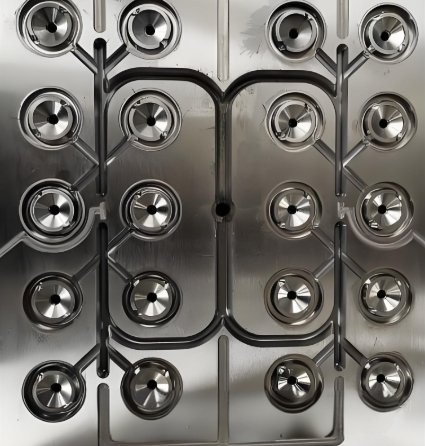
The use of FDA-approved plastics in medical injection molding is critical. These plastics ensure that medical devices meet strict safety and regulatory standards. A mold maker must carefully select materials that are approved by the FDA. This guarantees that the final products are safe for use in healthcare.
Why FDA-Approved Plastics Matter in Medical Injection Molding
1. Safety First
The FDA (Food and Drug Administration) is responsible for ensuring the safety and effectiveness of medical devices. FDA-approved plastics are tested to meet strict health and safety standards. These materials ensure that medical products are safe for patients and healthcare professionals.
2. Regulatory Compliance
The FDA approval process involves a series of tests. These tests check for biocompatibility, chemical resistance, and durability. Medical injection molding using FDA-approved plastics ensures that the final product complies with all regulatory requirements.
3. Risk Reduction
Using FDA-approved plastics minimizes the risk of device failures or adverse reactions. Medical devices made with unapproved materials may cause irritation or other harmful effects. With FDA-approved plastics, patients are protected from such risks.
Types of FDA-Approved Plastics for Medical Injection Molding
1. Polycarbonate (PC)
Polycarbonate is one of the most commonly used FDA-approved plastics. It is durable, transparent, and strong. It is used in a wide range of medical devices, such as diagnostic equipment, syringes, and surgical instruments.
2. Polypropylene (PP)
Polypropylene is lightweight, flexible, and resistant to chemicals. It is often used for medical containers, packaging, and syringes. It is FDA-approved and commonly used in disposable medical products.
3. Polyethylene (PE)
Polyethylene is another FDA-approved plastic used in medical injection molding. It is available in various forms, such as high-density (HDPE) and low-density (LDPE). It is commonly used for medical tubing, packaging, and bags.
4. Polyetheretherketone (PEEK)
PEEK is a high-performance plastic that is FDA-approved for medical applications. It is biocompatible, strong, and resistant to high temperatures. It is commonly used in implants, surgical instruments, and medical devices that need to withstand harsh conditions.
5. Medical-Grade Silicone
Silicone is biocompatible and flexible, making it suitable for a wide range of medical applications. Medical-grade silicone is FDA-approved for use in implants, seals, and other medical devices. It is durable and resistant to extreme temperatures.
6. Polylactic Acid (PLA)
Polylactic acid is a biodegradable plastic that is FDA-approved for certain medical applications. It is commonly used for tissue scaffolding and drug delivery systems. PLA is an environmentally friendly material that is safe for medical use.
Choosing FDA-Approved Plastics for Medical Injection Molding
1. Biocompatibility
Biocompatibility is one of the most critical factors when selecting FDA-approved plastics. The material must not cause adverse reactions when in contact with the human body. A mold maker must ensure that the chosen plastic passes biocompatibility testing.
2. Durability and Strength
Medical devices must be durable and able to withstand the conditions they will be exposed to. FDA-approved plastics like polycarbonate and PEEK are strong, resistant to wear and tear, and able to handle high-stress environments.
3. Sterilization Resistance
Medical devices often need to be sterilized before use. The plastic material must be resistant to common sterilization methods like autoclaving, gamma radiation, and ethylene oxide. Many FDA-approved plastics, such as polypropylene and medical-grade silicone, can withstand these processes without degrading.
4. Chemical Resistance
Medical devices are exposed to various chemicals, including disinfectants, bodily fluids, and drugs. FDA-approved plastics must be resistant to these chemicals to prevent degradation. Materials like polypropylene and polyethylene are known for their excellent chemical resistance.
5. Transparency and Clarity
Certain medical devices require transparency, such as syringes, diagnostic equipment, and IV components. FDA-approved plastics like polycarbonate offer excellent transparency, allowing healthcare professionals to monitor the contents or condition of the device.
The Role of a Mold Maker in FDA-Approved Medical Injection Molding
1. Selecting the Right Materials
A skilled mold maker plays a crucial role in the selection of FDA-approved plastics. They must choose the material that best suits the device’s requirements. The mold maker ensures that the plastic meets the necessary performance and regulatory standards.
2. Ensuring Compliance
A mold maker ensures that the materials used in medical injection molding comply with FDA guidelines. They are responsible for ensuring that the manufacturing process adheres to all regulatory requirements. This helps avoid any delays in approval or issues during product testing.
3. Quality Control
Quality control is essential when using FDA-approved plastics. The mold maker ensures that the plastic used in the injection molding process meets all specifications. They check for defects and ensure that each part is produced to the highest standard.
4. Precision and Accuracy
Medical devices require precision and accuracy. A mold maker uses advanced technology and equipment to ensure that each mold is created accurately. This ensures that the final product meets all design specifications and regulatory standards.
Challenges in Medical Injection Molding with FDA-Approved Plastics
1. Material Cost
FDA-approved plastics can be more expensive than non-approved materials. While the cost may be higher, the benefits of safety, durability, and compliance outweigh the costs. A mold maker must balance material costs with the need for high-quality products.
2. Supply Chain Issues
FDA-approved plastics may have limited availability or long lead times. This can delay production schedules. A mold maker must plan ahead and work closely with suppliers to ensure that materials are available when needed.
3. Complex Regulatory Requirements
The FDA approval process is stringent and can be time-consuming. Medical device manufacturers must navigate these regulations to ensure compliance. A mold maker plays a vital role in ensuring that the materials and manufacturing processes meet all regulatory standards.
The Future of Medical Injection Molding with FDA-Approved Plastics
1. Advances in Material Science
New FDA-approved plastics are being developed that offer better performance, biocompatibility, and sustainability. Innovations in material science will continue to improve medical injection molding processes and expand the possibilities for medical devices.
2. Sustainable Materials
There is a growing demand for sustainable and eco-friendly materials in the medical industry. The development of biodegradable and recyclable FDA-approved plastics will help reduce the environmental impact of medical device production.
3. Personalized Medical Devices
As medical technology advances, there is a growing focus on personalized medicine. FDA-approved plastics will play a crucial role in the production of custom medical devices tailored to individual patient needs.
Medical injection molding using FDA-approved plastics is essential for producing safe, reliable, and high-quality medical devices. A mold maker plays a critical role in selecting the right materials and ensuring compliance with all regulatory requirements. By using FDA-approved plastics, manufacturers can ensure that their products meet the highest standards of safety and effectiveness, ultimately improving patient care and outcomes.