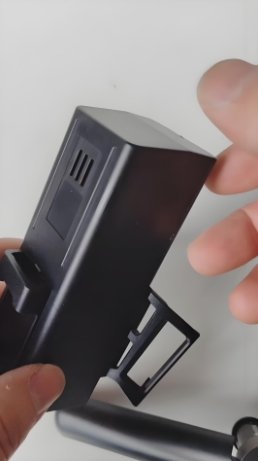
Polyethylene Terephthalate, or PET, is widely used for creating clear plastic parts due to its excellent transparency, strength, and barrier properties. But not all manufacturers can mold PET effectively. You need a specialized Injection Molding Company and an expert Mold Maker to achieve clarity and precision without defects.
This article explores the best practices, challenges, and benefits of working with a PET-focused Injection Molding Company, and why a professional Mold Maker plays a critical role in the success of your project.
Why PET Is Ideal for Clear Plastic Parts
PET is a thermoplastic polymer known for its excellent light transmission and high gloss. It’s widely used in:
- Beverage bottles
- Cosmetic containers
- Medical packaging
- Clear electronic housings
- Transparent machine guards
PET provides durability, resistance to moisture and chemicals, and excellent clarity—qualities you need for premium, consumer-facing products.
Why You Need a Specialized Injection Molding Company
PET is not as easy to mold as other resins. It has a narrow processing window and is sensitive to moisture and heat history. A capable Injection Molding Company knows how to handle PET properly and avoid defects like haze, bubbles, and yellowing.
Here’s what makes a professional Injection Molding Company essential:
1. Moisture Control
PET absorbs moisture quickly. If not dried properly, it degrades during molding, causing loss of clarity and poor mechanical strength. A reliable Injection Molding Company uses advanced dehumidifying dryers and drying ovens to ensure low moisture content.
2. Precise Temperature Management
PET requires precise temperature control during melting and molding. Overheating can cause degradation, while underheating may result in poor flow. A skilled Injection Molding Company maintains perfect thermal balance throughout the cycle.
3. Tooling Built by a Skilled Mold Maker
The role of the Mold Maker is vital. PET requires mirror-polished cavities and vented molds. The Mold Maker must understand the shrinkage characteristics of PET and apply advanced surface treatments to prevent sticking and burn marks.
The Role of the Mold Maker in PET Injection Molding
A Mold Maker plays a central role in ensuring PET parts come out clear, accurate, and defect-free. For PET molding, tooling precision must be exceptionally high.
Key Contributions from a Professional Mold Maker:
- Polished mold surfaces to prevent flow marks or dull areas.
- Highly vented mold designs to allow gases to escape during injection.
- Waterline design to manage consistent mold temperatures and avoid haze.
- Material choice for mold steels that resist corrosion from PET’s acidic degradation byproducts.
Choosing a Mold Maker experienced in PET molding means fewer revisions, longer tool life, and better part clarity.
Common Applications of PET Injection Molding
Working with a trusted Injection Molding Company lets you unlock the full potential of PET. Clear plastic parts made from PET are used in:
- Food and beverage packaging: Bottles, jars, and dispensers.
- Medical containers: Transparent blister trays and diagnostic vials.
- Consumer electronics: Covers for indicators, sensors, and displays.
- Beauty products: Compact cases, lipstick tubes, and cream jars.
- Retail products: Clamshell packaging and display cases.
PET performs reliably when molded correctly, providing both functionality and a polished appearance.
Common Challenges in PET Injection Molding (and How the Right Company Solves Them)
Challenge | How a Skilled Injection Molding Company Solves It |
---|---|
Yellowing or haziness | Ensures proper drying and temperature control |
Bubbles or voids | Uses gas venting and correct shot size |
Part sticking | Applies mold release and mirror-polished cavities |
Sink marks | Controls cooling rates and gate size |
Inconsistent dimensions | Employs experienced Mold Maker for mold design and alignment |
These challenges show that PET is not beginner-friendly. Only an experienced Injection Molding Company with a reliable Mold Maker can maintain part clarity and dimensional precision consistently.
Design Tips for Clear PET Parts
Your part design affects whether the molded result is crystal-clear or cloudy. A knowledgeable Injection Molding Company and Mold Maker will guide you on the following:
- Uniform wall thickness to avoid flow hesitations and stress lines.
- No sharp corners—use smooth transitions to maintain optical clarity.
- Large radii and gentle curves to prevent turbulence in resin flow.
- Proper gate placement to control how the material fills the cavity.
By involving a Mold Maker early in the design phase, your tooling will be optimized for PET’s unique flow behavior and shrinkage.
Benefits of Choosing the Right Injection Molding Company for PET
1. Superior Clarity
Get crystal-clear parts with no haze, fog, or bubbles.
2. Fast Cycle Times
Advanced equipment and cooling systems reduce production time.
3. Consistent Part Quality
From the first shot to the thousandth, dimensions remain stable.
4. In-House Mold Making
A full-service Injection Molding Company with its own Mold Maker can offer better pricing, quicker lead times, and better support.
5. Compliance with Safety Standards
Especially for food and medical applications, the company ensures FDA or ISO-compliant production.
Choosing the Best PET Injection Molding Company
When searching for a PET Injection Molding Company, look for these traits:
- Experience with clear resins like PETG, PET, and PC
- Full in-house mold making capabilities
- Transparent quality inspection systems
- Strong portfolio in food, medical, and consumer industries
- Responsive engineering and design support
A trusted Injection Molding Company and Mold Maker partnership ensures you don’t waste time or money on avoidable defects.
Conclusion
PET is one of the most widely used clear plastics in the world. But molding it correctly requires more than just a basic machine. You need a dedicated Injection Molding Company with experience, equipment, and attention to detail. You also need a precision-driven Mold Maker who knows how to polish, vent, and machine a tool specifically for PET.
When you combine these two forces—molding expertise and mold-making precision—you get clear, strong, beautiful plastic parts ready for the market.