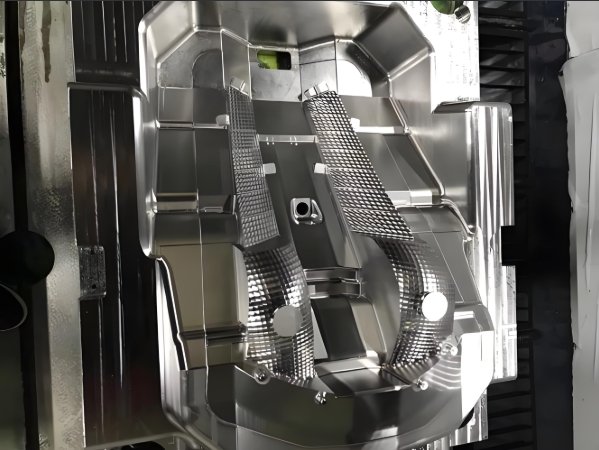
Engines are the heart of vehicles. Many parts come from precision plastic. Automotive Injection Molds make these parts possible. Skilled Mold Makers design and build these molds. They ensure accuracy and efficiency. This article explores the importance of molds in engine production.
Why Use Automotive Injection Molds for Engine Parts?
1. Precision Manufacturing
Injection molds produce exact shapes. This ensures perfect fit and function.
2. Lightweight Components
Plastic engine parts reduce weight. This improves fuel efficiency.
3. Cost-Effective Production
Molds allow high-volume manufacturing. This lowers costs over time.
4. Durability
Injection-molded parts last longer. They resist heat and wear.
Key Roles of a Mold Maker
1. Custom Design
Every engine part has unique needs. A Mold Maker designs molds to match these specifications.
2. Material Expertise
Choosing the right materials is crucial. A Mold Maker selects materials for strength and durability.
3. High Standards
Quality is essential. Skilled Mold Makers ensure precise molds for reliable parts.
4. Problem Solving
They address design challenges effectively. This improves production outcomes.
Engine Components Made with Injection Molds
1. Valve Covers
Plastic valve covers are lightweight and durable. Injection molds ensure their perfect shape.
2. Oil Pans
Molded oil pans are leak-resistant. They also reduce engine weight.
3. Air Intake Manifolds
These parts control airflow into the engine. Molds ensure smooth and accurate designs.
4. Engine Mounts
Molded mounts absorb vibrations. They provide strength and flexibility.
Materials for Automotive Injection Molds
1. Nylon
Nylon is strong and heat-resistant. It works well for engine parts.
2. Polypropylene
This lightweight material is durable. It reduces the weight of engine components.
3. ABS Plastic
ABS is impact-resistant. It provides strength and reliability.
4. Polycarbonate
This material offers high strength. It withstands extreme conditions.
The Injection Molding Process
1. Mold Design
The process starts with detailed designs. Mold Makers create precise plans.
2. Material Selection
Plastics are chosen based on part requirements.
3. Injection Phase
Molten plastic is injected into the mold.
4. Cooling and Solidifying
The plastic cools inside the mold. This gives it the desired shape.
5. Trimming and Finishing
Excess material is removed. The final product is ready.
Advantages of Injection Molding for Engine Components
1. Exact Specifications
Injection molding ensures high accuracy. Parts fit perfectly into engine systems.
2. High Strength
Molded parts resist stress and wear.
3. Lightweight Design
Plastic parts reduce engine weight.
4. Cost Efficiency
Mass production reduces overall costs.
Challenges in Making Engine Molds
1. Complex Designs
Engine components are intricate. Molds must meet these complex designs.
2. Material Constraints
Not all plastics suit high temperatures. Careful selection is critical.
3. Maintenance Needs
Molds require regular upkeep. This prevents defects in parts.
Advances in Injection Molding
1. 3D Printing for Prototypes
3D printing speeds up mold development.
2. Automation
Robotic systems enhance accuracy and efficiency.
3. Sustainable Practices
Recycled materials reduce environmental impact.
Applications Beyond Engine Components
1. Exterior Parts
Injection molds create bumpers and grilles.
2. Interior Components
Dashboards and panels come from precision molds.
3. Lighting Systems
Headlight and taillight housings use injection molding.
4. Fuel System Parts
Fuel tanks and filters are molded with precision.
Sustainability in Engine Molding
1. Eco-Friendly Plastics
Bio-based materials are becoming popular.
2. Energy Efficiency
Modern machines consume less energy.
3. Waste Reduction
Injection molding produces minimal waste.
Future Trends in Automotive Injection Molds
1. Smart Manufacturing
Molds will integrate real-time data.
2. Advanced Materials
New materials will improve part performance.
3. Faster Production
Technology will further reduce production time.
Precision is key in engine manufacturing. Automotive Injection Molds provide this precision. Skilled Mold Makers ensure molds meet high standards. They deliver durability and efficiency. As technology advances, injection molds will remain essential. For precise, cost-effective engine parts, these molds are irreplaceable.