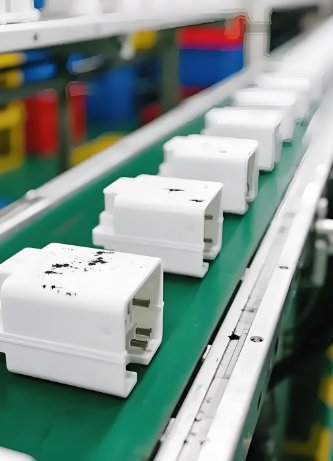
Choosing the right partner for your plastic housing project is a key decision that can impact quality, cost, lead time, and long-term success. For housing injection molding, you usually have two options: work directly with a specialized Mold Maker, or rely on an Original Equipment Manufacturer (OEM) to manage everything—including the tooling.
But how do you decide who is better suited for your needs?
This article compares a Mold Maker and OEM head-to-head across the critical areas of mold design, manufacturing quality, communication, cost, and delivery time. We’ll explain what each partner brings to the table, and which path provides more control and value in your housing injection molding project.
Let’s begin by defining the roles of each.
What Is a Mold Maker?
A Mold Maker is a professional or company that specializes in designing and building the molds used in housing injection molding. This is their core expertise. They typically serve a wide range of industries including electronics, automotive, medical, and consumer products.
Key services from a Mold Maker include:
- CAD mold design
- Mold flow analysis
- Precision tool machining
- Trial molding (T1, T2 samples)
- Mold maintenance and repair
The Mold Maker focuses exclusively on tooling. You or your molder then use that tool to mass-produce housings through housing injection molding.
What Is an OEM?
An Original Equipment Manufacturer (OEM) produces finished products, often offering full-service production—from design to assembly and packaging. Many OEMs outsource their mold production to third-party Mold Makers, though they may manage this process internally.
With OEMs, you don’t always get direct visibility into how or where your mold is built. You place the order for your housings, and they deliver the finished parts.
Comparison: Mold Maker vs. OEM for Housing Projects
1. Tooling Expertise
A Mold Maker lives and breathes tooling. Their shop is equipped with CNC mills, EDM machines, and grinding stations—all focused on perfect mold production. In contrast, OEMs often outsource mold work to these very same shops.
If you want:
- Complex housing geometry
- Tight tolerance fit
- Long mold life
…then a Mold Maker is the better choice for your housing injection molding tooling. They will work closely with your part design to build a high-performance mold with smooth ejection, balanced filling, and optimal cooling.
Winner: Mold Maker
2. Design Control
When you hire a Mold Maker, you own and control the design. You can:
- Approve mold drawings
- Request flow simulations
- Make revisions quickly
OEMs may not offer that level of transparency. They might present a completed tool without involving you in critical decisions. In some cases, they may even retain ownership of the mold.
For full design input and technical control in housing injection molding, partnering with a Mold Maker is a better path.
Winner: Mold Maker
3. Project Cost
Here’s where things get tricky. OEMs offer an all-in-one quote: part cost includes tooling, molding, and assembly. This can seem simpler and even cheaper upfront.
But long term, it may cost more.
OEMs often add a markup on the mold. Worse, you may have to pay again if you want to move production elsewhere. When you work with a Mold Maker, you can price-shop molders and use your mold wherever you like.
Plus, high-quality molds last longer. A well-built tool from a Mold Maker reduces downtime, maintenance, and reject rates in your housing injection molding runs.
Winner: Mold Maker (for long-term savings)
4. Lead Time
OEMs usually require more coordination and approval loops. They may ship mold designs overseas and wait weeks for updates.
A dedicated Mold Maker can often build a prototype or production mold in less time. Especially if you choose one located near your operations or in a time-zone-aligned country like China, Malaysia, or Eastern Europe.
The shorter the tooling lead time, the faster your housing injection molding can begin.
Winner: Mold Maker
5. Communication and Flexibility
Mold design is technical. It requires real-time feedback. Working directly with a Mold Maker ensures fast answers and fewer misunderstandings. You can speak to mold designers, toolmakers, and engineers without delay.
OEMs might filter your requests through project managers or sales reps. This adds friction and delays problem-solving.
In housing injection molding, fast decision-making keeps your schedule on track.
Winner: Mold Maker
6. Part Quality and Process Optimization
OEMs are often more concerned with delivering finished parts quickly than optimizing the mold for long-term use. This may lead to:
- Less durable tooling
- Warped parts
- Unbalanced filling
- Poor cooling efficiency
A Mold Maker ensures the mold is robust, easy to maintain, and optimized for performance. This results in better part consistency across thousands—or millions—of cycles.
For consistent output in housing injection molding, quality starts with tooling. And that means choosing the right Mold Maker.
Winner: Mold Maker
When Might an OEM Be a Better Choice?
Despite all the advantages of working with a Mold Maker, there are some cases where an OEM might be suitable:
- You need very low volumes (under 5,000 pieces)
- Your timeline is extremely tight
- Your housing design is simple and doesn’t require precision
- You don’t want to manage mold logistics
Even in these cases, asking the OEM for full mold documentation, CAD drawings, and ownership rights is smart.
Final Verdict: Who Wins?
For most serious plastic housing projects, especially when part quality and long-term savings matter, the Mold Maker clearly wins.
Criteria | Winner |
---|---|
Tooling Expertise | Mold Maker |
Design Control | Mold Maker |
Project Cost (Long Term) | Mold Maker |
Lead Time | Mold Maker |
Communication | Mold Maker |
Part Quality | Mold Maker |
Simplicity (Low Volume) | OEM (maybe) |
If your project demands excellent housing injection molding, tight tolerances, and future production scalability, then start by partnering with a skilled Mold Maker.
They are your first and most important ally in delivering strong, accurate, and professional plastic housings.