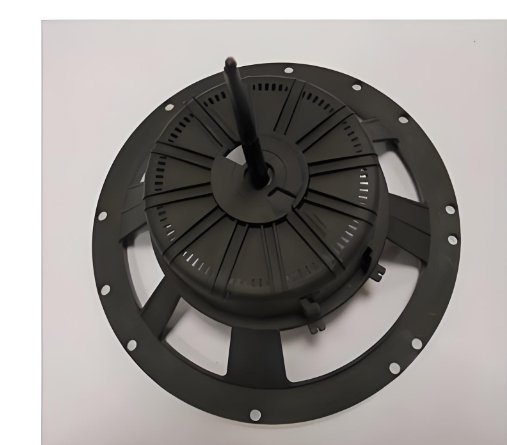
Electronic Injection Molding often involves extreme heat. This heat is needed to melt plastic. It also helps the plastic flow into thin, detailed molds. But high heat brings many problems.
To solve them, you need a smart plan. And you need a skilled Mold Maker. A good mold design can control heat. It can stop defects before they happen.
Let’s look at the top problems caused by heat. And see how the right Mold Maker can help.
1. Why High Heat Is Needed
Plastic must be melted to flow. In Electronic Injection Molding, many parts are thin. They also have sharp corners and tiny features.
Heat helps the plastic fill the mold fast. Without heat, flow stops. Parts come out short or incomplete.
2. Problems from Too Much Heat
While heat helps flow, too much can harm the part. Here are some common issues:
- Burn marks
- Warping
- Brittleness
- Discoloration
- Deformation
Each of these can ruin a part. And in electronics, that means product failure.
3. Burn Marks on Parts
Burn marks appear as black or brown spots. These are caused by trapped air. When plastic flows too hot and fast, it burns the air.
A smart Mold Maker will add vents in key spots. These vents let air escape. That stops burning in Electronic Injection Molding.
4. Deformed or Warped Parts
When some areas cool faster than others, warping happens. Heat shrink is also a problem. It changes the shape of the part.
To fix this, the Mold Maker balances cooling. They add cooling lines where needed. That keeps the whole mold at the right temperature.
5. Weak Spots in Parts
High heat can damage plastic strength. If the temperature is too high, bonds break. That makes parts brittle.
A skilled Mold Maker picks the right temperature. They also adjust cycle time. That helps plastic stay strong during Electronic Injection Molding.
6. Choosing the Right Plastic
Not all plastics handle heat the same. Some melt at low temps. Some resist high heat well. Choosing the wrong one can lead to cracks or burns.
A good Mold Maker helps pick the best material. They test flow, heat resistance, and shrinkage. In Electronic Injection Molding, material choice matters.
7. Controlling Mold Temperature
The mold itself must stay cool. If the mold gets too hot, parts stick. Flash and warping increase.
The Mold Maker designs channels for water or oil cooling. They place them where heat builds up. That keeps molding stable.
8. Heater Placement in the Mold
Too much or too little heat in one area causes problems. Balanced heat flow is important.
The Mold Maker places heaters with care. They avoid hot spots. This makes Electronic Injection Molding more reliable.
9. Thermal Expansion Issues
Heat makes metals expand. That includes the mold. If the mold shifts during use, parts change shape.
To prevent this, the Mold Maker uses heat-resistant steel. They calculate expansion before making the mold. This protects part shape and fit.
10. Short Shots from Cold Zones
Sometimes the mold cools too fast in spots. This stops flow. Parts come out incomplete. These are called short shots.
In Electronic Injection Molding, the Mold Maker studies flow paths. They place gates and runners to guide plastic evenly. They heat these zones if needed.
11. Protecting Inserts and Metal Parts
Many electronic parts include metal pins or inserts. Heat can melt glue or weaken bonding.
The Mold Maker isolates inserts with special cooling. This keeps parts safe during the hot process.
12. Using Hot Runners the Right Way
Hot runners help keep the plastic warm inside the mold. But if not balanced, they can overheat.
A good Mold Maker uses thermal sensors. These control the heat inside each runner. That keeps Electronic Injection Molding stable.
13. Fixing Discoloration Issues
Heat can change the plastic color. This happens if plastic stays too long in the barrel or nozzle.
To avoid this, the Mold Maker keeps flow paths short. They also adjust screw speed and back pressure. That keeps plastic fresh and clean.
14. Improving Part Surface Quality
Heat also affects how smooth a part looks. Too much heat can make surfaces rough or dull.
With better temperature control, the Mold Maker ensures a clean surface. This improves product look and feel.
15. Using Mold Flow Analysis
Before molding starts, software helps predict heat issues. Flow analysis shows hot spots, slow zones, and shrink areas.
The Mold Maker uses this data to fix problems before production. That improves results in Electronic Injection Molding.
16. Balancing Pressure and Heat
Heat and pressure must work together. If heat is too high but pressure is low, parts don’t fill. If pressure is high but heat is low, cracks form.
A skilled Mold Maker balances both. They test different settings. That brings the best output.
17. Shorter Cycle Time without Overheating
Long heat times raise cost. But fast cycles risk defects.
The Mold Maker uses efficient cooling and heat control. That shortens cycles. But part quality stays high in Electronic Injection Molding.
18. Making Repairs for Heat Damage
Old molds suffer from heat wear. Cracks form. Vents clog. Steel softens.
A trusted Mold Maker repairs damaged areas. They add heat shields or new cooling lines. This keeps molds running longer.
19. Improving Part Fit and Assembly
Heat changes part size. This affects how well it fits with other parts.
By adjusting mold shrinkage settings, the Mold Maker ensures a perfect fit. That helps with later assembly in electronics.
Heat is both friend and enemy in Electronic Injection Molding. It melts plastic and fills the mold. But too much heat causes cracks, warping, and burns.
A skilled Mold Maker knows how to manage this heat. They design smart cooling. They balance flow and pressure. They test and tweak every detail.
Good heat control means better parts. It means longer mold life. And it means fewer defects.
If you want success in Electronic Injection Molding, work with a proven Mold Maker. Your parts—and your customers—will thank you.