Injection Molding
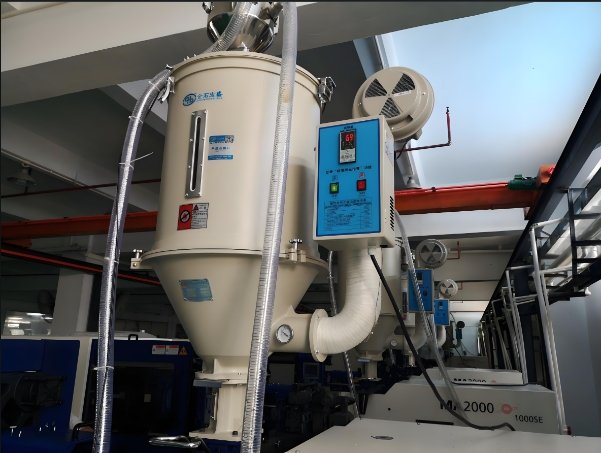
Material Preparation before Injection Molding
Granule Loading:The injection molding process begins with the preparation of the raw material, usually plastic pellets or granules. These materials are chosen based on the desired properties of the final product. Common materials include thermoplastics (like polyethylene, polypropylene, and polycarbonate) and thermosetting plastics. The granules are stored in a hopper positioned above the injection molding machine.
Drying: Some plastics, especially those with high moisture content, require drying before they can be processed. Moisture can lead to defects like bubbles or poor surface finish in the final product. Drying typically involves placing the granules in a drying hopper or oven, where the moisture is removed before processing.
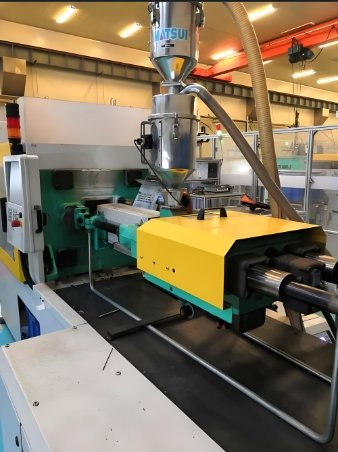
Heating before Injection Molding
Melting the Material: Once the granules are loaded into the hopper, they are gravity-fed into a heated barrel. Inside the barrel, an auger or screw mechanism continuously rotates, pushing the granules forward. The barrel’s heating elements are carefully controlled to melt the plastic granules into a molten state. The temperature is adjusted according to the type of plastic used and is crucial for ensuring that the material reaches the correct viscosity for injection.
Mixing: During the melting process, the plastic is thoroughly mixed by the rotating screw to ensure uniform temperature and consistency. Proper mixing is essential for achieving consistent quality in the molded parts.
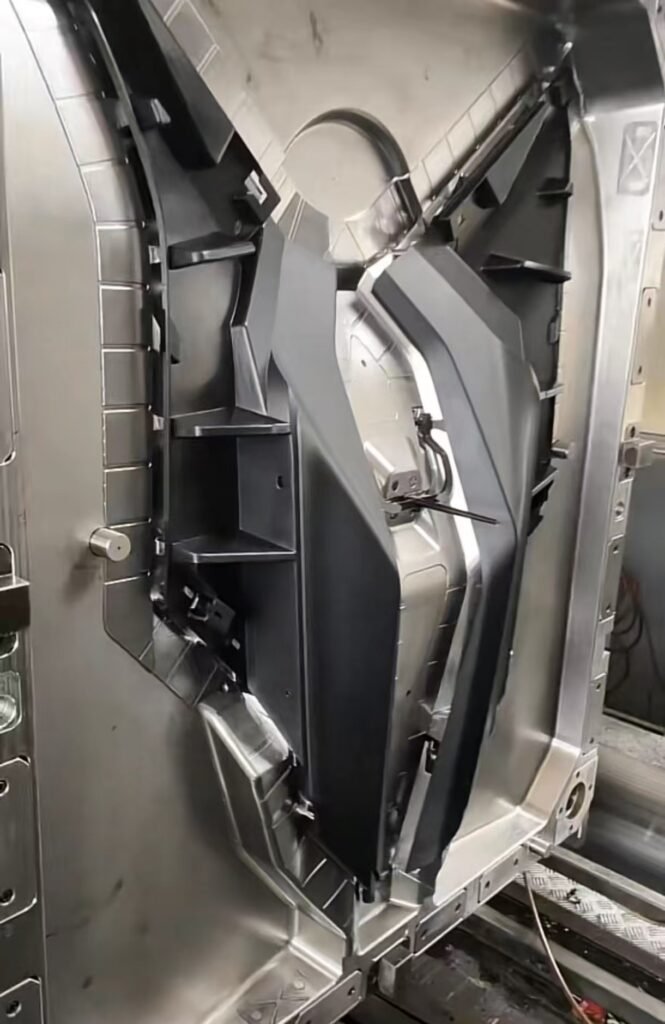
Injection Molding
Injection into the Mold:Once the plastic has reached the desired melt temperature and consistency, it is injected into the mold cavity. The injection is achieved by the machine’s injection unit, which uses hydraulic or electric power to force the molten plastic through a nozzle into the mold. The injection is performed under high pressure to ensure that the plastic completely fills the mold cavity, including any intricate details.
