Packaging
Injection Molding in the Packaging Industry, A Mold Maker Will Build It for You
Injection molding is crucial in the packaging industry. It provides an efficient method for producing various packaging components. A skilled mold maker plays a key role in this process. Their expertise ensures molds meet high standards.
Caps and Closures Tips From the Mold Maker
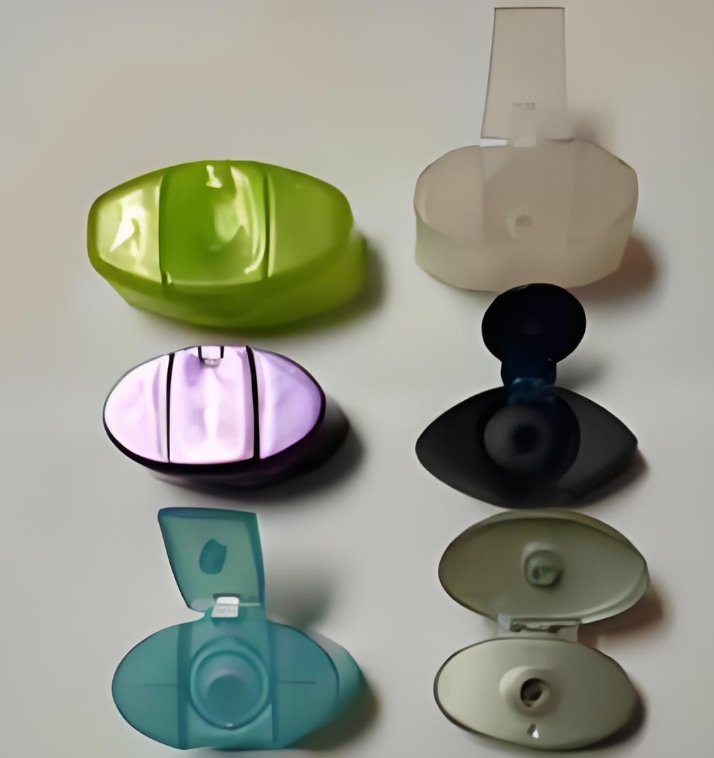
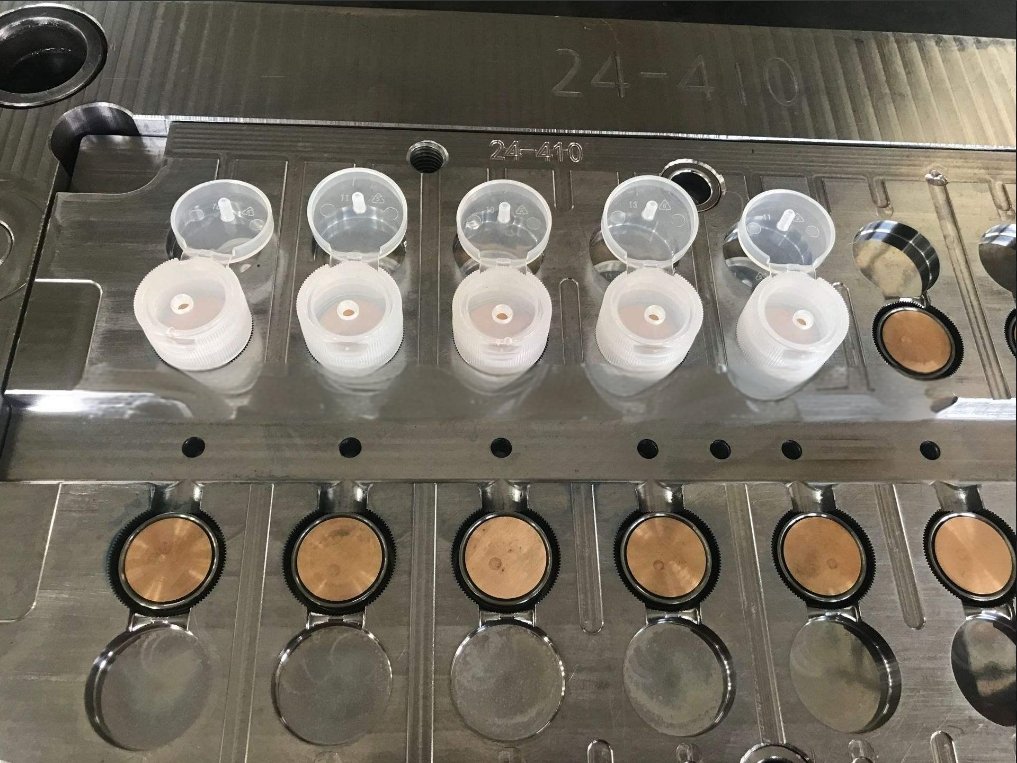
Examples: Bottle caps, flip-tops, snap-on lids, and dispensing closures.
