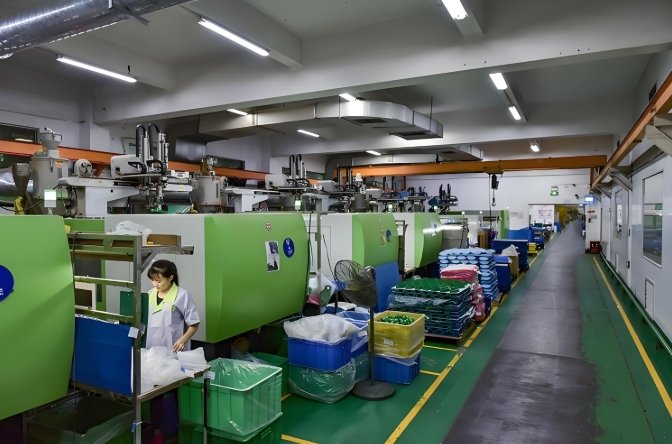
Surgical instruments require extreme precision. They must be durable, sterile, and safe. Medical injection molding is the best way to produce them. It allows for high-volume, consistent manufacturing. Mold makers create the tools needed for this process. They design and build the molds that form medical instruments.
Why Choose Medical Injection Molding?
1. High Precision and Consistency
Surgical instruments need exact dimensions. Even small errors can cause failures. Medical injection molding ensures uniform production. Every part meets strict specifications.
2. Cost-Effective Production
Traditional manufacturing is slow and expensive. Medical injection molding reduces costs. Once the mold is created, thousands of instruments can be produced quickly.
3. Biocompatible and Safe Materials
Surgical instruments must be safe for human use. Mold makers choose medical-grade plastics. These materials are biocompatible and non-toxic.
4. Sterilization Resistance
Surgical tools must withstand sterilization. Some require heat, radiation, or chemical cleaning. Medical injection molding allows for materials that resist these processes.
Key Materials for Surgical Instruments
1. Polyetheretherketone (PEEK)
PEEK is strong and resistant to chemicals. It is used for implants and reusable tools.
2. Polycarbonate (PC)
Polycarbonate is tough and transparent. It is ideal for instrument housings and handles.
3. Polypropylene (PP)
Polypropylene is flexible and resistant to chemicals. It is used in disposable instruments.
4. Acrylonitrile Butadiene Styrene (ABS)
ABS is durable and impact-resistant. It is common in hand-held medical devices.
The Role of a Mold Maker in Surgical Instrument Production
1. Designing the Mold
A mold maker starts by designing the mold. It must meet precise dimensions and material flow requirements.
2. Manufacturing the Mold
The mold is then created using high-precision machining. It must withstand high temperatures and repeated use.
3. Testing and Quality Assurance
Each mold undergoes testing. Sample parts are produced and inspected for defects.
4. Maintenance and Longevity
Molds wear down over time. Regular maintenance ensures they produce consistent parts.
Types of Surgical Instruments Made with Medical Injection Molding
1. Handheld Surgical Tools
Scalpels, forceps, and clamps are made using medical injection molding. These tools must be durable and lightweight.
2. Endoscopic and Laparoscopic Instruments
Minimally invasive surgeries require small, complex tools. Injection molding ensures precision and ergonomic designs.
3. Disposable Medical Devices
Syringes, retractors, and catheters are often single-use. Injection molding makes them cost-effective and sterile.
4. Instrument Handles and Casings
Plastic handles improve grip and comfort. Mold makers design ergonomic, user-friendly shapes.
Challenges in Medical Injection Molding for Surgical Tools
1. Meeting Strict Regulations
Medical devices must meet FDA and ISO standards. Every step must ensure compliance.
2. Choosing the Right Material
The material must be strong, safe, and resistant to sterilization. Mold makers select the best option for each instrument.
3. Achieving High Precision
Even small errors can make a tool unusable. Advanced molding techniques ensure accuracy.
4. Maintaining Sterility During Production
Molding facilities must follow cleanroom standards. Any contamination can be dangerous.
Advanced Techniques in Medical Injection Molding
1. Micro Molding for Tiny Parts
Some surgical instruments require microscopic parts. Micro molding allows for extreme precision.
2. Multi-Shot Molding for Complex Designs
Multi-shot molding combines different plastics in one part. This allows for advanced, multi-functional tools.
3. Automation for High Efficiency
Robotic systems improve speed and reduce human error. Automated medical injection molding ensures quality and consistency.
4. Sustainable and Biodegradable Plastics
New eco-friendly materials are emerging. These reduce medical waste and improve sustainability.
Medical injection molding plays a key role in surgical instrument production. It ensures high precision, safety, and cost-efficiency. Mold makers design and build the molds that create reliable medical tools. As technology advances, medical injection molding will continue to shape the future of surgery.