Mold Design Considerations: The mold itself is a complex tool made up of two halves: the core and the cavity. The design of the mold dictates the shape and features of the final product. It typically includes features such as cooling channels, vents, and gating systems. The gating system controls how the molten plastic flows into the cavity, while the cooling channels help regulate the temperature of the mold during the injection process.
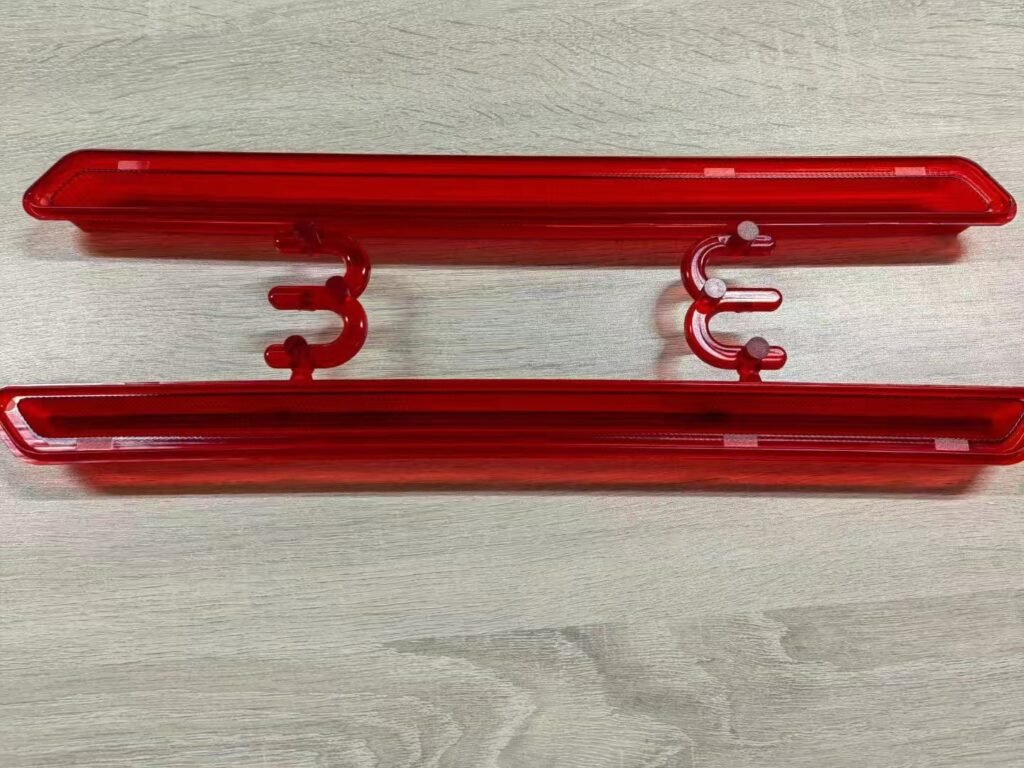

Ejection
Ejection Mechanisms:
Ejector Pins: Mechanical pins that push the part out of the mold cavity.
Air Blasts: Compressed air used to force the part out of the mold.
Hydraulic Ejectors: Used for more complex or high-volume parts.
Part Removal:
The part is carefully ejected from the mold to avoid damage. If the part has complex geometries or undercuts, additional mechanisms such as lifters or cams might be used to assist in its removal.