Injection molding achieves uniform wall thickness and smooth finishes. Mold maker ensure that these components are both functional and aesthetically pleasing.
Containers and Tubs Insights From the Mold Maker
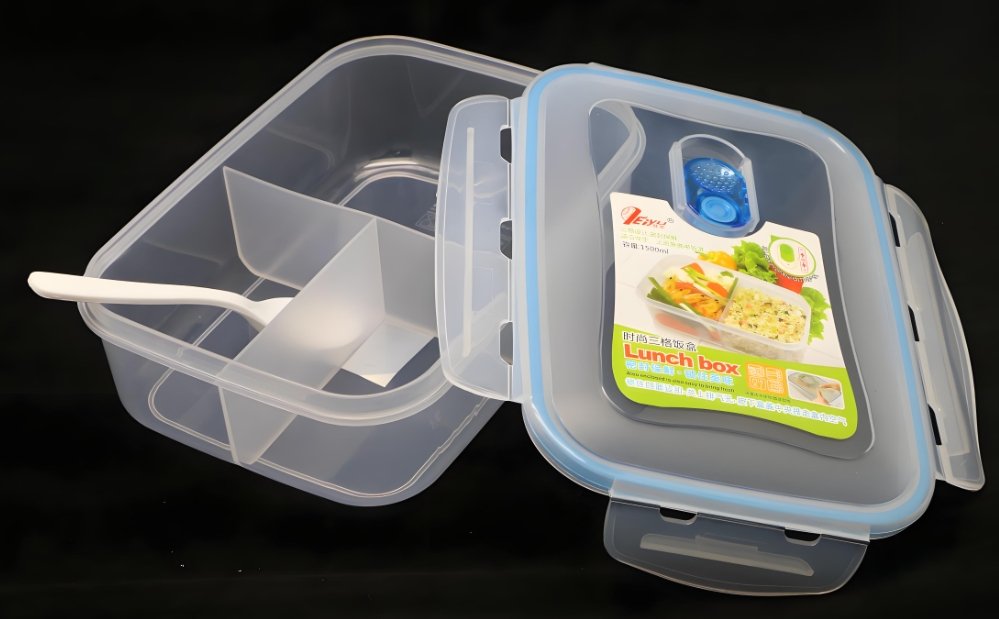

Examples: Food containers, yogurt cups, and storage tubs.
Containers need to be lightweight, durable, and food-safe. Injection molding allows for the production of containers with uniform wall thickness and smooth finishes, which are important for both functionality and aesthetics.
