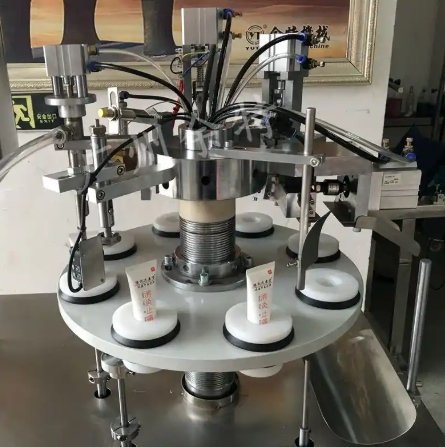
Automotive parts need accuracy. Automotive injection molds ensure precision. A skilled mold maker guarantees quality. Efficient molds reduce defects. Advanced designs improve performance.
Why Precision Matters in Automotive Manufacturing
1. High Standards for Auto Parts
Cars require reliable parts. Automotive injection molds ensure exact dimensions. A mold maker prevents errors.
2. Consistency in Large-Scale Production
Mass production demands accuracy. Automotive injection molds create identical parts. A mold maker maintains uniformity.
3. Cost-Effective Manufacturing
Precision reduces waste. Automotive injection molds optimize material use. A mold maker lowers costs.
4. Enhanced Vehicle Performance
Perfectly molded parts fit well. Automotive injection molds improve safety. A mold maker ensures proper design.
Key Components of Automotive Injection Molds
1. Mold Base
The base supports the mold. Automotive injection molds need a strong foundation. A mold maker selects durable metals.
2. Cavity and Core
These shape the part. Automotive injection molds must have accurate dimensions. A mold maker ensures precision.
3. Ejector System
This removes molded parts. Automotive injection molds need smooth ejection. A mold maker prevents sticking.
4. Cooling System
Fast cooling improves production. Automotive injection molds require efficient cooling. A mold maker designs proper channels.
Materials for Automotive Injection Molds
1. High-Strength Steel
Steel offers durability. Automotive injection molds use hardened steel. A mold maker extends mold life.
2. Aluminum for Prototyping
Aluminum is lightweight. Automotive injection molds use it for testing. A mold maker speeds up development.
3. Advanced Polymers
Polymers reduce wear. Automotive injection molds benefit from inserts. A mold maker enhances performance.
4. Surface Coatings
Coatings prevent corrosion. Automotive injection molds last longer with protection. A mold maker reduces maintenance.
Advanced Design Techniques in Injection Molding
1. CAD Modeling for Accuracy
CAD ensures precise design. Automotive injection molds rely on digital models. A mold maker eliminates errors.
2. Mold Flow Analysis
This tool predicts defects. Automotive injection molds improve through simulation. A mold maker enhances quality.
3. Multi-Cavity Molds
More cavities increase output. Automotive injection molds reduce cycle times. A mold maker boosts efficiency.
4. Conformal Cooling Design
Cooling speeds up production. Automotive injection molds use custom channels. A mold maker optimizes cooling.
Manufacturing Process of Automotive Injection Molds
1. Design Phase
Precision starts here. Automotive injection molds require detailed planning. A mold maker ensures accuracy.
2. CNC Machining
CNC cuts metal precisely. Automotive injection molds need high precision. A mold maker controls every step.
3. Heat Treatment
Hardening improves durability. Automotive injection molds last longer with treatment. A mold maker enhances strength.
4. Polishing and Assembly
Final touches matter. Automotive injection molds must be smooth. A mold maker ensures defect-free molds.
Applications of Automotive Injection Molds
1. Interior Components
Dashboards, panels, and trims. Automotive injection molds create precise parts. A mold maker ensures high detail.
2. Exterior Parts
Bumpers, grilles, and fenders. Automotive injection molds shape durable exteriors. A mold maker ensures strength.
3. Engine and Under-the-Hood Parts
Covers, housings, and reservoirs. Automotive injection molds improve engine efficiency. A mold maker guarantees quality.
4. Lighting Components
Headlights and taillights need precision. Automotive injection molds ensure perfect clarity. A mold maker enhances visibility.
Challenges in Automotive Injection Molding
1. High Precision Demands
Cars require exact parts. Automotive injection molds must have no defects. A mold maker maintains tight tolerances.
2. Complex Designs
Auto parts have intricate shapes. Automotive injection molds need advanced techniques. A mold maker ensures precision.
3. Material Selection
Different parts need different plastics. Automotive injection molds use various materials. A mold maker chooses the best option.
4. Rapid Production Needs
Automakers need fast output. Automotive injection molds must work efficiently. A mold maker optimizes production.
Future Trends in Automotive Injection Molding
1. Lightweight Materials
Cars need fuel efficiency. Automotive injection molds use lightweight plastics. A mold maker reduces weight.
2. Smart Mold Technology
Sensors track performance. Automotive injection molds improve with data. A mold maker enhances efficiency.
3. Sustainable Molding
Eco-friendly materials grow. Automotive injection molds use recycled plastics. A mold maker supports sustainability.
4. Automation in Mold Making
Robots improve speed. Automotive injection molds benefit from AI. A mold maker adapts to technology.
Precision is vital. Automotive injection molds shape reliable parts. A skilled mold maker ensures accuracy. Advanced designs improve efficiency. The future of automotive injection molds continues evolving.