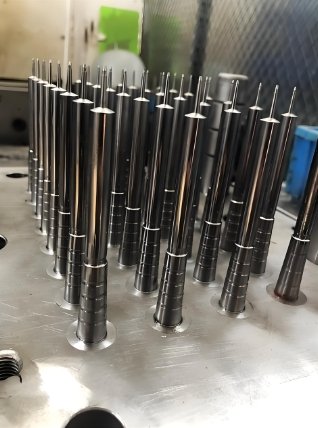
The choice of medical plastics in medical injection molding is crucial. These materials must meet strict requirements. They need to be safe, durable, and compliant with health regulations. A mold maker plays a significant role in choosing the right plastic materials for medical devices. The wrong choice can lead to device failure or health risks.
1. Why Medical Plastics Matter in Injection Molding
Medical plastics are used in various devices. They are essential in creating safe, functional, and reliable products. Medical injection molding turns these plastics into parts used in everything from syringes to implants. Without proper material selection, the final product could fail.
2. Key Characteristics of Medical Plastics
1. Biocompatibility
Biocompatibility is one of the most important factors. The plastic must not harm the body. It must not cause irritation, allergic reactions, or toxic responses. Medical injection molding uses plastics that are specifically designed for biocompatibility.
2. Sterilization Resistance
Medical devices often require sterilization. The material must withstand methods like autoclaving, gamma radiation, or ethylene oxide. A mold maker chooses plastics that won’t degrade under these conditions.
3. Durability
Medical devices need to last. Plastics used in injection molding must be durable. They must resist wear, tear, and damage over time. This is especially important for devices that are used frequently or need to last for years.
4. Chemical Resistance
Plastics used in medical devices need to resist chemicals. These include disinfectants, drugs, and bodily fluids. Materials that degrade when exposed to chemicals can compromise the device’s performance.
5. Mechanical Properties
Medical plastics need to have the right strength, flexibility, and impact resistance. Some devices need rigid plastics, while others require flexibility. Mold makers must choose materials that meet these specific needs.
6. Transparency
Certain medical devices, such as syringes or diagnostic equipment, require transparency. Transparent plastics allow visibility of the contents or the condition of the device.
3. Types of Medical Plastics Used in Injection Molding
1. Polypropylene (PP)
Polypropylene is commonly used in medical injection molding. It is durable, lightweight, and resistant to chemicals. It is often used for medical containers, packaging, and syringes.
2. Polyethylene (PE)
Polyethylene is flexible, resistant to chemicals, and commonly used in medical tubing, packaging, and other applications. It is available in several forms, including high-density (HDPE) and low-density (LDPE).
3. Polycarbonate (PC)
Polycarbonate is known for its strength and transparency. It is often used in diagnostic equipment, surgical instruments, and other medical devices that require both clarity and durability.
4. Polyetheretherketone (PEEK)
PEEK is a high-performance polymer used in medical implants and surgical instruments. It is biocompatible, strong, and resistant to high temperatures. It is ideal for long-term implants.
5. Medical-Grade Silicone
Silicone is biocompatible and flexible, making it ideal for implants, seals, and gaskets. It can withstand extreme temperatures and is resistant to wear and tear.
6. Polylactic Acid (PLA)
PLA is a biodegradable plastic. It is often used in medical devices that are designed to break down over time. It is useful for tissue scaffolding and drug delivery applications.
4. Selecting the Right Medical Plastic for Injection Molding
1. Consider the Device’s Purpose
The first step in material selection is understanding the device’s function. Some devices require rigid plastics, while others need flexibility. The mold maker will consider the device’s purpose to ensure the right material is chosen.
2. Regulatory Requirements
Medical devices must comply with strict regulatory standards. Materials must meet FDA and ISO guidelines. A mold maker ensures the chosen plastic meets all these regulations to avoid costly delays and ensure patient safety.
3. Assess the Manufacturing Process
The injection molding process itself can affect the material choice. Some plastics flow better and fill molds more easily. The mold maker will consider factors like shrinkage, flowability, and cooling time to select the best material.
4. Consider the End-User
The end-user, typically healthcare professionals or patients, must be considered. Materials must be safe for use and easy to handle. A mold maker takes into account how the device will be used in real-world scenarios.
5. Common Challenges in Medical Plastic Selection
1. Cost Considerations
Medical-grade plastics can be expensive. While choosing cheaper materials might seem tempting, it could lead to product failures or safety issues. A mold maker must balance cost with the performance required by the device.
2. Supply Chain Issues
Some materials are difficult to obtain or have long lead times. This can delay production. Mold makers must plan for material sourcing to ensure that the production process runs smoothly.
3. Environmental Impact
Some plastics are harmful to the environment. There is a growing push for using biodegradable and eco-friendly plastics. Manufacturers need to assess the environmental impact of their material choices.
4. Material Compatibility with Existing Equipment
Not all injection molding equipment works with every type of plastic. Some materials require specific equipment or conditions. A mold maker ensures that the chosen plastic is compatible with the equipment used in the process.
6. Future Trends in Medical Plastics for Injection Molding
1. Biodegradable Plastics
There is a growing interest in biodegradable materials for medical devices. These materials break down over time, reducing medical waste.
2. Smart Plastics
Smart plastics are materials that change in response to environmental stimuli, such as temperature or pH. These materials could revolutionize drug delivery systems and medical diagnostics.
3. Nanotechnology
Nanotechnology is being used to create more durable, biocompatible plastics. It allows for finer control over the material’s properties, which could improve device performance and safety.
Choosing the right plastic material for medical injection molding is essential for producing high-quality, reliable medical devices. The selected materials must be safe, durable, and compliant with regulations. A skilled mold maker carefully selects the right plastics to ensure the device performs as expected. The proper material can greatly impact the device’s success and longevity.