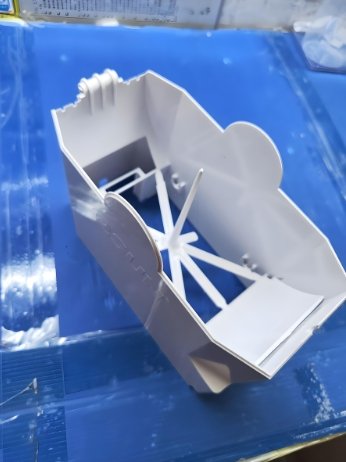
Modern manufacturing is changing fast. As machines become smarter and more connected, maintenance strategies are evolving too. For industries like Electronic Injection Molding, predictive maintenance is no longer just a nice option—it’s a powerful tool that can transform productivity, quality, and cost-efficiency.
For any Mold Maker working in electronics, downtime is costly. A single failure in an injection molding machine can lead to delays, defects, and financial loss. That’s why predictive maintenance is gaining traction. It allows manufacturers to forecast problems before they happen and fix them proactively.
What Is Predictive Maintenance?
Predictive maintenance uses data and smart technology to monitor machine health. Sensors track key parameters like temperature, vibration, pressure, and motor load. Algorithms analyze this data to spot early warning signs of wear or failure. When an issue is predicted, a maintenance alert is sent before the machine breaks down.
In Electronic Injection Molding, this technology is especially valuable. It ensures machines stay running during high-volume, high-precision production. For the Mold Maker, it also means fewer mold defects due to machine instability.
Why Predictive Maintenance Matters in Electronic Injection Molding
1. Reduced Downtime
Downtime is expensive, especially in electronics manufacturing. If a molding machine stops unexpectedly, the entire production line can stall. Products get delayed. Customer satisfaction drops.
Electronic Injection Molding often deals with tight schedules and delicate components. Predictive maintenance helps identify failing components—like heaters, sensors, or hydraulic pumps—before they stop working. The Mold Maker can plan service at the best time, not in the middle of production.
2. Better Part Quality
Inconsistent machine behavior affects part quality. If a molding machine runs with a worn screw or unstable temperature control, defects increase. You might see warping, flashing, or incomplete fills.
By keeping the machine in top condition, predictive maintenance helps maintain part precision. This is critical in Electronic Injection Molding, where tolerances are often within microns. It supports the Mold Maker by ensuring molds perform as designed, without unexpected issues caused by the machine.
3. Longer Equipment Life
Repairing machines reactively can lead to greater damage. For example, running a pump until it fails might harm other parts too. Predictive maintenance prevents this.
Machines used in Electronic Injection Molding are expensive. They run at high speeds and temperatures for long hours. Proactive servicing extends their life. That saves money and reduces the chance of full machine replacement.
How Predictive Maintenance Works
Sensors and Data Collection
Modern injection molding machines come equipped with sensors. These may monitor:
- Hydraulic fluid pressure
- Screw motor torque
- Heater temperatures
- Cycle times
- Cooling efficiency
- Vibration and noise
This data is sent to a central system for analysis.
Data Analysis and Machine Learning
The system uses machine learning to recognize patterns in the data. It learns what “normal” operation looks like. When something starts to drift—such as a rise in vibration or slower cooling—it raises a flag.
In Electronic Injection Molding, this is vital. Small changes can lead to big problems, especially when molding parts for phones, computers, or medical devices. The Mold Maker relies on stable machines to produce accurate parts.
Maintenance Alerts
The system sends alerts to operators, technicians, or managers. These alerts might say, “Hydraulic pump efficiency dropping—check within 20 hours,” or “Barrel heater 3 shows a 10% deviation—possible failure in 48 hours.”
This allows for scheduling service during breaks or shift changes, avoiding downtime during production.
Benefits for the Mold Maker
For the Mold Maker, predictive maintenance offers several benefits:
Mold Protection
Molds are expensive. If a molding machine fails during operation, it could damage the mold cavity or core. For example, poor ejection due to mechanical failure could bend pins or cause cracks.
Predictive maintenance keeps the machine stable. This protects the mold investment and ensures long-term use.
Reduced Scrap
Machine issues lead to rejected parts. That means wasted time, materials, and energy. When the process stays stable, part quality improves. This reduces scrap and lowers production cost.
Process Repeatability
In Electronic Injection Molding, repeatability is key. Customers want consistent results for every part, every batch. Predictive maintenance ensures the machine keeps performing at the same level, which supports mold accuracy and repeatability.
Real-World Applications
Many companies now use predictive maintenance in Electronic Injection Molding:
- Automotive Electronics: Factories producing sensor housings and connectors can’t afford downtime. Predictive tools monitor machines constantly to avoid stoppages.
- Consumer Devices: Makers of smartphones and laptops use predictive analytics to reduce variation and support high-volume production.
- Medical Electronics: Cleanroom molding operations must meet strict standards. Predictive maintenance ensures machines perform reliably and avoid contamination risks.
In each case, the Mold Maker benefits. They receive fewer emergency calls, enjoy better part quality, and support their customers more effectively.
Technologies Enabling Predictive Maintenance
Several tools make predictive maintenance possible in Electronic Injection Molding:
- IoT (Internet of Things): Connects machines to the cloud for live monitoring.
- Edge Computing: Processes data directly at the machine for faster decisions.
- AI and Machine Learning: Helps analyze complex trends and predict failures earlier.
- CMMS (Computerized Maintenance Management Systems): Tracks service schedules and history.
These tools give the Mold Maker and plant manager a complete view of machine health.
Challenges and Solutions
Cost of Implementation
Some companies worry about upfront investment. Sensors, software, and training take time and money. However, the long-term savings from reduced downtime and longer machine life far outweigh the costs.
Data Overload
Too much data can be confusing. That’s why smart algorithms and dashboards are used. They summarize the information clearly so managers and Mold Makers can take quick action.
Integration with Older Machines
Many older machines don’t support IoT. Retrofits are available, allowing sensors to be added and linked to modern systems.
The Future of Maintenance in Injection Molding
Predictive maintenance will continue to evolve. In the future, we may see:
- Self-diagnosing machines that order their own parts
- Voice alerts and mobile app integration
- Full AI-driven maintenance planning
- Predictive tools built into mold design
For the Mold Maker, this means new collaboration with machine suppliers, software developers, and data analysts.
Predictive maintenance is changing how we manage Electronic Injection Molding machines. It turns guesswork into science. It prevents breakdowns, protects molds, and ensures top-quality parts.
Every Mold Maker should embrace this technology. Not only does it protect your molds, but it also helps your customers succeed with fewer delays and better products.
As machines get smarter, maintenance must get smarter too. Predictive systems offer a clear path to more efficient, reliable, and profitable Electronic Injection Molding. The time to adopt this approach is now.