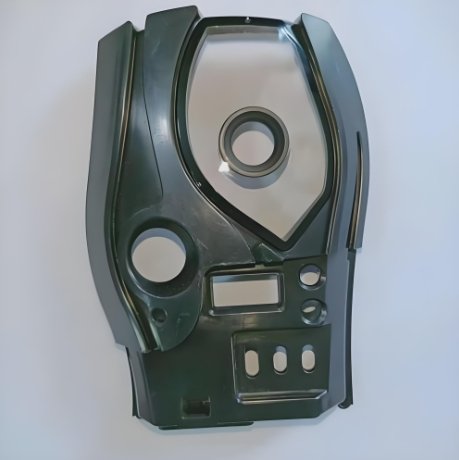
When producing medical devices, precision and cleanliness are essential. Any contamination or deviation can result in product failure or even patient harm. That’s why choosing a medical Injection Molding Company with cleanroom production and a highly skilled Mold Maker team is critical for healthcare manufacturers. In this article, we explore the vital role cleanroom molding plays in medical plastics, the importance of expert mold making, and how to select the right Injection Molding Company for your project.
What Is Cleanroom Injection Molding?
Cleanroom injection molding is a process where plastic parts are produced in a controlled environment with minimal airborne particles. Medical-grade cleanrooms are classified based on the number of particles per cubic meter of air. Most medical parts are manufactured in ISO Class 7 or ISO Class 8 cleanrooms.
A qualified Injection Molding Company operating in such environments ensures that parts are not only precise but also sterile or contaminant-free. This is essential for applications like syringes, diagnostic cartridges, surgical devices, and implants.
Along with a clean environment, precision molds created by an experienced Mold Maker ensure each part is dimensionally stable and performs consistently.
Why Cleanroom Molding Matters in Medical Applications
In the medical field, cleanliness is not a bonus—it’s a requirement. Regulatory bodies like the FDA and ISO demand strict adherence to hygiene and quality standards. Cleanroom injection molding offers several advantages:
- Reduces particulate contamination
- Supports sterilization-ready parts
- Ensures compatibility with sensitive internal body systems
- Allows for in-line packaging in sterile conditions
- Meets global compliance standards
When a certified Injection Molding Company and skilled Mold Maker come together, you get parts that meet all requirements, every time.
The Role of the Mold Maker in Cleanroom Molding
A Mold Maker plays a vital role in medical-grade molding. Even the cleanest environment can’t compensate for poor mold design or tool wear. Cleanroom standards demand perfect surfaces, tight tolerances, and long-lasting performance.
A professional Mold Maker ensures:
- Smooth, polished mold cavities for easy release
- Minimal parting lines to avoid contamination traps
- Accurate venting and gating for defect-free parts
- Materials and coatings that prevent bacterial growth
- Long mold life for consistent quality over time
A poor mold leads to defects, which leads to waste, recalls, and risk. A great Mold Maker eliminates these issues before they arise.
Key Features of a Medical Injection Molding Company
1. ISO 13485 Certification
Top-tier Injection Molding Companies meet ISO 13485, which governs quality systems for medical devices.
2. FDA-Approved Materials
Only FDA-compliant resins like medical-grade polypropylene, polycarbonate, PEEK, and TPU should be used.
3. Cleanroom Facility
Class 7 or Class 8 certified environments are required for most medical components. Some companies offer Class 5 for ultra-sensitive items.
4. In-House Mold Maker Team
Having in-house tooling experts speeds up production, lowers costs, and improves quality control.
5. Full Validation Services
IQ, OQ, and PQ validation is essential for FDA and global compliance.
Common Medical Products Made with Cleanroom Injection Molding
A specialized Injection Molding Company with a cleanroom setup can produce a wide range of items:
- Diagnostic housings
- Blood collection devices
- Surgical handles
- Implant delivery systems
- Dental components
- Drug delivery systems (inhalers, injectors)
- Catheter parts and fluid connectors
Each item must meet exact specifications, which is only possible when both the Injection Molding Company and the Mold Maker understand medical-grade expectations.
Case Study: Class 7 Cleanroom for Diagnostic Components
A diagnostics firm needed high-clarity, sterile diagnostic cassette housings. These components required cleanroom production, FDA-compliant materials, and tight tolerances.
A trusted Injection Molding Company provided Class 7 cleanroom molding, while its Mold Maker designed and fabricated precision steel tooling with mirror-finish cavities. The result was high-yield, crystal-clear housings with zero flash and consistent performance across thousands of cycles.
The parts passed FDA validation with minimal adjustments and began commercial production within weeks.
How to Choose the Right Medical Injection Molding Partner
Ask the following:
- Are your facilities ISO 13485 certified?
- Do you operate an ISO Class 7 or Class 8 cleanroom?
- What FDA-compliant materials do you support?
- Is your Mold Maker team in-house or outsourced?
- Do you perform full mold and process validation?
- Can you handle small batch and high-volume production?
The answers will help you identify if a company is truly equipped to handle your medical molding needs.
Why In-House Mold Making Matters
Many companies outsource mold making, which increases lead times and costs. A full-service Injection Molding Company with an in-house Mold Maker team offers:
- Faster turnaround on new molds
- Lower costs and higher accountability
- Easier design iterations and refinements
- Faster maintenance and reduced downtime
- Tighter quality integration between mold and molded part
This synergy is especially important in cleanroom environments, where a defective mold can halt the entire production line.
Innovations in Medical Molding
Medical-grade Injection Molding Companies are adopting new technologies to improve outcomes:
- Automated vision systems for inline defect detection
- Multi-material molding for devices that combine soft and rigid parts
- Micro-molding for small and precise parts under 1 gram
- Laser marking for traceability without contamination risk
These innovations only work if the Mold Maker can create tooling to support them. Therefore, toolmaking must evolve alongside molding technologies.
Conclusion
In the competitive and highly regulated field of healthcare, quality cannot be compromised. Partnering with a cleanroom-capable Injection Molding Company backed by an expert Mold Maker ensures precision, cleanliness, and compliance.
Whether you’re producing surgical tools, drug delivery devices, or diagnostic components, choose a company that combines cleanroom molding with FDA expertise and precision tooling. Your product’s success—and your patient’s safety—depend on it.