Thin-Walled Packaging Tips From the Mold Maker
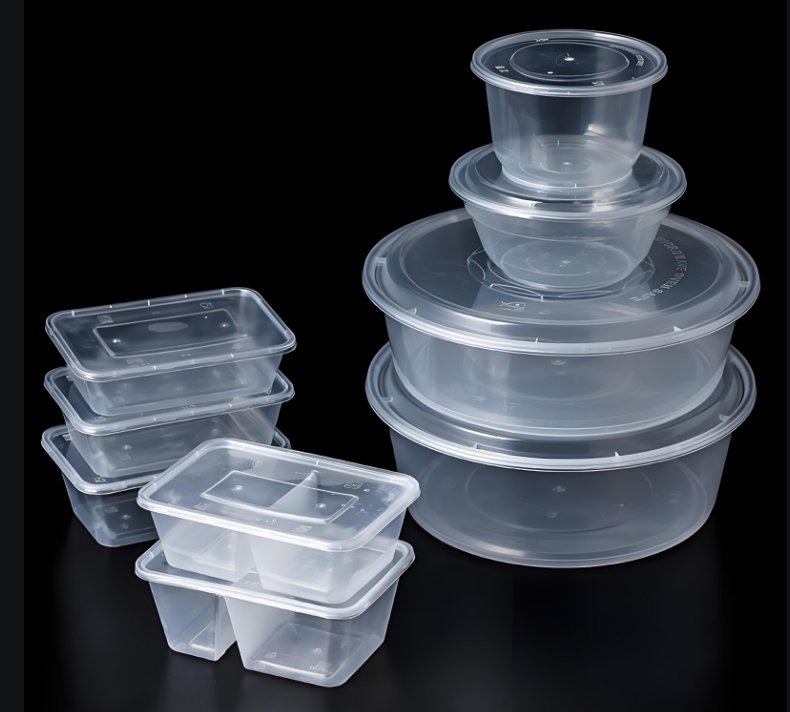
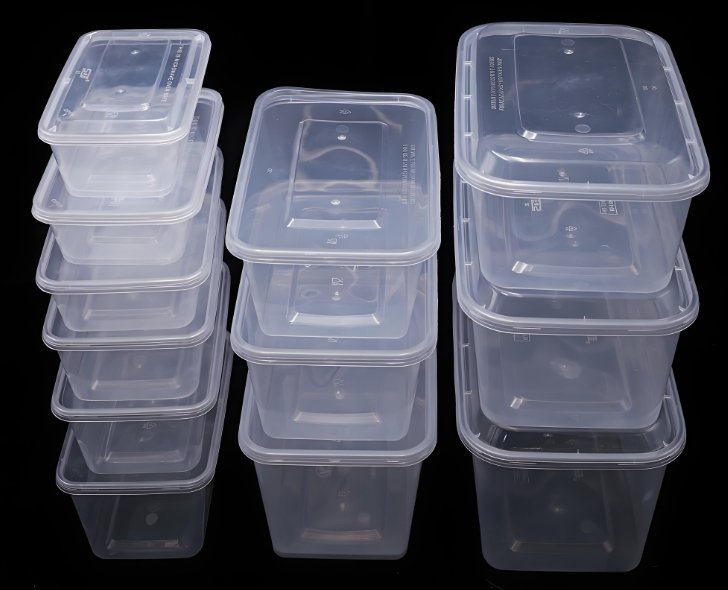
Examples: Disposable cups, trays, and lids.
Thin-walled packaging requires precision in molding to achieve lightweight yet strong components that are cost-effective and easy to produce in large volumes. Injection molding is ideal for creating these thin, uniform structures.
Handles and Grips
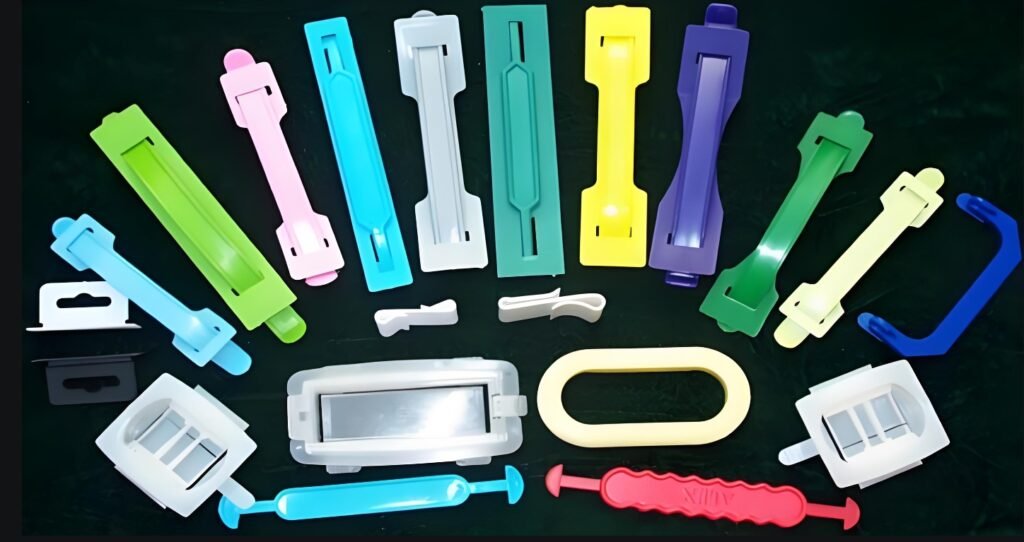
Examples: Handles for jugs, boxes, and other packaging products.
