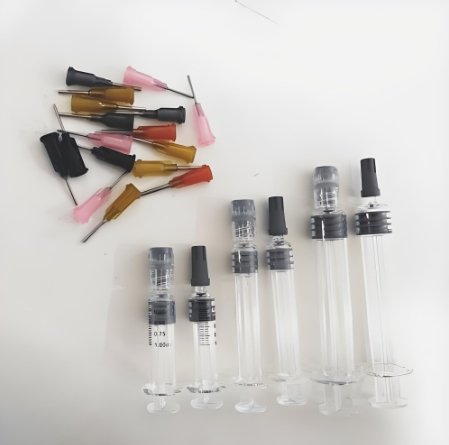
Medical devices must meet strict quality standards. Medical injection molding is a key process in manufacturing these devices. To ensure safety, compliance is essential. Mold makers play a crucial role in maintaining these standards. This article explores how medical injection molding meets industry regulations.
Why Standards Matter in Medical Injection Molding
1. Patient Safety
Defective medical parts can cause serious harm. Meeting industry standards ensures product safety.
2. Regulatory Compliance
Government agencies require strict compliance. Standards like FDA and ISO ensure that medical devices are reliable.
3. Product Consistency
Every molded part must meet the same specifications. Quality standards ensure that products work as intended.
4. Reducing Manufacturing Risks
Following industry standards helps prevent defects. This reduces recalls, saving time and money.
Key Industry Standards for Medical Injection Molding
1. FDA 21 CFR Part 820
- Outlines quality system regulations for medical device manufacturing.
- Requires strict documentation and quality control measures.
2. ISO 13485
- Ensures that medical devices meet international quality standards.
- Requires a quality management system for all production processes.
3. ISO 14971: Risk Management for Medical Devices
- Focuses on identifying and minimizing risks.
- Ensures that manufacturers control potential failures in production.
4. Good Manufacturing Practices (GMP)
- Ensures consistency in medical device production.
- Covers facility cleanliness, equipment maintenance, and employee training.
5. ISO 10993: Biocompatibility Testing
- Ensures that materials used in medical devices are safe.
- Prevents toxic reactions when materials come into contact with the human body.
6. ISO 14644: Cleanroom Standards
- Regulates air purity and contamination levels in cleanrooms.
- Essential for sterile medical device manufacturing.
Role of the Mold Maker in Meeting Medical Standards
1. Precision Mold Design
- Mold makers design molds that meet tight tolerances.
- Proper mold design ensures product consistency.
2. High-Quality Material Selection
- Medical devices require FDA-approved materials.
- Mold makers choose biocompatible plastics for safety.
3. Regular Mold Maintenance
- Clean molds prevent defects in medical parts.
- Mold makers ensure molds are properly maintained and inspected.
4. Process Validation
- Every molding process must be tested and validated.
- Mold makers ensure the process consistently produces defect-free parts.
Best Practices for Meeting Medical Injection Molding Standards
1. Strict Quality Control Measures
- Automated inspection systems detect defects.
- Regular testing ensures each part meets specifications.
2. Detailed Documentation and Traceability
- Manufacturers must keep records of each production run.
- Traceability helps identify defects and prevents recalls.
3. Implementing Cleanroom Manufacturing
- Cleanrooms minimize contamination risks.
- Following ISO 14644 ensures sterile production.
4. Employee Training and Certification
- Workers must understand FDA and ISO regulations.
- Ongoing training ensures compliance with new industry standards.
5. Working with Certified Suppliers
- Only FDA-approved materials should be used.
- Suppliers must provide documentation for material traceability.
Challenges in Meeting Medical Injection Molding Standards
1. Complex Regulatory Requirements
- Standards frequently change, requiring constant updates.
- Non-compliance can lead to fines and recalls.
2. High Cost of Compliance
- Investing in cleanrooms, automation, and testing increases costs.
- Compliance is necessary but requires significant resources.
3. Maintaining Precision in High-Volume Production
- Producing millions of identical parts is challenging.
- Small deviations can lead to non-compliance.
4. Preventing Material Contamination
- Even small contaminants can ruin medical components.
- Strict handling and storage guidelines must be followed.
Advanced Technologies for Meeting Standards
1. AI-Powered Quality Control
- AI detects defects faster than human inspectors.
- Automated systems improve accuracy and efficiency.
2. 3D Printing for Mold Prototyping
- Allows testing of molds before full production.
- Reduces errors and improves mold design.
3. Smart Manufacturing with IoT
- Sensors track molding conditions in real-time.
- Ensures compliance by monitoring temperature, pressure, and humidity.
4. Blockchain for Supply Chain Transparency
- Improves traceability of medical-grade materials.
- Ensures all components meet regulatory requirements.
Future Trends in Medical Injection Molding Compliance
1. Increased Automation
- Robots will reduce human error in manufacturing.
- AI will optimize the injection molding process.
2. Stricter Environmental Regulations
- Manufacturers will adopt eco-friendly medical plastics.
- Sustainability will become a key factor in compliance.
3. Digital Quality Control Systems
- Smart cameras and sensors will improve defect detection.
- Digital records will streamline compliance documentation.
4. Customization in Medical Device Manufacturing
- Personalized medical devices will require more flexible molding processes.
- Advanced mold designs will allow for faster adjustments.
Meeting industry standards in medical injection molding is essential for safety and compliance. Mold makers play a key role in ensuring precision and reliability. By following FDA, ISO, and GMP guidelines, manufacturers can produce high-quality medical devices. As technology advances, compliance will become more efficient, improving quality and patient safety.