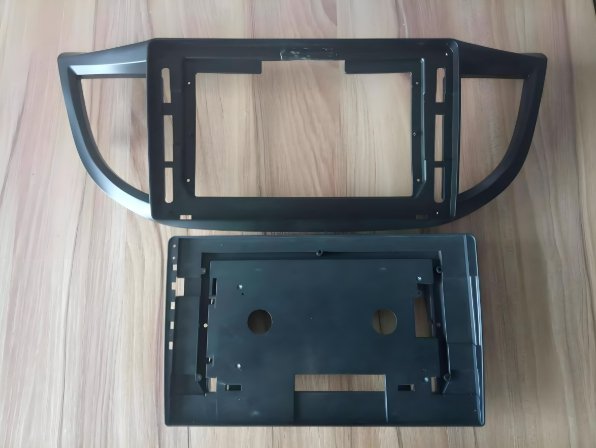
Electronic devices require high-precision parts. Electronic injection molding ensures accuracy in producing these components. Mold makers use advanced techniques to create durable, high-performance parts. This article explores the future of electronic injection molding and its impact on manufacturing.
1. What Is Electronic Injection Molding?
1.1 The Basics of Injection Molding
Injection molding is a process that shapes plastic by injecting molten material into a mold.
1.2 How It Applies to Electronics
Electronic injection molding produces casings, connectors, and circuit board components.
1.3 Importance of Precision
Even the smallest defects can affect electronic performance.
2. Key Advantages of Electronic Injection Molding
2.1 High Precision and Consistency
Molded parts maintain exact dimensions across large production runs.
2.2 Cost-Effective Production
Mass production reduces per-unit costs.
2.3 Lightweight and Durable Components
Advanced plastics offer strength while keeping devices lightweight.
2.4 Complex Geometries
Intricate designs are possible with modern molding techniques.
3. The Role of Mold Makers in Electronic Injection Molding
3.1 Designing High-Precision Molds
Mold makers create detailed molds for complex electronic parts.
3.2 Material Selection
They choose plastics that provide durability, heat resistance, and electrical insulation.
3.3 Ensuring Tight Tolerances
Accurate molds reduce defects in electronic components.
4. Advanced Materials for Electronic Injection Molding
4.1 High-Performance Plastics
Materials like PEEK and LCP withstand high temperatures and electrical loads.
4.2 Conductive Polymers
Some plastics allow electricity to pass, making them ideal for sensors.
4.3 Flame-Retardant Materials
These plastics prevent fire hazards in electronic devices.
5. Innovations in Electronic Injection Molding
5.1 Micro Injection Molding
Tiny parts for wearables and medical devices require micro-molding.
5.2 Overmolding
Combining different materials in one part improves performance.
5.3 Insert Molding
Plastic is molded around metal components for stronger electronic parts.
6. Applications of Electronic Injection Molding
6.1 Consumer Electronics
Smartphones, laptops, and tablets require molded casings and connectors.
6.2 Automotive Electronics
Injection molding produces durable components for car electronics.
6.3 Medical Devices
Wearable monitors and diagnostic tools use molded plastic parts.
6.4 Telecommunications
Connectors and cable housings ensure reliable communication systems.
7. Challenges in Electronic Injection Molding
7.1 Tight Industry Regulations
Electronic components must meet strict safety and performance standards.
7.2 Miniaturization of Components
Smaller devices require extreme precision in molding.
7.3 Material Limitations
Not all plastics can handle heat and electrical currents effectively.
8. Automation in Electronic Injection Molding
8.1 AI-Driven Quality Control
Machine learning detects defects before parts leave production.
8.2 Robotic Mold Handling
Automated systems improve efficiency and consistency.
8.3 Smart Factories
Connected machines optimize the molding process for better performance.
9. The Future of Electronic Injection Molding
9.1 Sustainable Materials
Recyclable and biodegradable plastics will reduce environmental impact.
9.2 3D-Printed Molds
Faster prototyping will improve design testing.
9.3 Integration with Industry 4.0
Data-driven manufacturing will enhance quality control.
Electronic injection molding is shaping the future of manufacturing. Mold makers play a crucial role in creating precise, high-performance components. As technology advances, injection molding will become even more efficient and sustainable. The future of electronics depends on innovation in precision molding.