Handles and grips must be ergonomically designed for ease of use and strong enough to support the weight of the product. Injection molding ensures that these components are both durable and comfortable for the user.
Pallets and Crates
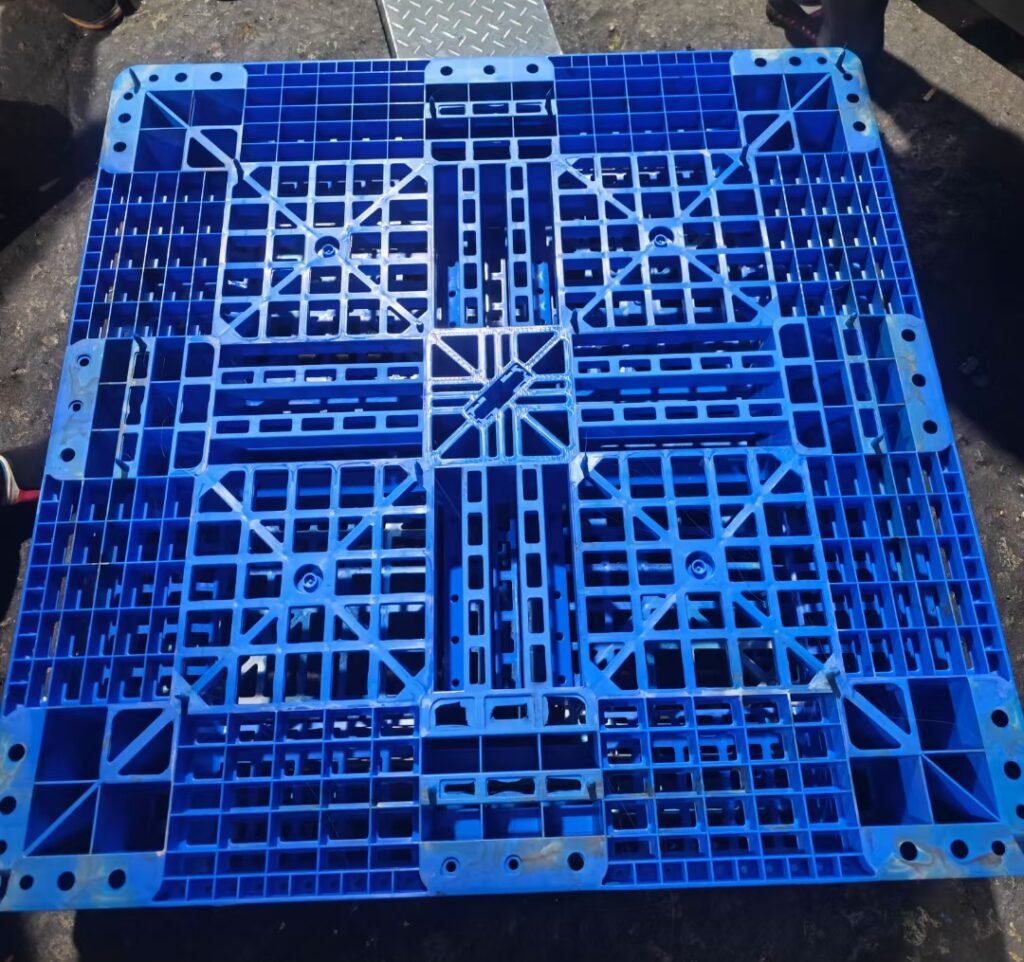
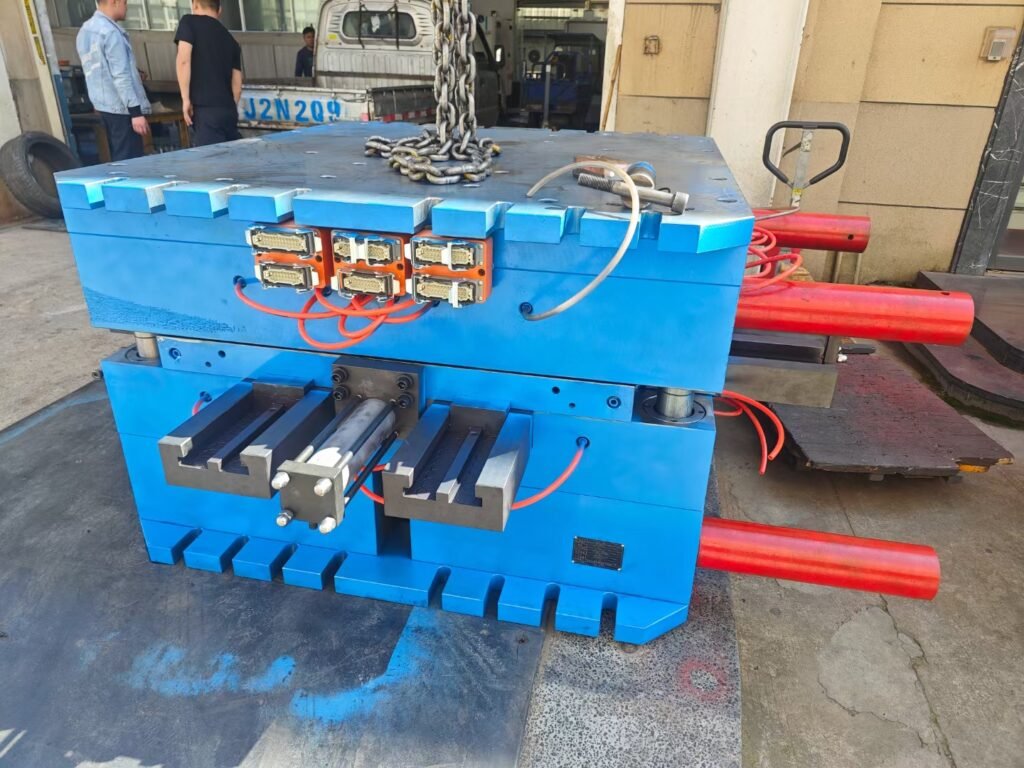
Examples: Reusable plastic pallets and storage crates.
Pallets and crates must be strong enough to carry heavy loads while being lightweight for easier handling. Injection molding produces these parts with consistent strength and durability, suitable for repeated use.
Spouts and Dispensers
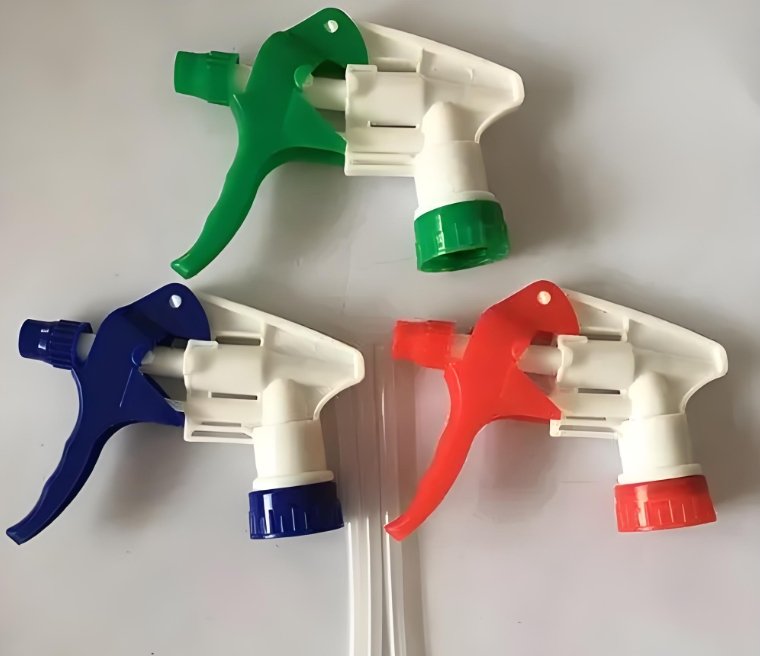
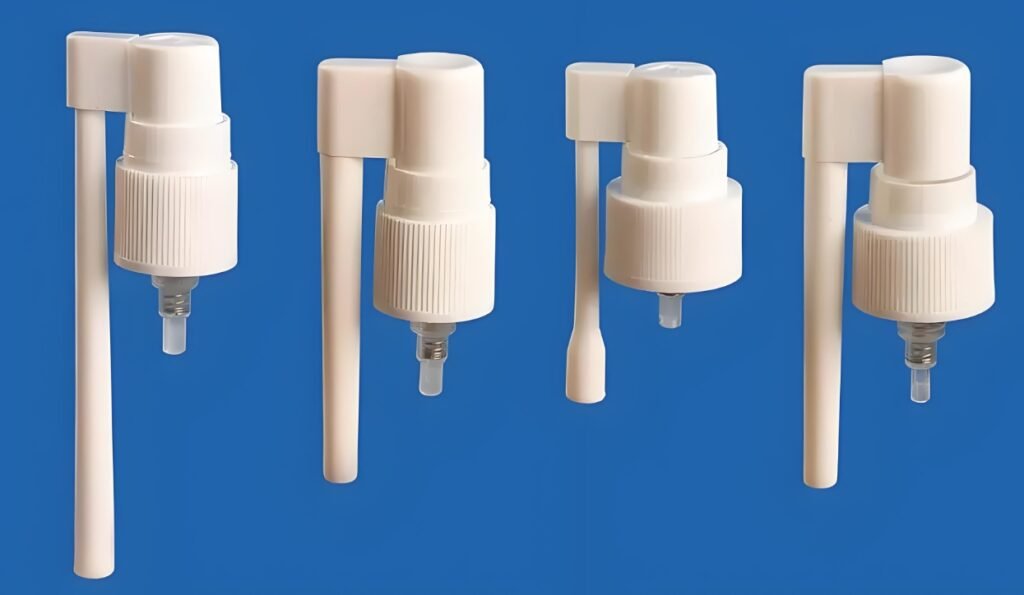
