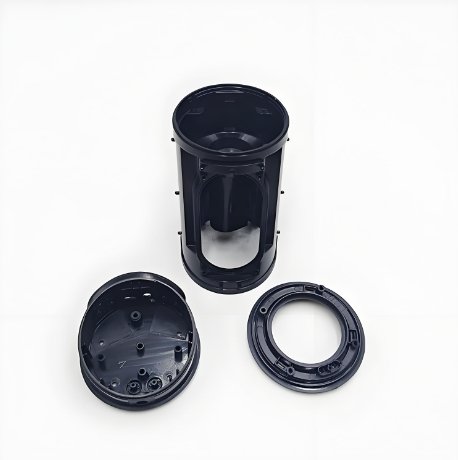
In the competitive world of housing injection molding, quality is everything. Flash—those unwanted thin layers of plastic around parting lines—is a common defect that reduces quality, weakens function, and adds to finishing costs. If left unchecked, flash can damage the appearance and performance of your plastic housing components.
Flash isn’t just an aesthetic issue. It can interfere with the assembly of snap-fit parts, create sharp edges, and result in inconsistent dimensions. That’s why experienced engineers and every mold maker take flash prevention seriously in housing injection molding projects.
This article explains what causes flash, where it appears, and most importantly, how to prevent it. With over 1000 words of practical insight, we’ll help you eliminate flash from your molded housings—starting from design and tooling to process control.
What Is Flash in Housing Injection Molding?
Flash is a thin film of excess plastic that forms where molten material escapes from the cavity of the mold. It typically appears at:
- The parting line between mold halves
- Around ejector pins
- Near slides or lifters
- Gate or runner intersections
In housing injection molding, flash is especially problematic because most housings are meant to fit tightly and look clean. Excess material makes assembly harder and ruins the visual finish.
Why Flash Happens
To prevent flash, you must first understand why it occurs. Several factors contribute to flash:
1. Poor Mold Clamping
If the injection molding machine doesn’t clamp the mold halves tightly enough, plastic can seep between them. This happens when:
- Clamping force is too low
- Mold surfaces are misaligned
- The mold base is worn
In housing injection molding, where parts often have wide surfaces, even slight clamping issues create noticeable flash.
2. Excess Injection Pressure
High injection pressure forces molten plastic into every corner of the mold. If the mold isn’t sealed tightly or if parting lines aren’t precise, pressure will force plastic out. This is one of the top causes of flash.
3. Worn or Damaged Mold
Over time, molds wear down. Parting lines may lose their sharpness. Ejector pins may loosen. Guide pins may not align. A seasoned mold maker always monitors tool wear in housing injection molding operations.
4. Poor Mold Design or Fit
If the mold was not designed with tight tolerances, gaps may exist between shutoffs or inserts. Any small mismatch leads to flash.
5. Temperature Imbalance
Plastic that is too hot flows too easily. It can leak into tiny gaps in the mold. Temperature imbalance also leads to over-packing, which increases flash risk.
The Role of a Mold Maker in Flash Prevention
A professional mold maker plays a vital role in building and maintaining molds that resist flash. Here’s how:
1. Precise Mold Construction
The best defense against flash is a mold built to exact tolerances. Skilled mold makers ensure that shutoffs are tight and surfaces align perfectly. They use precision grinding, high-quality steel, and hardened inserts.
2. Mold Maintenance
Even the best mold degrades with time. Regular inspections and maintenance help detect worn parting lines, damaged ejectors, or misaligned components. A smart mold maker includes mold maintenance in the production plan.
3. Proper Venting
Trapped air causes burn marks and uneven flow, which increases injection pressure and leads to flash. Proper venting designed by the mold maker allows gas to escape without letting plastic leak out.
4. High-Quality Mold Base
In housing injection molding, a strong mold base reduces deflection under pressure. A weak mold frame flexes during clamping, creating space for flash. A good mold maker selects mold bases that match the molding pressure required.
Process Control to Prevent Flash
Even with a perfect mold, process settings greatly affect flash. Here’s what to control:
1. Optimize Clamping Force
The clamp must match the part size and injection pressure. Too little clamping allows flash. Too much wears out the machine and mold. Use the recommended tonnage per square inch of projected area and increase slightly if needed.
2. Adjust Injection Pressure and Speed
If injection is too fast or too forceful, the melt forces its way into gaps. Slowing the fill speed and reducing pressure can prevent this. Start with lower settings and increase only when necessary.
3. Monitor Melt Temperature
Overheated plastic is more likely to flash. Use the correct melt temperature for your material and control heater bands and screw settings precisely. Cooling imbalances can also lead to inconsistent shrinkage, increasing the risk of flash.
4. Balance Flow Paths
Uneven flow can cause one side of the mold to fill before the other. This imbalance may force open shutoffs on the unfilled side. Use mold flow simulation to design gates and runners that promote even filling.
Design Tips to Reduce Flash Risk
Sometimes flash is caused by part design. Here are key tips to avoid it:
1. Add Proper Draft
Undercuts and straight walls resist ejection. This can pull or shift mold components during ejection, causing flash. Use a minimum of 1–2 degrees of draft on vertical walls to ease part release.
2. Avoid Sharp Corners at Shutoffs
Sharp corners tend to wear down faster, allowing flash over time. Use radii and clean transitions in shutoff zones.
3. Simplify Parting Line Location
If possible, keep the parting line in simple, flat regions. Avoid placing it across curved or highly detailed areas, where sealing becomes harder.
4. Collaborate with the Mold Maker Early
Involve your mold maker at the design stage. They’ll suggest improvements that make your housing design easier to mold and less prone to flash.
Detection and Correction
If flash starts appearing, take immediate action:
- Inspect the mold for wear
- Check clamp force calibration
- Lower injection pressure and melt temperature
- Run a mold fill analysis
- Contact the mold maker for detailed inspection
In housing injection molding, flash can appear suddenly due to a small shift or buildup. Constant vigilance is needed to catch it early.
Conclusion
Flash in plastic housings can damage product quality and increase manufacturing costs. Preventing flash requires a combination of good mold design, accurate process control, and continuous mold maintenance.
Here’s a quick checklist to prevent flash:
- Use a skilled mold maker to build precision molds
- Ensure proper mold venting, shutoff design, and alignment
- Monitor injection pressure, melt temperature, and clamping force
- Design parts with good draft and parting lines
- Regularly inspect and maintain your molds
With these strategies, your housing injection molding projects can stay flash-free, delivering clean, strong, and functional housings. Trust your mold maker, invest in quality, and stay proactive in your process control.