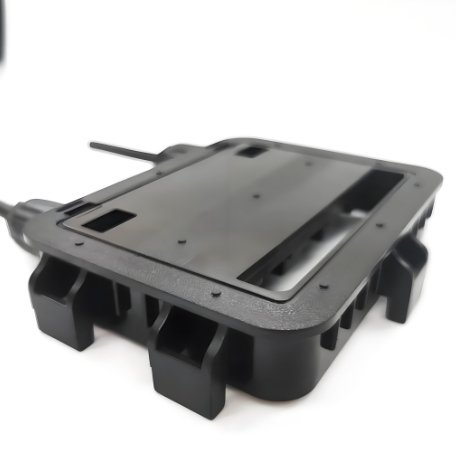
Nylon is one of the most reliable and widely used engineering plastics in the injection molding industry. Known for its excellent mechanical strength, wear resistance, and chemical stability, nylon is ideal for applications that demand durability and toughness. Choosing the right Injection Molding Company with a skilled Mold Maker is crucial to achieving optimal tensile strength in your nylon parts.
In this article, we explore how the expertise of a specialized Injection Molding Company and a professional Mold Maker directly contributes to producing high-tensile nylon components for critical applications.
Why Nylon is a Popular Choice in Injection Molding
Nylon (polyamide) offers several performance advantages:
- High tensile strength
- Excellent wear and abrasion resistance
- Good thermal stability
- Low coefficient of friction
- Resistant to fuels, oils, and many chemicals
- Natural lubricity for moving parts
Because of these traits, nylon is frequently used in automotive, industrial, consumer electronics, and structural parts. However, molding nylon successfully requires deep knowledge and precision, both from the Injection Molding Company and the Mold Maker involved in the process.
The Role of the Injection Molding Company
An experienced Injection Molding Company handles nylon with attention to detail. Nylon’s hygroscopic nature means it absorbs moisture easily. If not dried properly before molding, the part may suffer from porosity and reduced strength.
Key considerations handled by a capable Injection Molding Company include:
1. Proper Material Preparation
Nylon must be thoroughly dried. A quality Injection Molding Company uses desiccant dryers and monitors moisture levels closely.
2. Precise Temperature Control
Barrel temperatures usually range between 230–290°C for nylon. The company ensures stable temperature zones to avoid degradation and to promote strong molecular bonding.
3. Optimized Injection Speed and Pressure
Nylon flows easily when molten but can flash if injected too quickly. The Injection Molding Company uses balanced injection speeds and pressures to achieve a clean fill with high density.
4. Efficient Cooling Cycles
Controlled cooling prevents warping and stress concentration. This directly affects the part’s tensile performance.
5. Post-Molding Conditioning
Some nylon parts may require annealing or controlled humidity exposure to stabilize strength and flexibility.
The Critical Role of the Mold Maker
A professional Mold Maker plays a foundational role in producing high-strength nylon parts. The mold must support proper flow, cooling, and ejection to maintain the structural integrity of the material.
1. Mold Steel Selection
The Mold Maker chooses high-hardness tool steel with strong wear resistance to withstand nylon’s abrasiveness.
2. Vent Design
Nylon can trap gas during molding. Precise venting by the Mold Maker prevents short shots and burn marks.
3. Balanced Flow Paths
The gate and runner system must ensure even fill to avoid stress risers. Proper design leads to consistent tensile performance.
4. Core and Cavity Precision
Tolerances are tightly maintained by the Mold Maker. Accurate alignment ensures that walls, ribs, and bosses mold exactly to design.
5. Surface Finish
Mold texture affects part aesthetics and function. For moving parts, the Mold Maker may add a polished finish to reduce friction.
Applications of Nylon Injection Molding
A specialized Injection Molding Company working with nylon serves many industries. Common applications include:
- Automotive Components – gears, bushings, cable ties, housings
- Industrial Machinery – sprockets, pulleys, structural brackets
- Electrical – circuit board holders, connectors, insulating parts
- Consumer Products – sports gear, handles, zippers
- Medical Devices – clips, housings, and limited-use instruments
In all these areas, the high tensile strength of nylon improves safety, reliability, and product lifespan.
Measuring Tensile Performance in Nylon Parts
Tensile strength is the material’s resistance to pulling forces. It’s measured in megapascals (MPa). Nylon 6, for example, typically has tensile strength between 45–90 MPa. With glass-filled nylon, it can reach 150 MPa or more.
A reputable Injection Molding Company works with design engineers to optimize wall thickness, rib placement, and gate location to maximize strength. The Mold Maker ensures mold geometry supports uniform flow and stress distribution.
What Makes a Great Nylon Injection Molding Company?
When selecting a partner for nylon parts, look for the following:
1. Material Expertise
The best Injection Molding Company offers guidance on nylon grades—Nylon 6, Nylon 6/6, glass-filled options, and more.
2. Tooling Excellence
Having an in-house Mold Maker means faster modifications, better tooling accuracy, and shorter lead times.
3. Advanced Machinery
Modern injection machines with multi-zone control and closed-loop feedback help optimize every shot.
4. Quality Assurance
The company should offer tensile testing, dimensional verification, and part certification.
5. Design Support
Skilled engineers at the Injection Molding Company and the Mold Maker help improve product design for strength, cost, and manufacturability.
Nylon Molding Challenges and Solutions
Nylon is tough but tricky. Here are some common problems and how experienced teams solve them:
Problem | Solution |
---|---|
Moisture absorption | Proper drying and sealed storage |
Flashing at parting lines | Optimized clamp force and mold alignment |
Warp or sink marks | Even wall thickness and proper cooling design |
Brittleness | Proper conditioning and controlled molding environment |
Surface defects | Polish mold surface and adjust fill speed |
The combined expertise of a seasoned Injection Molding Company and a precision Mold Maker prevents these issues before they occur.
Conclusion
Producing strong, reliable nylon components starts with choosing the right Injection Molding Company and a skilled Mold Maker. Nylon offers unmatched tensile performance when handled correctly, but success depends on drying, tooling, machine control, and post-processing.
A trustworthy Injection Molding Company will understand how to handle nylon’s behavior under heat, pressure, and humidity. The Mold Maker will create molds that maintain consistency, strength, and efficiency.
If your project demands parts that can withstand high loads, mechanical stress, and tough environments, nylon injection molding is your solution. And with the right Injection Molding Company and Mold Maker by your side, you can be confident in both performance and reliability.