Examples: Spouts for liquid containers, spray nozzles, and pump dispensers.
Spouts and dispensers require precise functionality to control the flow of liquids or sprays. Injection molding ensures that these parts are produced with the necessary precision and quality to perform reliably.
Protective Packaging Components:
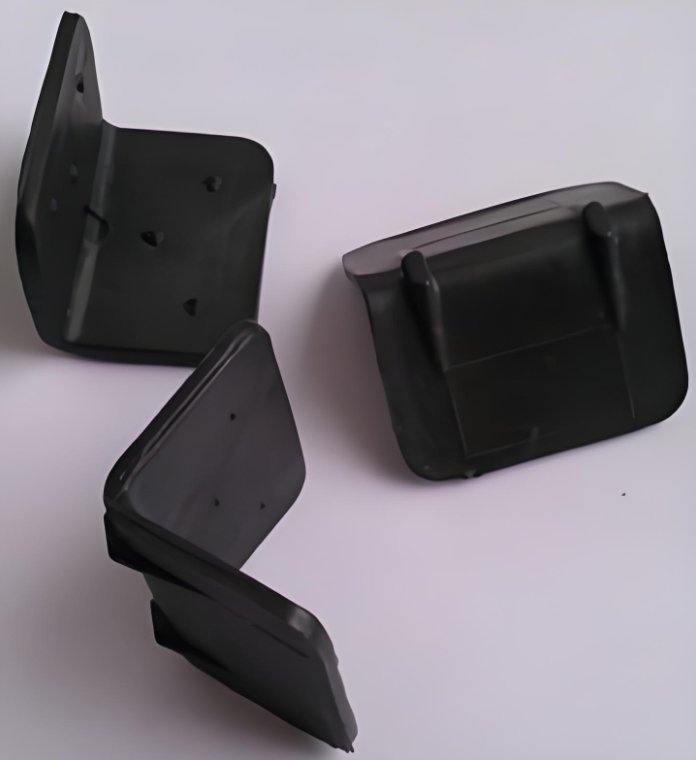
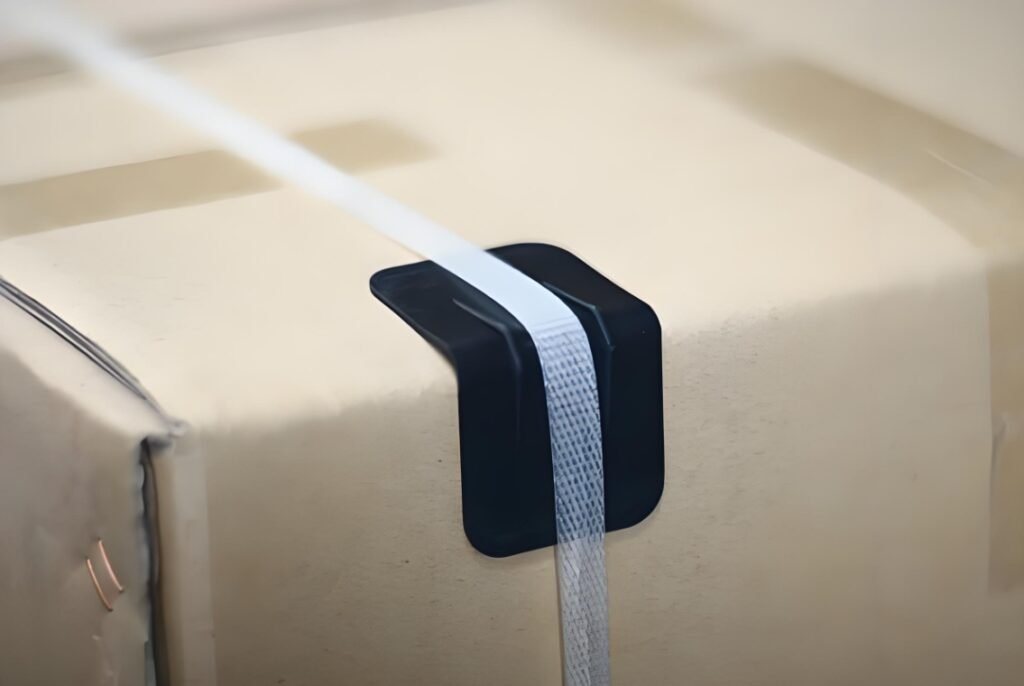
Examples: Corner protectors, edge guards, and cushioning elements.
These components need to absorb impact and protect products during shipping and handling. Injection molding allows for the use of materials that provide the necessary strength and resilience while being lightweight.
Advantages of Injection Molding in the Packaging Sector
High Production Efficiency: Injection molding is well-suited for mass production, allowing for the rapid production of large quantities of packaging components, which is essential in the fast-paced packaging industry.
Precision and Consistency: The ability to produce parts with tight tolerances ensures that packaging components like caps, closures, and containers fit together perfectly, maintaining product integrity.
Material Versatility: A wide range of materials can be used in injection molding, including food-grade and biodegradable plastics, catering to the diverse needs of the packaging industry.
Cost-Effective for High Volumes: Although the initial mold creation is expensive, the cost per unit drops significantly with high-volume production, making injection molding an economical choice for large-scale packaging needs.
Design Flexibility: Injection molding supports complex shapes and intricate designs, allowing for the customization of packaging components to meet specific brand and product requirements.
Lightweight and Durable: Packaging components need to be lightweight to reduce shipping costs but also durable enough to protect the contents. Injection molding provides an excellent balance between these two requirements.
In the packaging industry, injection molding is indispensable for producing a variety of components that meet the demanding requirements for durability, precision, and cost-efficiency.