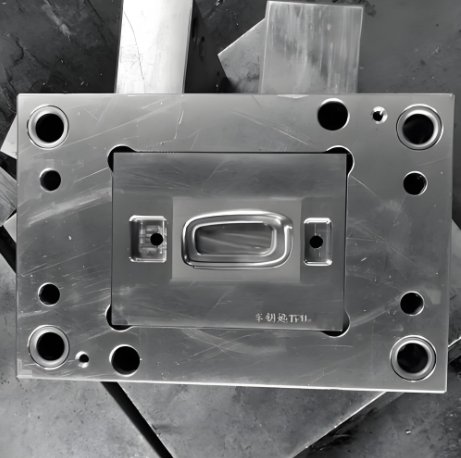
Plastic control boxes are found in nearly every industry—from home electronics to factory automation. These housings protect electronic components, organize wiring, and keep systems safe. The most effective and efficient way to produce them is through Housing Injection Molding. When this method is used by a skilled Mold Maker, the result is a strong, precise, and long-lasting housing solution.
In this article, we’ll explore how Housing Injection Molding works for control boxes, the benefits it offers, and the critical role of the Mold Maker.
What Is Housing Injection Molding?
Housing Injection Molding is a process that forms plastic parts by injecting molten material into a metal mold. It’s ideal for high-volume production of complex parts—like plastic control box housings—that must meet tight tolerances and design requirements.
The basic steps include:
- Plastic pellets are melted inside a heated barrel.
- The molten plastic is injected into a precision-made mold.
- The plastic fills the cavity, taking on the mold’s shape.
- It cools and hardens.
- The mold opens, and the finished part is ejected.
This method is highly efficient and creates repeatable results for thousands or even millions of parts.
Why Control Boxes Use Housing Injection Molding
Plastic control boxes must be strong, lightweight, and resistant to moisture or chemicals. They also need to look professional, with a clean surface and sometimes logos or openings for switches.
Housing Injection Molding delivers all these benefits:
- Accuracy: It creates detailed designs, perfect for cable slots, button holes, and hinges.
- Strength: Plastic types like ABS and polycarbonate offer excellent durability.
- Cost-Efficiency: Once the mold is made, the cost per part drops significantly.
- Custom Options: Colors, textures, and transparency levels can be added easily.
Because control boxes often require different shapes and sizes, the flexibility of Housing Injection Molding is a major advantage.
The Importance of the Mold Maker
Every injection-molded part starts with a mold—and that mold must be perfect. That’s where the Mold Maker comes in. A skilled Mold Maker understands how to design and build molds that work smoothly in high-speed production.
To make a mold for a plastic control box, the Mold Maker must:
- Design the cavity to match the part’s exact dimensions
- Choose the right steel grade for long mold life
- Add cooling channels to control temperature during molding
- Include gates and vents to guide the plastic and remove air
- Polish surfaces or add texture depending on the final look
A good mold reduces part defects, lowers scrap rates, and ensures long-term production stability.
Best Plastic Materials for Control Boxes
Choosing the right plastic for control box housings is critical. The choice depends on what the box will face: heat, impact, chemicals, or UV light.
Some popular options in Housing Injection Molding include:
- ABS (Acrylonitrile Butadiene Styrene): Strong, easy to mold, and cost-effective.
- Polycarbonate (PC): Transparent, very tough, and heat-resistant.
- PVC (Polyvinyl Chloride): Good for chemical resistance and electrical insulation.
- Polypropylene (PP): Lightweight and moisture-resistant.
The Mold Maker adjusts the mold design based on which plastic is used, since each one flows and shrinks differently.
Applications of Injection-Molded Control Box Housings
Control boxes made using Housing Injection Molding appear in many sectors:
- Electronics: Enclosures for circuit boards, battery holders, and connectors.
- Automation: Housing for control systems in machines and robots.
- Automotive: Fuse boxes, sensor enclosures, and power modules.
- Consumer Products: Remote controls, gaming systems, and charging docks.
- Medical Devices: Control panels and electronic monitoring systems.
In each case, the housing must protect internal parts while offering a professional and reliable appearance.
Design Tips for Molded Control Boxes
To make sure the design works well with Housing Injection Molding, engineers follow a few basic rules:
- Uniform Wall Thickness: Prevents warping and uneven cooling.
- Rounded Corners: Easier to mold and more resistant to cracking.
- Draft Angles: Help the part release easily from the mold.
- Ribbing: Adds strength without using extra material.
These features allow the Mold Maker to create a mold that functions smoothly and lasts longer in production.
Production Volume and Cost Benefits
One big advantage of Housing Injection Molding is scalability. After the mold is made, the same part can be produced at very low cost. That makes this process perfect for both medium and high-volume runs.
A well-built mold by a professional Mold Maker can last for hundreds of thousands of shots. Even complex parts become affordable when spread over large production runs.
Automation can also be added to further reduce labor costs and increase speed.
Quality Control in the Injection Molding Process
Plastic control box housings need to meet exact standards. Here’s how quality is kept high:
- Visual Inspections: Check for defects like sink marks or flash.
- Dimensional Checks: Use calipers and CMM machines to measure parts.
- Fit Testing: Make sure covers snap shut or screw in place perfectly.
- Material Tests: Confirm plastic strength and chemical resistance.
The Mold Maker and injection team work together to fix any problems quickly.
Future Trends in Control Box Housing Design
The future of Housing Injection Molding includes smart materials and advanced mold technology. Expect more:
- Recycled plastics to meet green goals
- Two-shot molding for combining materials
- Laser etching for custom branding
- Smart molds with sensors to monitor pressure and heat
The role of the Mold Maker is becoming more advanced too, with 3D printing and AI-assisted design helping build better molds faster.
Plastic control box housings are essential to modern electronics and industrial systems. With Housing Injection Molding, manufacturers can make durable, high-quality enclosures quickly and at scale. But this is only possible with the help of an expert Mold Maker who creates the precise mold behind each perfect part.
Whether you’re producing enclosures for industrial machines or consumer electronics, this process offers strength, flexibility, and cost savings. When done right, Housing Injection Molding delivers both protection and polish to every device it supports.
Do you want a technical diagram showing a control box injection mold? I can provide one for visual clarity.