Inspection and Finishing
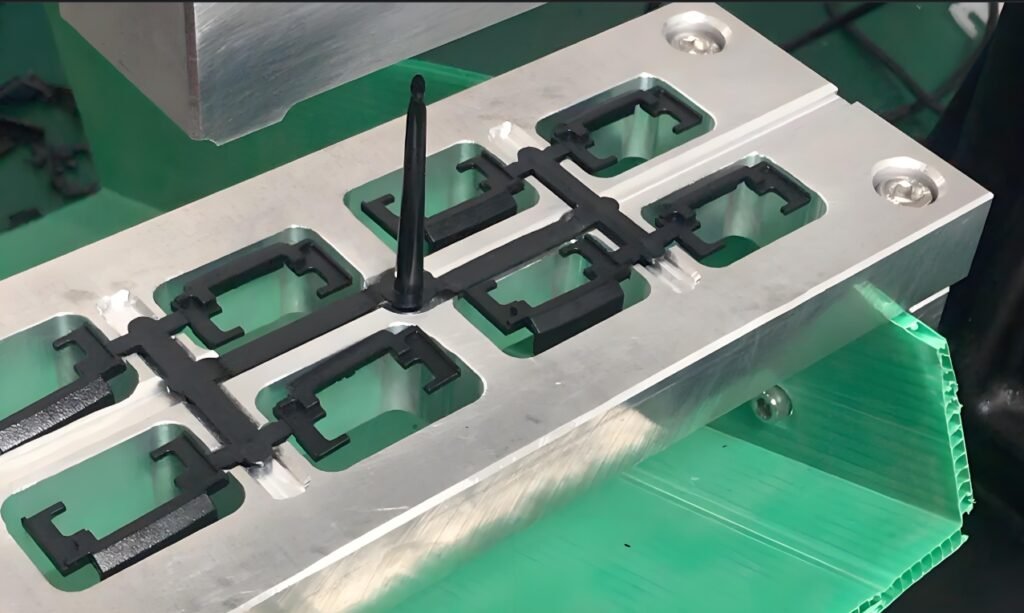
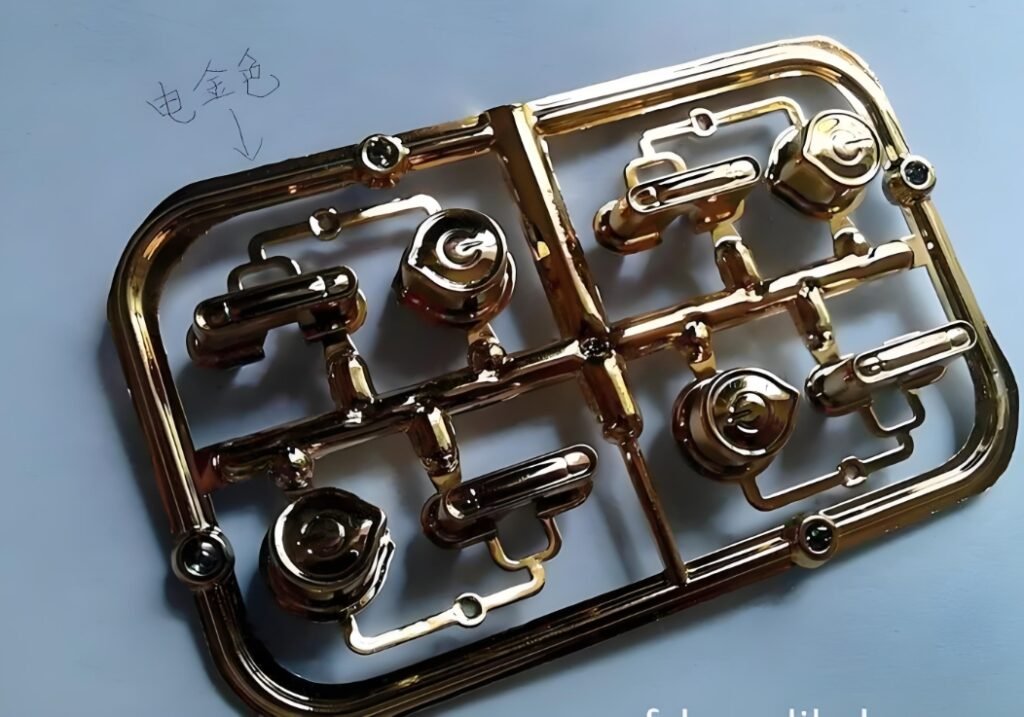
Inspection: After ejection, the molded part undergoes inspection to ensure it meets the required specifications. This inspection can be visual or involve precise measurements. Common issues to check for include dimensional accuracy, surface defects, and overall quality.
Trimming: Removing any excess material, such as flash or sprue, from the part.
Deburring: Smoothing out any sharp edges or burrs.
Painting or Coating: Applying any surface finishes or coatings required for the final product.
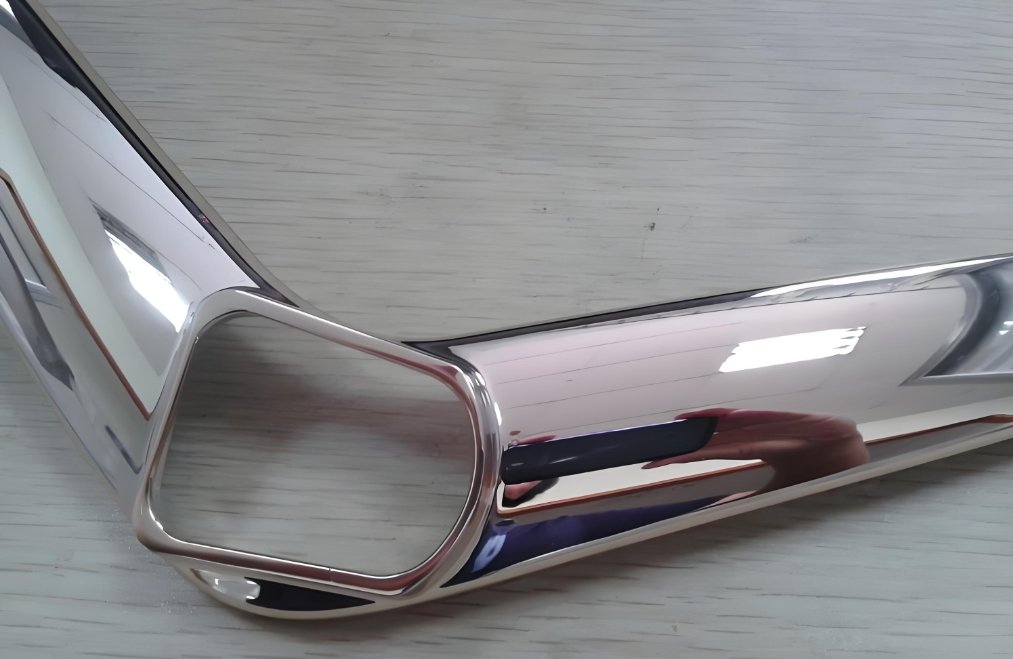
Cycle Repetition
Repeat Process: After ejection, the molded part undergoes inspection to ensure it meets the required specifications. This inspection can be visual or involve precise measurements. Common issues to check for include dimensional accuracy, surface defects, and overall quality.
Cycle Time: The cycle time is the duration it takes to complete one full cycle of injection, cooling, and ejection. This time can vary based on the part’s complexity, material used, and the efficiency of the mold. Reducing cycle time is often a goal in optimizing the injection molding process to increase production efficiency.
Mold Maintenance
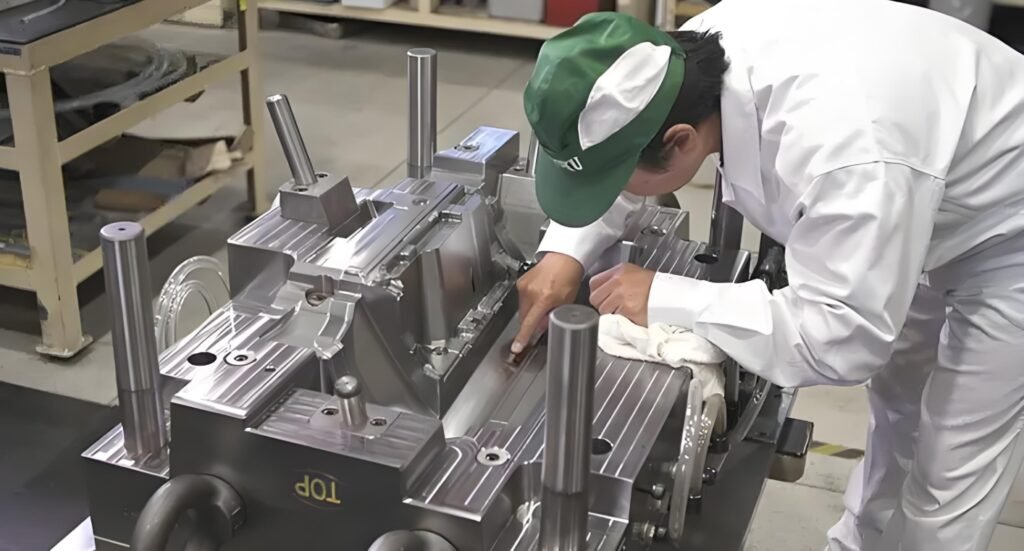
Routine Maintenance: To ensure the longevity and consistent performance of the mold, routine maintenance is required. This includes regular cleaning, lubrication of moving parts, and inspection for wear and tear.
Cycle Time: The cycle time is the duration it takes to complete one full cycle of injection, cooling, and ejection. This time can vary based on the part’s complexity, material used, and the efficiency of the mold. Reducing cycle time is often a goal in optimizing the injection molding process to increase production efficiency.
Production Scaling
High-Volume Production: Once the mold and process are optimized, the system is scaled up for high-volume production. The efficiency of the mold and the stability of the process are critical for maintaining consistency and reducing costs in large-scale manufacturing.
Efficiency Improvements: Continuous monitoring and optimization are often applied to improve efficiency, reduce defects, and increase production rates. This can involve tweaking machine settings, modifying the mold, or improving material handling processes.
This comprehensive overview covers the major steps involved in the injection molding process, from material preparation through to production scaling. Each step is crucial for ensuring the production of high-quality, consistent parts and optimizing the manufacturing process.